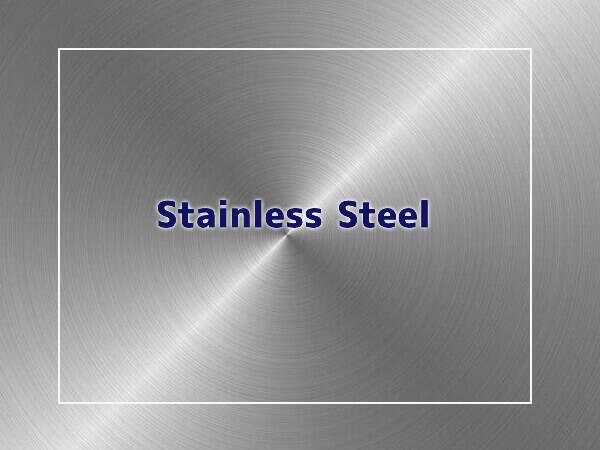
Stainless Steel is usually involved when we talk about metallic materials, stainless steel plays an important role in the metal world, and stainless steel possesses unique characteristics and properties to make it the most popular metal. Stainless steel is resilient and versatile. It is exceptionally strong, durable, scratch-resistant, and does not rust, corrode, or stain easily. It is also easy to clean and sterilize, these benefits make stainless steel suitable for use in many applications and harsh environments.
Stainless steel (SS) is an excellent metal-based material alternative to carbon-based materials due to its outstanding mechanical properties, electrical conductivity, and corrosion resistance. Applying stainless steel from modern buildings’ facades to artistic creations and critical applications such as nuclear reactors.
- What Is Stainless Steel?
- Stainless Steel Composition
- How Stainless Steel Is Made?
- Types Of Stainless Steel
- Stainless Steel Grades
- 304 Stainless Steel
- 304L Stainless Steel
- 316L Stainless Steel
- 321 Stainless Steel
- 904L Stainless Steel
- 430 Stainless Steel
- 444 Stainless Steel
- 409 Stainless Steel
- 439 Stainless Steel
- 441 Stainless Steel
- 436 Stainless Steel
- 446 Stainless Steel
- 410 Stainless Steel
- 420 Stainless Steel
- 431 Stainless Steel
- 440 Stainless Steel
- 2205 Duplex Steel
- AISI Stainless Steel
- Stainless Steel Properties
- Stainless Steel Finishes
- Advantages of Stainless Steel
- Stainless Steel Products
- Stainless Steel Applications
- Stainless Steel Elements
What Is Stainless Steel?
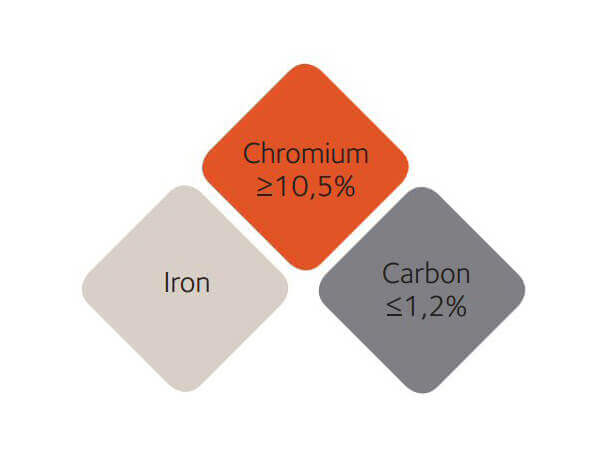
Stainless steel is an iron alloy with a minimum of 10.5% chromium content, and a maximum of 1.2% carbon (by weight), the chromium in the alloy is an essential element to form a passive film on oxidation when exposed to air, this layer acts as a shield against further corrosion essentially making the alloy rustproof, the film is rapidly self-repairing in the presence of oxygen, this characteristic makes stainless steel highly resistant to rust and corrosion, even in harsh environments. There are five types of stainless steel groups with over 100 stainless steel grades, each grade has a unique composition and properties to meet the application, and the grades adding the chemical element enhance the properties.
Stainless Steel Composition
Stainless steel composition is composed of iron, carbon, and chromium, chromium is a key element of stainless steel, and its content is usually between 10 and 30 percent. The main function of chromium is to form a dense chromium oxide film on the steel surface, thus improving the corrosion resistance of stainless steel. In addition to chromium, stainless steel contains small amounts of other elements, including molybdenum, nickel, manganese, etc. Molybdenum can improve the corrosion resistance of stainless steel. stainless steel elements may include the following:
- Nickel
- Chromium
- Manganese
- Molybdenum
- Silicon
- Titanium
- Copper
- Carbon
- Nitrogen
The addition of different chemical elements can impact and alter stainless steel characteristics, such as formability, ductility and cryogenic toughness properties, and improve performance in strength and corrosion resistance. The chemical compositions for some commonly used austenitic, ferritic, martensitic, and duplex stainless steels are provided in the following based on ASTM standards.
Stainless Steel Composition Chart
How Stainless Steel Is Made?
- Melting: raw materials such as iron, nickel, chromium, manganese and other metals are mixed in proportion and melted in a blast furnace to produce pig iron.
- Steelmaking: pig iron is added to the steelmaking furnace to remove impurities through the action of oxidizers, and at the same time control the content of chromium, nickel and other alloying elements to produce a billet that meets the requirements of a specific stainless steel composition.
- Hot rolling: the refined billet is heated to the appropriate temperature, and then hot rolled through the rolling mill to obtain hot rolled sheet.
- Pickling: the hot rolled sheet is put into the pickling tank for pickling, to remove the surface of the oxide skin and rust layer, so that the surface is more smooth and clean.
