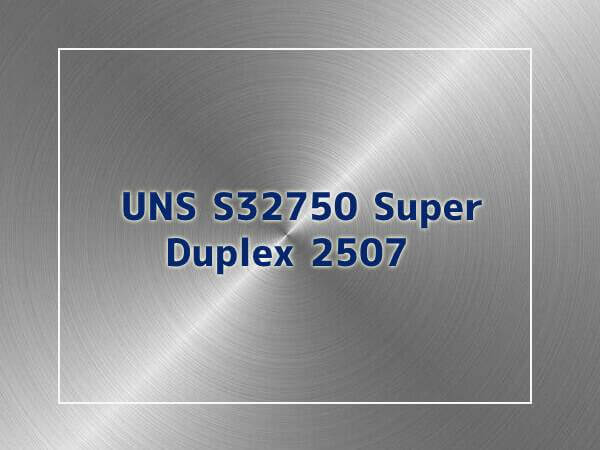
UNS S32750 is a super duplex stainless steel designed for applications that demand exceptional strength and corrosion resistance. Super Duplex stainless UNS S32750 is a mixed microstructure of austenite and ferrite (50/50) which has improved strength over ferritic and austenitic steel grades. Super Duplex has a higher molybdenum and chromium content which gives the material greater corrosion resistance than standard duplex grades.
UNS S32750 is duplex stainless steel specially designed for service in aggressive chloride-containing environments. It has good resistance to localized corrosion and stress corrosion cracking in combination with high mechanical strength. It is widely used in oil & gas, hydropower, pressure vessels, pulp & paper, structural components and chemical tankers. Like other duplex (ferritic/austenitic) grades the super duplex grades are unsuitable for high or low-temperature service. UNS S32750 is not recommended for temperatures below -50°C or above +300°C, because of reduced toughness outside this range.
UNS S32750 Chemical Composition
The Chemical Composition of UNS S32750 consists of 24-26% chromium, 3-5% molybdenum, and 6-8% nickel. This high molybdenum, chromium and nitrogen contents provide excellent resistance to chloride pitting and crevice corrosion attack and the duplex structure provides 2507 with exceptional resistance to chloride stress corrosion cracking.
Alloy | C | Si | Mn | P | Cr | Ni | N | Mo | S | Cu | Fe |
---|---|---|---|---|---|---|---|---|---|---|---|
S32750 | 0.03 | 0.8 | 1.2 | 0.035 | 24.0-26.0 | 6.0-8.0 | 0.24-0.32 | 3.0-5.0 | 0.02 | 0.5 | Bal |
UNS S32750 Mechanical Properties
Tensile Strength, Mpa (Ksi), Min | Yield Strength, MPa (Ksi), Min | Elongation, %, Min | Hardness, Brinell HB |
---|---|---|---|
795 (116) | 550 (80) | 15 | 310 Max |
Duplex S32750 possesses excellent mechanical properties. Often a light gauge of S32750 material can be used to achieve the same design strength of a thicker nickel alloy. The resulting savings in weight can dramatically reduce the overall cost of fabrication.
UNS S32750 Equivalent
- EN X2CrNiMoN25-7-4
- ASTM 2507
- DIN 1.4410
- A182 f53
UNS S32750 Physical Properties
Physical Properties | Data |
---|---|
Density (Kg/m3) | 7810 |
Magnetic Permeability (20°C) | 33 |
Young’s Modulus (kN/mm2) | 199 |
Specific Electrical Resistance, 20°C (µΩ.m) | 0.8 |
Mean coefficient of thermal expansion, 20-300°C (m/m/oC) | 11.1 x 10-6 |
Specific Heat, 20°C (J/kg.K) | 475 |
Thermal conductivity, 20°C (W/m.K) | 14.2 |
Forms
- ASTM A240 UNS S32750 Plate
- ASTM A790 UNS S32750 Pipe
- ASTM A789 UNS S32750 Tube
- ASTM A815 UNS S32750
- ASTM A926 UNS S32750
- ASTM A479 UNS S32750
UNS S32750 Properties
- Super duplex grade with the combination of properties given by austenitic and ferritic structure
- High mechanical strength.
- High resistance to stress corrosion cracking in halide-containing environments.
- High resistance to pitting and crevice corrosion.
- High resistance to general corrosion.
- High resistance to erosion corrosion and corrosion fatigue.
- Good weldability and workability
- Low rate of thermal expansion
- Suggested for applications up to 600° F
Corrosion Resistance
2507 is very highly resistant to general corrosion and to pitting and crevice corrosion in high chloride, hot environments. Its duplex structure also results in excellent resistance to stress corrosion cracking.
