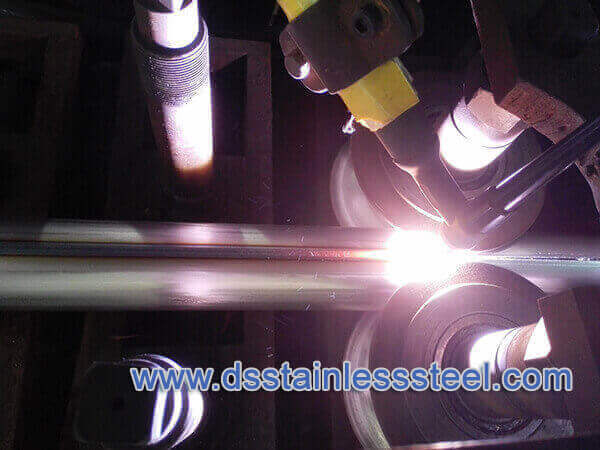
TIG welding (Tungsten Inert Gas Welding) is the most common method for welding stainless steel, whether manual or automatic welding, argon can be effectively isolated from the surrounding air which itself is not dissolved in the metal, and no metal reaction; the arc in the process of tungsten argon arc welding and automatic removal of the role of the surface oxide film.
Argon arc welding according to the different electrode materials can be divided into tungsten argon arc welding (non-melting pole) and fusion pole argon arc welding. According to its operating method can be divided into manual, semi-automatic and automatic tig welding. The power supply can be divided into DC tig welding, AC tig welding and pulse tig welding.
Argon Protected Welding
Argon arc welding is a welding technique that uses argon as a shielding gas. Also known as argon gas shielding welding. It is to pass argon protective gas around the arc welding to isolate the air outside the weld zone and prevent oxidation of the weld zone.
Argon arc welding technology is based on the principle of ordinary arc welding, the use of argon gas to protect the metal welding consumables, through the high current so that the welding consumables in the welded base material melted into a liquid state to form a molten pool, so that the welded metal and welding consumables to achieve metallurgical bonding of a welding technology, due to the high-temperature molten weld constantly fed with argon, so that the welding consumables can not be contacted with the oxygen in the air, which prevents the oxidation of the welding consumables, and can therefore be welded stainless steel, iron metal hardware metal.
A type of tungsten inert gas shielded welding (TIG). Is under the protection of argon gas, the use of arc heat to melt the base material and filler wire to form a joint welding method. Mainly control the welding current, welding speed, and argon flow three parameters. Compared with manual welding, the arc and the molten pool are visible, easy to operate; and can be welded to the active metal of the thin plate structure; weld quality is good, and the joint strength is up to 80% to 90% of the base material.
Protective Gas
The most commonly used inert gas is argon. It is a colorless, odorless gas with a content of 0.935% (by volume) in air. The boiling point of argon is -186°C, which is between the boiling points of oxygen and helium. Argon is a by-product of the fractionation of liquid air to produce oxygen in oxygen plants.
Argon is an ideal shielding gas, 25% denser than air, which is good for welding arc protection and reduces the consumption of shielding gas in flat welding. Argon is a very chemically inactive gas, even at high temperatures, but also does not have a chemical reaction with the metal, so there are no alloying elements oxidized and burned and the resulting series of problems. Argon is also insoluble in liquid metal and thus does not cause porosity. Argon is a monoatomic gas, the atomic state exists, at high temperatures without molecular decomposition or atomic heat absorption phenomenon. The specific heat capacity of argon and heat conduction capacity is small, that is, its own absorption is small, outward heat transfer is also less, the heat in the arc is not easy to dissipate, so the welding arc combustion is stable, heat concentration, conducive to the welding process.
TIG Welding Stainless Steel Process
operating rules and regulations
- Argon arc welding must be operated by a person switch.
- Check the equipment before work, tools are good.
- Check the welding power supply, the control system is grounded, the transmission part of the lubricating oil. The rotation should be normal, argon gas, water must be unobstructed. If there is a leak, you should immediately notify the repair.
- Check whether the welding gun is normal, whether the ground is reliable.
- Check whether the high-frequency arc system, welding system is normal, wire, cable joints are reliable, for automatic wire pole argon arc welding, but also check the adjustment mechanism, wire feeding mechanism are intact.
- According to the material of the workpiece choose the polarity, connect the welding circuit, general material with DC positive connection, for aluminum and aluminum alloy with reverse connection method or AC power supply.
- Check whether the welding bevel is qualified, the bevel surface shall not have oil, rust, etc., in the weld on both sides of 200mm to remove oil and rust.
- For the use of tire tools to check the reliability of the weldments that need to be preheated, but also check the preheating equipment, and temperature measuring instruments.
- The argon arc welding maneuvering button shall not be far from the arc, so that in the event of failure can be closed at any time.
- The use of high-frequency arc must be frequently checked for leakage.