- Cold rolling: the pickled plate is heated to the appropriate temperature again, and then cold rolled by the rolling mill to get the cold rolled plate. After cold rolling, the surface of the plate is smooth, the dimensional accuracy is high, and the strength, hardness and wear resistance are improved.
- Annealing: the cold rolled sheet is heated to the appropriate temperature and annealed to eliminate the residual stress in the sheet and improve the plasticity and toughness.
- Finished product processing: the annealed sheet is cut and molded according to the need to get the final product.
General steps in stainless steel manufacturing include melting, casting, forming, heat treatment/annealing, descaling, cutting, and finishing. In the whole process, it is also necessary to carry out a number of refining and adjustments, such as the use of a refining agent in the refining furnace to remove oxygen, blowing into the inert gas – argon, to reduce the content of carbon and sulfur, and at the same time adjust the chemical composition. In addition, there are specific smelting technologies and equipment such as electric arc furnace smelting, vacuum oxygen decarburization (VOD), and argon oxygen decarburization (AOD).
To summarize, stainless steel smelting is a multi-stage, stainless steel production is a complex and delicate process involving multiple steps and different technical means. The above is the basic process of stainless steel smelting.
Types Of Stainless Steel
Stainless steels are classified into five major groups in the family of stainless steels according to metallurgical microstructure, Austenitic stainless steels, Ferritic stainless steels, Martensitic Stainless Steels, Duplex stainless steels and Precipitation-hardening stainless steels, there are more than 100 grades of stainless steel, each grade consists of Nickel and Chromium chemical composition percentage with unique properties and functions.
There are five types of stainless steel depending on their metallurgical microstructure, each group has particular alloying elements and composition that will affect stainless steel properties and uses.
- Austenitic stainless steels
- Ferritic stainless steels
- Martensitic stainless steels
- Duplex (ferritic-austenitic) stainless steel
- Precipitation-hardening (PH) stainless steel
Austenitic Stainless Steels
Austenitic stainless steel is chromium-nickel stainless steel with a stable Austenite structure, Austenitic stainless steel is the largest category, 70 percent of all stainless steel is austenitic, Austenitic stainless steel usually contains 16 to 26 percent chromium and up to 35 percent nickel content. this group includes Cr-Mn grades, Cr-Ni grades, Cr-Ni-Mo grades, high-performance austenitic grades, and high-temperature austenitic grades. Cr-Ni grades are sometimes referred to as 18-8 type of stainless steel, typical 304 grade, Cr-Mn grades are also referred to as “200-series” grades, the grade has almost the same formability, corrosion resistance and weldability as grade 304, but with higher strength. The high-performance austenitic stainless steels were developed for use in very demanding environments and have even higher alloying content, typically 254 SMO and 904L.
Austenitic steel grades have good comprehensive performance, good weldability and formability and excellent corrosion resistance, altering and improving the performance after adding different alloy elements such as molybdenum, titanium, and copper. Austenitic steel grades are non-magnetic in the solution-annealed condition, and not hardenable by heat treatment. Typical applications for austenitic stainless steel are in the food industry, catering and kitchen equipment, process industries, building, architecture and transport.
Austenitic Stainless Steel Chemical Composition
UNS No | AISI No. | C | Si | Mn | P | S | Cr | Mo | Ni | Others |
---|---|---|---|---|---|---|---|---|---|---|
S30100 | 301 | 0.15 | 1.00 | 2.00 | 0.045 | 0.030 | 16.0/18.0 | – | 6.0/8.0 | N 0.10 |
S30400 | 304 | 0.07 | 0.75 | 2.00 | 0.045 | 0.030 | 17.5/19.5 | – | 8.0/10.5 | N 0.10 |
S30403 | 304L | 0.030 | 0.75 | 2.00 | 0.045 | 0.030 | 17.5/19.5 | – | 8.0/12.0 | N 0.10 |
S30453 | 304LN | 0.030 | 0.75 | 2.00 | 0.045 | 0.030 | 18.0/20.0 | – | 8.0/12.0 | N 0.10/0.16 |
S30500 | 305 | 0.12 | 0.75 | 2.00 | 0.045 | 0.030 | 17.0/19.0 | – | 10.5/13.0 | – |
S31600 | 316 | 0.08 | 0.75 | 2.00 | 0.045 | 0.030 | 16.0/18.0 | 2.00/3.00 | 10.0/14.0 | N 0.10 |
S31603 | 316L | 0.030 | 0.75 | 2.00 | 0.045 | 0.030 | 16.0/18.0 | 2.00/3.00 | 10.0/14.0 | N 0.10 |
S31635 | 316Ti | 0.08 | 0.75 | 2.00 | 0.045 | 0.030 | 16.0/18.0 | 2.00/3.00 | 10.0/14.0 | Ti 5x (C+N) / 0.70 N 0.10 |
S31653 | 316LN | 0.030 | 0.75 | 2.00 | 0.045 | 0.030 | 16.0/18.0 | 2.00/3.00 | 10.0/14.0 | N 0.10/0.16 |
S31700 | 317 | 0.08 | 0.75 | 2.00 | 0.045 | 0.030 | 18.0/20.0 | 3.0/4.0 | 11.0/15.0 | N 0.10 |
S31703 | 317L | 0.030 | 0.75 | 2.00 | 0.045 | 0.030 | 18.0/20.0 | 3.00/4.00 | 11.0/15.0 | N 0.10 |
S31753 | 317LN | 0.030 | 0.75 | 2.00 | 0.045 | 0.030 | 18.0/20.0 | 3.0/4.0 | 11.0/15.0 | N 0.10/0.22 |
S32100 | 321 | 0.08 | 0.75 | 2.00 | 0.045 | 0.030 | 17.0/19.0 | – | 9.0/12.0 | Ti 5 X C Min/0.70 N 0.10 |
S34700 | 347 | 0.08 | 0.75 | 2.00 | 0.045 | 0.030 | 17.0/19.0 | – | 9.0/13.0 | Nb+Ta 10 X C Min/1.0 |
Ferritic Stainless Steel
Ferritic stainless steels contain a chromium content of 10.5-18%, adding chromium element improves the corrosion resistance, toughness and weldability, ferritic grades are magnetic due to their ferritic microstructure, and because of their low carbon content (less than 0.2 percent), they are not hardenable by heat treatment, they have bad mechanical properties and process performance compared to Austenitic stainless steels. The low nickel content of the ferritic grades make them more price stable compared to grades with high nickel content. Molybdenum is added to some grades to improve the corrosion resistance while alloying with niobium and/or titanium improves the weldability.