2507 Duplex is highly resistant to uniform corrosion by organic acids such as formic and acetic acid. It is also highly resistant to inorganic acids, especially if they contain chlorides. Alloy 2507 is highly resistant to carbide-related intergranular corrosion. Due to the ferritic portion of the duplex structure of the alloy it is very resistant to stress corrosion cracking in warm chloride-containing environments. Through additions of chromium, molybdenum and nitrogen localized corrosion such as pitting and crevice attack are improved. Alloy 2507 has excellent localized pitting resistance.
2507 has excellent general corrosion resistance, superior to virtually all other stainless steels. It has high resistance to intergranular corrosion and very high resistance to stress corrosion cracking in both chloride and sulfide environments.
Welding
Alloy S32750 is readily weldable using many of the standard electric arc welding processes but oxyacetylene welding is not recommended because carbon pickup in the weld metal may occur.
2507 possesses good weldability and can be joined to itself or other materials by shielded metal arc welding (SMAW), gas tungsten arc welding (GTAW), plasma arc welding (PAW), flux cored wire (FCW), or submerged arc welding (SAW). 2507/P100 filler metal is suggested when welding 2507 because it will produce the appropriate duplex weld structure
Heat Treatment
Alloy S32750 should be solution annealed and quenched after either hot or cold forming. Solution annealing should be done at 1040 – 1120°C.
Annealing should be followed immediately by a rapid air or water quench. To obtain maximum corrosion resistance, heat-treated products should be pickled and rinsed.
Duplex and super duplex grades cannot be hardened by thermal treatment.
Typical Applications
- Desalination plants
- Industrial piping
- Scrubbers
- Tubes for oil and gas applications
- Deep-sea pipelines
- Flanges and valves
Disadvantages of UNS S32750
- Higher cost: Compared to other stainless steel materials, UNS S32750 is more costly.
- Welding requires special techniques: Due to its special material properties, welding UNS S32750 requires special processes and techniques, otherwise it is prone to form heat-affected zones, affecting the welding quality.
- Sensitivity to hydrogen: UNS S32750 is sensitive to hydrogen, which may limit its use in certain applications (e.g. hydrogen storage, oil, gas, etc.).
UNS32750, 1.4410 Chemical Comparison
Standard | Grade | C | Mn | Cr | Ni | Mo | N |
---|---|---|---|---|---|---|---|
ASME II A SA-240 | UNS S32750 | ≤0.030 | ≤1.20 | 24.0-26.0 | 6.00-8.00 | 3.00-5.00 | 0.24-0.32 |
ASTM A240 | UNS S32750 | ≤0.030 | ≤1.20 | 24.0-26.0 | 6.0-8.0 | 3.0-5.0 | 0.24-0.32 |
EN 10028-7 | 1.4410 | ≤0.030 | ≤2.00 | 24.00-26.00 | 6.00-8.00 | 3.00-4.50 | 0.20-0.35 |
EN 10088-2 | 1.4410 | ≤0.030 | ≤2.00 | 24.0-26.0 | 6.0-8.0 | 3.0-4.5 | 0.24-0.35 |
EN 10088-3 | 1.4410 | ≤0.030 | ≤2.00 | 24.0-26.0 | 6.0-8.0 | 3.0-4.5 | 0.24-0.35 |
EN 10088-4 | 1.4410 | ≤0.030 | ≤2.00 | 24.0-26.0 | 6.0-8.0 | 3.0-4.5 | 0.24-0.35 |
Related References
- ASTM A789, ASME SA789 – Seamless and Welded Ferritic/Austenitic Stainless Steel Tubing for General Service
- ASTM A790, ASME SA790 – General Requirements for alloy and Stainless Steel Pipe
- ASTM A240/ASME SB240, Standard Specification for Chromium and Chromium-Nickel Stainless Steel Plate, Sheet, and Strip for Pressure Vessels and for General Applications
- ASTM A480, Standard Specification for General Requirements for Flat-Rolled Stainless and Heat-Resisting Steel Plate, Sheet, and Strip
- EN 10088-2, Stainless steels. Technical delivery conditions for sheet/plate and strip of corrosion-resisting steels for general purposes
- EN 10088-3, Stainless steels. Technical delivery conditions for semi-finished products, bars, rods, wire, sections and bright products of corrosion-resisting steels for general purposes
- EN 10088-4, Stainless steels. Technical delivery conditions for sheet/plate and strip of corrosion-resisting steels for construction purposes
- EN 10088-5, Stainless steels. Technical delivery conditions for bars, rods, wire, sections and bright products of corrosion-resisting steels for construction purposes
- ASTM A249, Standard Specification for Welded Austenitic Steel Boiler, Superheater, Heat-Exchanger, and Condenser Tubes
- ASTM A213, Standard Specification for Seamless Ferritic and Austenitic Alloy-Steel Boiler, Superheater, and Heat-Exchanger Tubes
- ASTM A312, Standard Specification for Seamless, Welded, and Heavily Cold Worked Austenitic Stainless Steel Pipes