- Equipment failure should be shut down for maintenance, the operation of the workers shall not repair themselves.
- In the vicinity of the arc, to bare body and other parts of the bare storm, not allowed to smoke near the arc, eating, so as to avoid ozone, and smoke inhalation.
- Grinding thorium tungsten pole must wear a mask, and gloves, and comply with the operating procedures of the sander. The best choice of cerium tungsten electrode (less radiation). The sander must be equipped with an air extraction device.
- The operator should always wear static dust mask. Operate to minimize the high-frequency electric action time. Continuous work shall not exceed 6 hours.
- Argon arc welding workplace must be air circulation. Ventilation and detoxification equipment should be opened during work. Ventilation device failure, should stop working.
- Argon gas bottles are not allowed to hit the smash, the stand must have bracket, and be away from open flames of more than 3 meters.
- In the container inside the argon arc welding, should wear a special mask to reduce the inhalation of harmful fumes. Outside the container should be set up to monitor and cooperate.
- Thorium tungsten rods should be stored in the lead box to avoid injury due to a large number of thorium tungsten rods concentrated together, the radioactive dose exceeds the safety regulations.
Wire feeding: Subdivision of internal filler wire and external filler wire.
External filler wire can be used for bottoming and filling, is a larger current, its wire head in the front of the bevel, the left-hand pinched wire, and constantly fed into the molten pool for welding, the bevel gap requires a small or no gap.
Its advantage is that because of the high current, and the gap is small, so the production efficiency is high, the operation skill is easy to master. The disadvantage is used for bottoming words because the operator can not see the blunt edge of the melting and the reverse side of the residual high situation, so easy to produce not fused and do not get the ideal reverse side of the molding.
Filling wire can only be used for bottoming welding, is the left thumb, index or middle finger with the wire feeding action, pinky and ring finger clamp the wire to control the direction of the wire, the wire is close to the inside of the bevel at the blunt edge, and the blunt edge with the melting of the weld, the requirements of the bevel gap is larger than the diameter of the wire, is a plate, then you can bend the wire into an arc.
Its advantages because the wire on the reverse side of the bevel, you can clearly see the blunt edge and the melting of the wire, the afterglow of the eyes can also see the reverse side of the residual height of the situation, so the weld fusion is good, the reverse side of the residual height and not fused can be well controlled. The disadvantage is that it is difficult to operate, requiring the welder to have more skillful operating skills, because the gap is large, so the amount of welding has to be increased accordingly, the gap is large, so the current is low, and the efficiency is slower than the outer filler wire.
Welding handles are categorized into shaking handles and mopping handles.
Shaking the welding nozzle is slightly pressed on the welding seam, arm greatly shaking for welding. Its advantages because the welding nozzle pressed on the weld, the welding handle in the running process is very stable, so the weld protection is good, good quality, the appearance of the formation is very beautiful, the product qualification rate is high, especially the weld is very easy to weld the back weld, weld stainless steel can be obtained when the color of the appearance is very beautiful. The disadvantage is that it is difficult to learn, because the arm shaking amplitude, so can not be in an obstacle to the welding.
The mop is the welding nozzle gently leaning or not leaning on the top of the weld, the right hand little finger or ring finger is also leaning or not leaning on the workpiece, and the arms swing is small, dragging the welding handle for welding. Its advantage is easy to learn, and good adaptability, the disadvantage is that the shape and quality are not as good as shaking the handle, especially upward welding without shaking the handle to facilitate welding, welding stainless steel makes it difficult to get the ideal color and shape.
Arc
the arc is generally used arc inducer (high-frequency oscillator or high-frequency pulse generator), the tungsten electrode and the weldment does not touch the arc, there is no arc inducer when the arc is used to contact the arc , can be used in copper or graphite placed on the weldment bevel to induce the arc, but the method is more troublesome, the use of fewer, generally with the wire gently scratching the weldment and tungsten electrode and the tungsten electrode directly short-circuited and quickly disconnect and ignite the arc.
Welding
After the arc is ignited, it should be preheated for 3-5 seconds at the beginning of the weldment to form a molten pool and then start feeding the wire. When welding, the angle of the welding torch should be appropriate, and the wire should be fed evenly. Welding gun forward movement should be smooth, the left and right swing is a little slower on both sides, and slightly faster in the middle. To pay close attention to the changes in the melt pool, the melt pool becomes larger, wider weld or concave, to speed up the welding speed or re-adjust the welding current. When the molten pool fusion is not good and send wire sends the feeling of immobility, to reduce the welding speed or increase the welding current, if it is the bottoming of the welding gaze should be focused on the bevel of the two sides of the blunt edge of the eye of the eye of the afterglow in the seam on the opposite side, pay attention to the rest of the high changes.