Ferritic stainless steel grades have good mechanical properties, sitting broadly in the middle between the other stainless steel families. They typically have higher yield strength than austenitic stainless steels. The elongation and forming properties of ferritic steel grades are equivalent to those of high-strength carbon steels.
Ferritic Stainless Steel Chemical Composition
UNS No | AISI No. | C | Si | Mn | P | S | Cr | Mo | Ni | Others |
---|---|---|---|---|---|---|---|---|---|---|
S40300 | 403 | 0.15 | 0.50 | 1.00 | 0.040 | 0.030 | 11.5/13.0 | – | – | – |
S40500 | 405 | 0.08 | 1.00 | 1.00 | 0.040 | 0.030 | 11.5/14.5 | – | – | Al 0.10./0.30 |
S40800 | – | 0.08 | 1.00 | 1.00 | 0.045 | 0.045 | 11.5/13.0 | – | 0.50 | Ti 12xC/1.10 |
S41008 | 410S | 0.08 | 1.00 | 1.00 | 0.040 | 0.030 | 11.5/13.5 | – | 0.60 | – |
S43000 | 430 | 0.12 | 1.00 | 1.00 | 0.040 | 0.030 | 16.0/18.0 | – | – | – |
S43400 | 434 | 0.12 | 1.00 | 1.00 | 0.040 | 0.030 | 16.0/18.0 | 0.75/1.25 | – | – |
S43600 | 436 | 0.12 | 1.00 | 1.00 | 0.040 | 0.030 | 16.0/18.0 | 0.75/1.25 | – | Nb+Ta 5xC/0.80 |
S44200 | 442 | 0.20 | 1.00 | 1.00 | 0.040 | 0.035 | 18.0/23.0 | – | 0.60 | – |
Martensitic Stainless Steels
Martensitic stainless steels can improve mechanical properties by heat treatment, chromium alloy is a key element containing 12–14% content, which is lower than that of Ferritic stainless steels, Generally, they also contain 0.1 to 1 percent carbon, 0.2 to 1 percent molybdenum and, less than 2 percent nickel, they have high carbon content. They are also magnetic.
Features of martensitic stainless steel include:
- Moderate corrosion resistance
- Heat treatable
- Magnetic
- Inability to be cold-formed
- Poor weldability
Martensitic grades are often used in applications where high strength and wear resistance are demanded, such as for shafts, knives, and wear and press plates.
Duplex Stainless Steels
Duplex stainless steels are combined of Ferrite and Austenite structure, usually containing 21 to 27 percent chromium, 1.35 to 8 percent nickel, 0.05 to 3 percent copper, and 0.05 to 5 percent molybdenum. Duplex grades have Ferrite and Austenite stainless steel benefits, high strength and toughness, excellent corrosion resistance and good weldability they are magnetic. Common duplex grades have 2101, 2304, 2205, and 2507. The duplex microstructure contributes to the high mechanical strength and high resistance to stress corrosion cracking.
Duplex Stainless Steel Chemical Composition
Chemical Composition
UNS Designation | C | Mn | P | S | Si | Ni | Cr | Mo | N | Cu | Others |
---|---|---|---|---|---|---|---|---|---|---|---|
S31200 | 0.030 | 2.00 | 0.045 | 0.030 | 1.00 | 5.5–6.5 | 24.0–26.0 | 1.20–2.00 | 0.14–0.20 | . . . | . . . |
S31260 | 0.030 | 1.00 | 0.030 | 0.030 | 0.75 | 5.5–7.5 | 24.0–26.0 | 2.5–3.5 | 0.10–0.30 | 0.20–0.80 | W 0.10–0.50 |
S31500 | 0.030 | 1.20–2.00 | 0.030 | 0.030 | 1.40–2.00 | 4.3–5.2 | 18.0–19.0 | 2.50–3.00 | 0.05–0.1 | . . . | . . . |
S31803 | 0.030 | 2.00 | 0.030 | 0.020 | 1.00 | 4.5–6.5 | 21.0–23.0 | 2.5–3.5 | 0.08–0.20 | . . . | . . . |
S32001 | 0.030 | 4.00–6.00 | 0.040 | 0.030 | 1.00 | 1.0–3.0 | 19.5–21.5 | 0.60 | 0.05–0.17 | 1.00 | . . . |
S32003 | 0.030 | 2.00 | 0.030 | 0.020 | 1.00 | 3.0-4.0 | 19.5-22.5 | 1.50-2.00 | 0.14-0.20 | . . . | . . . |
S32101 | 0.040 | 4.0-6.0 | 0.040 | 0.030 | 1.00 | 1.35-1.70 | 21.0-22.0 | 0.10-0.80 | 0.20-0.25 | 0.10-0.80 | . . . |
S32202 | 0.030 | 2.00 | 0.040 | 0.010 | 1.00 | 1.00–2.80 | 21.5–24.0 | 0.45 | 0.18–0.26 | . . . | . . . |
S32205 | 0.030 | 2.00 | 0.030 | 0.020 | 1.00 | 4.5–6.5 | 22.0–23.0 | 3.0–3.5 | 0.14–0.20 | . . . | . . . |
S32304 | 0.030 | 2.50 | 0.040 | 0.040 | 1.00 | 3.0–5.5 | 21.5–24.5 | 0.05–0.60 | 0.05–0.20 | 0.05–0.60 | . . . |
S32506 | 0.030 | 1.00 | 0.040 | 0.015 | 0.90 | 5.5–7.2 | 24.0–26.0 | 3.0–3.5 | 0.08–0.20 | . . . | W 0.05–0.30 |
S32520 | 0.030 | 1.50 | 0.035 | 0.020 | 0.80 | 5.5–8.0 | 23.0–25.0 | 3.–5. | 0.20–0.35 | 0.50–3.00 | . . . |
S32550 | 0.04 | 1.50 | 0.040 | 0.030 | 1.00 | 4.5–6.5 | 24.0–27.0 | 2.9–3.9 | 0.10–0.25 | 1.50–2.50 | . . . |
S32707 | 0.030 | 1.50 | 0.035 | 0.010 | 0.50 | 5.5–9.5 | 26.0–29.0 | 4.0–5.0 | 0.30–0.50 | 1.0 max | Co 0.5–2.0 |
S32750 | 0.030 | 1.20 | 0.035 | 0.020 | 0.80 | 6.0–8.0 | 24.0–26.0 | 3.0–5.0 | 0.24–0.32 | 0.50 | . . . |
S32760 | 0.030 | 1.00 | 0.030 | 0.010 | 1.00 | 6.0–8.0 | 24.0–26.0 | 3.0–4.0 | 0.20–0.30 | 0.50–1.00 | W 0.50–1.00 |
S32808 | 0.030 | 1.10 | 0.030 | 0.010 | 0.50 | 7.0–8.2 | 27.0–27.9 | 0.80–1.20 | 0.30–0.40 | . . . | W 2.10–2.50 |
S32900 | 0.08 | 1.00 | 0.040 | 0.030 | 0.75 | 2.5–5.0 | 23.0–28.0 | 1.00–2.00 | . . . | . . . | . . . |
S32906 | 0.030 | 0.80–1.50 | 0.030 | 0.030 | 0.80 | 5.8–7.5 | 28.0 –30.0 | 1.50–2.60 | 0.30–0.40 | 0.80 | . . . |
S32950 | 0.030 | 2.00 | 0.035 | 0.010 | 0.60 | 3.5–5.2 | 26.0–29.0 | 1.00–2.50 | 0.15–0.35 | . . . | . . . |
S33207 | 0.030 | 1.50 | 0.035 | 0.010 | 0.80 | 6.0–9.0 | 29.0–33.0 | 3.0–5.0 | 0.40–0.60 | 1.0 | . . . |
S39274 | 0.030 | 1.00 | 0.030 | 0.020 | 0.80 | 6.0–8.0 | 24.0–26.0 | 2.5–3.5 | 0.24–0.32 | 0.20–0.80 | W 1.50–2.50 |
S39277 | 0.025 | 0.80 | 0.025 | 0.002 | 0.80 | 6.5–8.0 | 24.0–26.0 | 3.00–4.00 | 0.23–0.33 | 1.20–2.00 | W 0.80–1.21 |
S82011 | 0.030 | 2.0–3.0 | 0.040 | 0.020 | 1.00 | 1.00–2.00 | 20.5–23.5 | 0.10–1.00 | 0.15–0.27 | 0.50 | . . . |
S82441 | 0.030 | 2.50–4.00 | 0.035 | 0.005 | 0.70 | 3.0–4.5 | 23.0–25.0 | 1.00–2.00 | 0.20–0.30 | 0.10–0.80 |
Maximum, unless a range or minimum is indicated.
Typical applications for duplex stainless steels are process industries, pulp & paper, oil & gas applications, desalination, chemical tankers (cargo tanks), pressure vessels and structural applications in harsh climates. Super duplex stainless steels are found in marine installations, oil & gas, flexible pipes, umbilicals and desalination plants.
Precipitation-Hardening Stainless Steels
This group’s grades contain both chromium and nickel, with high tensile strength. Matrix for the Austenitic or Martensitic crystal structure The commonly used grade is PH 17-4, also known as 630 grade, with 17% of chromium, 4% of nickel, 4% of copper and 0.3% of niobium.
Precipitation hardening stainless steel adds strengthening elements of different compositions and percentages, the process of precipitation in different compositions and percentages of carbide, nitride, carbon nitride and intermetallic compounds, a kind of high-strength stainless steel can increase the strength of the steel and maintain sufficient toughness.
Stainless Steel Grades
304 Stainless Steel
304 stainless steel is a typical 18-8 chromium-nickel grade, as well as the basic grade of Austenitic stainless steels, the chemical composition of 304 stainless steel is mainly iron Fe (about 67-71.5%), chromium Cr (about 18-20%) and nickel Ni (about 8-10.5%). Among them, chromium and nickel are important elements to improve the corrosion resistance and oxidation resistance of stainless steel, chromium can form a layer of stable passivation film on the surface, to protect the steel from external erosion, and nickel can enhance the stability and ductility of the passivation film to improve the plasticity and toughness of stainless steel. 304 stainless steel also contains a small amount of carbon C (≤0.08%), manganese Mn (≤2.00%), silicon Si (≤1.00%), phosphorus P (≤0.00%) and phosphorus P (≤0.00%). ), phosphorus P (≤ 0.045%), sulfur S (≤ 0.030%) and other elements, these elements have a certain effect on the mechanical properties and processing performance of stainless steel. it is the most commonly used stainless steel grade.