End the Arc
If the direct arc is easy to produce shrinkage holes, if there is an arc inducer torch to intermittent arc or adjust the arc current to the appropriate arc slow arc, such as there is no arc inducer welding machine will slow the arc to the side of the bevel, do not produce shrinkage holes, such as shrinkage holes to be polished clean before welding.
Close the arc if it is in the joints, should be the first to be joints polished into a beveled mouth, to be fully melted joints and then welded forward 10-20mm and then slowly close the arc, do not produce shrinkage holes. Often seen in the production of joints do not grind into a beveled mouth, directly lengthen the joint welding time for joints, which is a very bad habit, so that the joints are prone to concave, joints are not fused and the opposite side of the disjointed impact on the molding of the aesthetic, such as high alloy materials are also prone to cracks.
After welding to check the appearance of the qualified, people go off the power and gas!
Features
High current density, concentrated heat, high deposition rate, fast welding speed. In addition, it is easy to lead the arc. Need to strengthen the protection because of the strong arc of light, and smoke, so to strengthen the protection.
Advantages of TIG Welding
- Argon protection can be isolated from the air oxygen, nitrogen, hydrogen and other adverse effects on the arc and the molten pool, reduce the alloying elements of the burn, in order to get dense, no spatter, high-quality welded joints;
- Argon arc welding arc combustion stability, heat concentration, high arc column temperature, high welding productivity, narrow heat-affected zone, welded weldments stress, deformation, crack tendency is small;
- Argon arc welding for open arc welding, operation, observation and convenience;
- Eectrode loss is small, the arc length is easy to maintain, welding without flux, and coating layer, so it is easy to realize mechanization and automation;
- Argon arc welding can weld almost all metals, especially some refractory metals, easy-to-oxidize metals, such as magnesium, titanium, molybdenum, zirconium, aluminum and its alloys;
- Not subject to the position of the weldment position limitations, can be all-position welding.
Safety regulations
- Welding workplace must be equipped with fire prevention equipment, such as sand box, fire extinguisher, fire hydrant, water bucket, etc.. Flammable items shall not be less than 5m away from the welding place. if it is impossible to meet the specified distance, it can be properly covered with asbestos sheet, asbestos cloth, etc. to prevent sparks from falling into the flammable items. Explosive substances from the welding shall not be less than 10 m. Argon arc welding workplace should have good natural ventilation and fixed mechanical ventilation devices to reduce the hazard of argon arc welding harmful gases and metal dust.
- Manual tungsten arc welding machine should be placed in a dry ventilated place, in strict accordance with the instructions for operation. Before use should be a comprehensive inspection of the welding machine. Determine that there are no hidden dangers, and then turn on the power. No-load operation is normal before welding. Ensure that the welding machine is wired correctly, must be good, solid grounding to ensure safety. Welder power on and off by the power board on the switch control, it is strictly prohibited load trigger switch, so as to avoid shape contact burns.
- Should always check the argon arc welding gun cooling water system work, found clogged or leaking should be resolved immediately to prevent burning the gun and affect the welding quality.
- Welding personnel to leave the workplace or the welder is not in use, must cut off the power supply. If the welder fails, should be maintained by professionals, maintenance should be done to prevent electric shock and other safety measures. The welding machine should be dusted and cleaned at least once a year.
- Tungsten argon arc welding machine high-frequency oscillator generated by the high-frequency electromagnetic field will make people produce a certain amount of dizziness, fatigue. Therefore, welding should minimize the time of the role of high-frequency electromagnetic fields, ignite the arc immediately after cutting off the high-frequency power supply. Welding gun and welding cable should be shielded with soft metal braid outside (one end of the hose is connected to the welding gun, the other end is grounded, and the outside is not wrapped with insulation). If possible, should try to use crystal pulse arc instead of high-frequency arc.
- Argon arc welding, ultraviolet light intensity is very large, easy to cause photophthalmia, arc burns, while producing ozone and nitrogen oxides stimulate the respiratory tract. Therefore, welders should wear white canvas overalls when operating, wear a good mask, face mask and protective gloves, foot cover, etc. To prevent electrocution, the ground near the workbench should be covered with insulating rubber, and the staff should wear insulating rubber shoes.
TIG Welding Stainless Steel Pipe
DONGSHANG STAINLESS produces TIG welding stainless steel pipe for boilers, heat exchangers, condensers and other general service purposes, with excellent performance in corrosive environments. Stainless steel grades mainly have 304, 304L, 316 316L, 321, 2205, 310S.
TIG welding stainless steel pipe wall thickness ranges from 0.5 to 4.0 mm, tubes are produced without adding filler metal, welding two strip edges, TIG welding process provides high-quality welding, after heat treated solution, welding bend is integrity with base metal.
We use automatic TIG welding to manufacture stainless steel tubing, specifications cover ASTM A249, A269, A312, A554, A789, A790, and equivalent EN/DIN standards, various tubing forms and shapes are using TIG welding process, such as round tube, and rectangular tube, square tube, oval tubing, and U bend tube.