304L Stainless Steel
304L stainless steel has a low carbon content of 304, the chemical composition of 304L stainless steel includes carbon (C) ≤ 0.03%, silicon (Si) ≤ 1.0%, manganese (Mn) ≤ 2.0%, phosphorus (P) ≤ 0.045%, sulfur (S) ≤ 0.03%, chromium (Cr) 18.0-20.0%, nickel (Ni) 8.0-10.0%. Its chemical composition is characterized by a low carbon content, usually below 0.03%, which makes 304L stainless steel excellent resistance to intergranular corrosion, especially suitable for welded parts without heat treatment. In addition, 304L stainless steel also has good processing performance and welding performance, commonly used in the manufacture of high-temperature furnaces, heat treatment equipment, and so on.
316L Stainless Steel
316L stainless steel is a low carbon and addition of molybdenum element grade, The carbon content should be controlled at C≤0.03%, silicon content Si≤1.00%, manganese content Mn≤2.00%, phosphorus content P≤0.035%, and sulfur content S≤0.03%. The range of nickel content is Ni:10.0-14.0%, chromium content Cr:16.0-18.0%, and molybdenum is added between Mo:2.0-3.0%, these elements give 316L stainless steel excellent corrosion resistance, especially to alkaline solutions and most organic and inorganic acids. In addition, due to the presence of molybdenum, 316L stainless steel shows good resistance to pitting corrosion and creep resistance at high temperatures.
321 Stainless Steel
321 stainless steel composition are iron, chromium and nickel, of which the content of chromium is between 17% and 20%, and the content of nickel is between 9% and 13%. In addition, it also contains a small amount of carbon, silicon, manganese, phosphorus, sulfur and other elements. 321 stainless steel is Ni-Cr-Ti type austenitic stainless steel, its properties are very similar to 304, but due to the addition of the metal titanium, so that it has a better resistance to grain boundary corrosion and high-temperature strength. Due to the addition of titanium, it effectively controls the formation of chromium carbide.
904L Stainless Steel
904L stainless steel contains a high proportion of chromium, nickel and molybdenum and other alloying elements, the chemical composition is generally as follows: chromium (Cr) is about 19% to 23%, nickel (Ni) is about 23% to 28%, molybdenum (Mo) is about 4% to 5%, but also contains a small amount of copper (Cu) and low carbon content. 904L (N08904) austenitic stainless steel has excellent corrosion resistance in a variety of acidic media, including sulfuric acid, phosphoric acid, nitric acid and other strong acids, as well as seawater and other corrosive solutions with high chloride content. It also has good resistance to corrosive gases and oxidizing agents and is suitable for use in marine environments, chemical, petroleum, pharmaceutical, food processing and other fields.
430 Stainless Steel
430 stainless steel is the basic grade of ferritic stainless steel, and most of the performance with 304 is similar, 430 grade consists mainly of iron, chromium and a small amount of carbon. Its chromium content is usually around 16-18 percent, which gives it good corrosion resistance, especially in weakly acidic and alkaline environments. Typical 430 is often used as a substitute for 304 of the materials used in kitchen facilities, dishwashers, pots, etc. 430 stainless steel can be considered a food-grade material, especially for use in a general kitchen environment. However, for some specific applications with high acidity or special hygiene requirements, 304 or 316 stainless steel may be preferred.
444 Stainless Steel
444 stainless steel contains 18-20% chromium, 11-13% molybdenum, 0.5-1.5% carbon, 2-3% nickel, and trace amounts of other elements. The high levels of chromium and molybdenum give 444 stainless steel excellent corrosion resistance. The low carbon content ensures that 444 stainless steel is resistant to intergranular corrosion and weldable. The high nickel content makes 444 stainless steel resistant to pitting and crevice corrosion, the corrosion resistance of 444 grade is similar to that of 316 grade. 444 Higher chromium and molybdenum content also gives better weldability than 316/316L stainless steel.
409 Stainless Steel
409 stainless steel contains chromium content10.5-11.75%, and the nickel content is less than 0.5%. In addition, 409 has a small amount of carbon, manganese, silicon, phosphorus, sulfur and other elements. 409 is a chromium-nickel stainless steel material with good corrosion resistance, high-temperature resistance and mechanical properties, suitable for automotive exhaust systems, boiler flues, and other applications requiring corrosion resistance and high-temperature resistance, it is applied for no corrosion or mild corrosive environment.
439 Stainless Steel
439 steel grade is based on the ordinary ferritic material (430) to reduce the content of C while adding Ti and other stabilizing elements, so that the intergranular corrosion resistance, formability and weldability of this steel grade have been improved.
441 Stainless Steel
441 stainless steel is a ferritic stainless steel alloy characterized by a high chromium content, which gives it excellent corrosion resistance. Compared to other ferritic steels, 441 stainless steel has a higher chromium content, typically between 17.5 and 18.5 percent, which provides it with excellent corrosion resistance. In addition, titanium and niobium are added to 441 stainless steel, which helps to stabilize the carbides, which in turn improves the steel’s oxidation resistance and strength at high temperatures.
436 Stainless Steel
The chemical composition of 436 stainless steel mainly includes low carbon content (≤0.12%), moderate amount of chromium (16.00 ~ 18.00%) and molybdenum (0.75 ~ 1.25%), the reasonable ratio of these elements gives it excellent corrosion resistance and strength. In addition, stainless steel also has good processing properties and heat treatment properties, making it suitable for a variety of processing and forming processes.
446 Stainless Steel
446 stainless steel has more chromium and molybdenum that increased corrosion resistance and oxidation resistance, corrosion resistance and oxidation resistance is better than 316, the typical use of coastal and other corrosion-resistant environments.
410 Stainless Steel
410 stainless steel is the basic Martensitic stainless steel grade, mainly containing iron, carbon, chromium and other elements, of which the carbon content is ≤0.15% and the chromium content is between 11.50 and 13.50%. In addition, it also contains a small amount of silicon, manganese, phosphorus, sulfur and other elements. 410 stainless steel has good corrosion resistance in weak corrosive media, especially for atmospheric corrosion has a strong resistance. After hardening and polishing treatment, its corrosion resistance can be further improved. After quenching and tempering treatment, 410 stainless steel has high strength and toughness. At the same time, it also has good mechanical processing performance, suitable for the manufacture of various mechanical parts.
420 Stainless Steel
420 stainless steel includes carbon (C) and chromium (Cr). Specifically, the chemical composition of 420 stainless steel is dominated by two elements, carbon and chromium. This steel is produced to ASTM standards and contains 12-14% chromium and a minimum carbon content of 0.15%, with a typical value of 0.31%. The UNS standard number for 420 stainless steel is UNS S42000. 420 stainless steel is widely used in many industrial applications due to its good corrosion resistance and hardness.
431 Stainless Steel
431 stainless steel is a martensitic stainless steel alloy whose chemical composition consists primarily of chromium and nickel with a significant addition of 1.25-2.5 percent manganese. The steel also contains moderate amounts of carbon, usually around 0.12-0.20 percent, which contributes to its martensitic structure and high strength. The presence of chromium provides corrosion resistance, making it suitable for applications in mildly corrosive environments. 431 stainless steel is known for its exceptional hardness, toughness, and wear resistance, making it a popular choice for components in industries such as aerospace, automotive, and medical equipment, where strength and durability are critical. it has the best corrosion resistance properties of all the martensitic grades.
440 Stainless Steel
440 stainless steel is high-carbon chromium steel, also known as high-carbon high-chromium stainless steel.440 stainless steel is mainly composed of iron (Fe), carbon (C), chromium (Cr) and molybdenum (Mo) and other elements. The carbon content is usually between 0.60 percent and 0.75 percent, and the chromium content is 16 percent to 18 percent. In addition, small amounts of molybdenum and other alloying elements can be added to improve the material properties. 440 grade has 440A, 440B, and 440C.
2205 Duplex Steel
2205 duplex stainless steel is typically composed of 22% chromium, 2.5% molybdenum, 4.5% to 6.5% nickel, 0.14% to 0.20% nitrogen, and small amounts of carbon (C ≤ 0.030%), silicon (Si ≤ 1.00%), manganese (Mn ≤ 2.00%), phosphorus (P ≤ 0.030%) and sulfur (S ≤ 0.020%). The unique complex structure of this stainless steel gives it many excellent properties. The proper balance of its ferrite and austenite phase ratio ensures high strength, high corrosion resistance and good welding performance. Compared with ordinary austenitic stainless steels, 2205 duplex stainless steel has more than double the yield strength and excellent resistance to chloride stress corrosion cracking. Its high chromium and molybdenum content gives it excellent resistance to pitting and uniform corrosion, while the duplex microstructure greatly improves resistance to stress corrosion rupture.
AISI Stainless Steel
The AISI (American Iron and Steel Institute) system for naming stainless steel is still used by the industry. The numbering system uses three-digit numbers starting with 2, 3, or 4. Stainless steels are also designated as 200 series, 300 series, 400 series, 500 series, 600 series.
- 200 Series, This series is used for austenitic grades that contain manganese. These chromium manganese steels have a low nickel content (below 5 percent).
- 300 Series, This series names austenitic stainless steels with carbon, nickel, and molybdenum as alloying elements. The addition of molybdenum improves corrosion resistance in acidic environments while nickel improves ductility.
- 400 Series, Ferritic and martensitic alloys form this series of stainless steel. These grades are available for heat treatment. Providing a good combination of strength and high wear resistance. The corrosion-resistance properties are lower than the 300 series, though.
- 500 Series
- 600 Series
- SAE Grades, The SAE system of numbering uses a 1-letter + 5-digit UNS number code to designate stainless steel. The common AISI grade 304 has S30400 as its SAE designation. While most grades have a designation, newly developed exclusive grades may be named by their owners and not have any SAE code.
Stainless Steel Equivalents
Stainless Steel Equivalents
EN Designation | Alternative Designations | |||||
---|---|---|---|---|---|---|
Steel Name | Steel Number | AISI | UNS | GB | BS | Generic/Brand |
Ferritic Stainless Steels | ||||||
X2CrNi12 | 1.4003 | S40977 | 3CR12 | |||
X2CrTi12 | 1.4512 | 409 | S40900 | 409S19 | ||
X6CrAl13 | 1.4002 | 405 | S40500 | 405S17 | ||
X6Cr17 | 1.4016 | 430 | S43000 | 430S17 | ||
X3CrTi17 | 1.4510 | 439 | S43035 | |||
X2CrMoTi18-2 | 1.4521 | 444 | S44400 | |||
X6CrMoNb17-1 | 1.4526 | 436 | S43600 | |||
X2CrTiNb18 | 1.4509 | 441 | S43932 | 18CrCb | ||
Austenitic Stainless Steels | ||||||
X2CrNiN18-7 | 1.4318 | 301LN | S30153 | |||
X2CrNi18-9 | 1.4307 | 304L | S30403 | 022Cr19Ni10 | 304S11 | |
X2CrNi19-11 | 1.4306 | 304L | S30403 | |||
X2CrNiN18-10 | 1.4311 | 304LN | S30453 | 304S51 | ||
X5CrNi18-10 | 1.4301 | 304 | S30400 | 06Cr19Ni10 | 304S15 | |
X6CrNiTi18-10 | 1.4541 | 321 | S32100 | 06Cr18Ni11Ti | 321S31 | |
X6CrNiNb18-10 | 1.4550 | 347 | S34700 | 06Cr18Ni11Nb | 347S31 | |
X2CrNiMo17-12-2 | 1.4404 | 316L | S31603 | 022Cr17Ni12Mo2 | 316S11 | |
X5CrNiMo17-12-2 | 1.4401 | 316 | S31600 | 06Cr17Ni12Mo2 | 316S31 | |
X6CrNiMoTi17-12-2 | 1.4571 | 316Ti | S31635 | 06Cr17Ni12Mo2Ti | 320S31 | |
X2CrNiMo17-12-3 | 1.4432 | 316L | S31603 | 316S13 | ||
X2CrNiMoN17-3-3 | 1.4429 | 316LN | S31653 | |||
X3CrNiMo17-13-3 | 1.4436 | 316 | S31600 | 316S33 | ||
X2CrNiMo18-14-3 | 1.4435 | 316L | S31603 | 316S13 | ||
X2CrNiMoN17-13-5 | 1.4439 | 317LMN | S31726 | |||
X1NiCrMoCu25-20-5 | 1.4539 | N08904 | 015Cr21Ni26Mo5Cu2 | 904S13 | 904L | |
X1CrNiMoCuN20-18-7 | 1.4547 | S31254 | 015Cr20Ni18Mo6CuN | 254SMO | ||
X6CrNiMoNb17-12-2 | 1.4580 | S31640 | ||||
X2CrNiMo18-15-4 | 1.4438 | 317L | S31703 | 022Cr19Ni13Mo3 | 317S12 | |
X1CrNiMoCuN24-22-8 | 1.4652 | S32654 | 654SMO | |||
X1NiCrMo31-27-4 | 1.4563 | N08028 | Sanicro 28 | |||
X1CrNiMoCuN25-25-5 | 1.4537 | N08932 | ||||
X1CrNiMoCuNW24-22-6 | 1.4659 | S31266 | ||||
X1NiCrMoCuN25-20-7 | 1.4529 | N08925 | 1925hMo | |||
Austenitic Stainless Steels – Heat Resisting Grades | ||||||
X15CrNiSi20-12 | 1.4828 | |||||
X9CrNiSiNCe21-11-2 | 1.4835 | S30815 | 253 MA | |||
X12CrNi23-13 | 1.4833 | 309 | S30900 | 309S24 | ||
X8CrNi25-21 | 1.4845 | 310S | S31000 | 06Cr25Ni20 | 310S24 | |
X6CrNiSiNCe19-10 | 1.4818 | S30415 | 153 MA | |||
X6NiCrSiNCe35-25 | 1.4854 | S35315 | 353MA | |||
X10NiCrSi35-19 | 1.4886 | N08330 | 330 | |||
Austenitic-Ferritic Stainless Steels | ||||||
X2CrMnNiN21-5-1 | 1.4162 | S32101 | 2101 LDX | |||
X2CrNiN23-4 | 1.4362 | S32304 | 2304 | |||
X2CrNiMoN12-5-3 | 1.4462 | S31803/S32205 | 022Cr23Ni5Mo3N | 2205 | ||
X2CrNiMoN25-7-4 | 1.4410 | 2507 | ||||
X2CrNiMoCuEWN25-7-4 | 1.4501 | S32760 | Zeron 100 |
Stainless Steel Systems
There are several stainless steel grade systems in the world, each standard has a unique No. or name, in many cases, these grades can be equivalent, due to their the same or similar chemical composition and properties.
- ASTM, American Society for Testing and Materials
- AISI, American Iron and Steel Institute
- EN, European Standard
- DIN, German Standard
- JIS, Japanese Industrial Standards
- GB, Chinese Standard
- BS, British Standards
Stainless Steel Properties
Physical Properties
Modulus of Elasticity
The modulus of elasticity is a measure of a material’s ability to resist deformation. The modulus of elasticity of stainless steel is related to its composition and structure and is usually high.
Thermal Expansion
Thermal expansion refers to the phenomenon of expansion and contraction that occurs when an object changes temperature. Stainless steel compared with carbon steel, austenitic 304 stainless steel has a larger coefficient of linear expansion, while ferritic 430 stainless steel has a smaller coefficient of linear expansion.
Thermal Conductivity
The thermal conductivity of stainless steel is generally considered to be ‘bad’, but in cases where insulation is required, this property becomes an advantage. For example, the thermal conductivity of 430 stainless steel is about 1/8 of that of aluminum, and that of 304 stainless steel is about 1/13 of that of aluminum. In addition, the thermal conductivity of stainless steel varies with temperature, and in the high-temperature range from 50 to 800°C, the thermal conductivity increases with the increase in temperature; in the low-temperature range, the thermal conductivity decreases with the decrease in temperature.
Density
The density of stainless steel ranges from 7600 kg/m3 to 8000 kg/m3, stainless steel is usually denser than carbon steel, but less dense than plastics, glass, aluminum and titanium, and slightly less dense than copper. Specifically, the austenitic series of stainless steels are denser than carbon steel, while the martensitic and ferritic series of stainless steels are less dense than carbon steel.
Magnetic Conductivity
Magnetic conductivity is a dimensionless coefficient that indicates how easily a substance can be magnetized. The magnetic permeability of stainless steel is related to its composition and structure, and usually stainless steel has a low magnetic conductivity.
Melting Point
Stainless steel is a kind of alloy material, composed of iron, chromium, nickel, carbon and other elements, and its melting point is affected by the content and proportion of various elements. Generally speaking, the melting point of 304 stainless steel is about 1400℃, the melting point of 316 stainless steel is about 1425℃, and the melting point of stainless steel in high temperature alloys can be as high as 1700℃ or more.
Specific heat
Specific heat is the amount of heat required to change the temperature of a substance per unit mass by 1 degree. The specific heat of stainless steel is related to its composition and structure, and the specific value should be analyzed according to the specific material.
Mechanical Properties
Yield Strength
Depending on the grade, stainless may exhibit high strength and low elongation or low strength and high elongation properties. They compare very well to carbon steels when it comes to yield strength.
Tensile Strength
When it comes to tensile strength, stainless steel is superior to materials like aluminum, brass, and mild steel, the highest tensile strength is seen in precipitation hardening and martensitic grades. These grades can have tensile strengths that are twice as much as the ubiquitous 304 and 316 grades. Duplex steel, in particular, has a high strength/ductility ratio.
Elongation
Elongation refers to the stretching process, the material in the unit length of the deformation, is a measure of the ductility of stainless steel material and is an important indicator. The elongation of stainless steel and its material composition, processing technology, temperature and other factors. Generally speaking, the higher the elongation of stainless steel, the better its ductility, which means that it is easier to deform during processing, and easier to mold. The elongation of stainless steel is usually expressed as a percentage, for example, the elongation of 304 stainless steel is about 40%.
Hardness
Hardness expresses the ability of a material to resist being pressed into its surface by a hard object. It is one of the important performance indicators of metallic materials. Generally the higher the hardness, the better the wear resistance. Commonly used hardness indicators are Brinell hardness, Rockwell hardness and Vickers hardness.
Stainless Steel Composition Chart
Corrosion Resistance
Stainless steel has good corrosion resistance, the biggest difference between it and carbon steel. Chromium elements exist and other additions of alloys increase corrosion resistance, these elements react with oxygen to form spontaneously a very thin and stable film in air, a self-healing protective clear oxide layer that forms spontaneously in air. The self-healing nature of the oxide layer resists corrosion, When the material surface is cut or damaged, it will self-heal and corrosion resistance will be maintained.
Increasing Chromium content and Molybdenum content can improve corrosion resistance, in general, Austenitic Stainless Steels are better than Ferritic Stainless Steels and Duplex Stainless Steels perform best, in different environments, such as air, seawater, acid, and high-temperature conditions, thus selecting the right stainless steel grade is very important to use in these conditions.
Though stainless steels have excellent corrosion resistance and are not easy to rust, However, stainless steel is not completely true that it is stain-proof, the corrosion resistance depends on the grade, It is essential to choose the grade to suit the application.
Stainless Steel Finishes
Various stainless steel surface finishes are available, depending on the desired applications. The costs of achieving different surface finishes are varied. In general, smoother or more polished surfaces are more expensive than rougher surfaces.
Mill finishes and polishing finishes are common surface finishes, Mill finishes are attained by direct application of rollers and mechanical abrasives to flat rolled (wrought) stainless steel sheets and are the basic finishes for all flat stainless steels. Polished finishes are attained by the use of a variety of techniques to “polish” stainless steel. Grinding with abrasives and/or buffing with cloth wheels may be used to achieve a reflective finish.
NO.1 | Cold Rolled, Annealed, Pickled, Smooth Non-Reflective Finish |
---|---|
NO.2D | Cold Rolled, Annealed, Pickled, Smooth Reflective Finish, The Widest Used Finish |
NO.2B | Cold Worked To Obtain Specified Properties |
BA | Smooth, Bright, Reflective Finish By Annealing In The Controlled Atmosphere Furnace |
NO.3 | Non Reflective Finish, Light Polishing Using Grinding Belt, 100 – 120 Grit |
NO.4 | Reflective Dull Polishing, Brushed Finish, Using 120 – 320 Grit Belt After Light Grinding |
NO.6 | Cold Rolled, Dull Satin Finish By Tampico Brushing A No.4 Finish |
NO.7 | High Reflective Finish, By A Finely Ground Surface, 320 Grit Is Buffed |
NO.8 | High Reflective, Bright Polishing, Smooth Surface, Mirror Finish |
TR | Cold Worked To Obtain A Specified Properties |
Advantages of Stainless Steel
Stainless steels are sustainable, as both recyclable and reusable, This is good for the environment. Stainless steels are versatile. Available in 150 different standard iterations, there’s stainless steel for every application. Next, stainless steel is incredibly durable and strong. Finally, unlike many lesser metals, stainless steel doesn’t need a special coating or finish to resist attacks from corrosion, abrasion, and the like.
- Superior corrosion resistant
- High tensile strength
- Highly durable
- Temperature-resistant, cold and heat-resistant
- Easy formability and fabrication
- Low-maintenance, long life cycle
- Attractive appearance with various surface finishes, easy to clean
- Environmentally friendly (recyclable)
- Hygienic and Safe material
- Lightweight
- Recyclability
- Cleanability
Stainless Steel Products
Stainless steels have high strength and excellent corrosion resistance, and they are easy to weld and clean, safe and durable material, with various surface finishes for option, it can be recycled and reused. Stainless steel is an ideal material for designing and fabricating flat and long products.
- Stainless steel plates
- Stainless Steel strips
- Stainless steel bars
- Stainless steel wire
- Stainless steel pipe
- Stainless steel tube
Stainless Steel Applications
The high-performance stainless steels collectively offer a great variety of mechanical, physical, metallurgical, and corrosion properties, the stainless grades are suitable for use in different applications and environments. Thus, the applications in which they are used are extremely varied and usually much more corrosive than would be suitable for the standard stainless grades. High-performance stainless steels are being used in literally thousands of different applications in many areas of the process, energy, paper, transportation, and other industries. They are available in essentially all product forms and are covered by many industry specifications.
Chemical Processing And Petrochemical Industries
Stainless steel is the material of choice in the Chemical and petrochemical industries because it offers excellent corrosion resistance in the harsh gaseous, aqueous, and high-temperature environments used in these industries.
Oil Well Tubing and Drill pipe.
Weakly magnetic (i.e. paramagnetic) not easily magnetized stainless steel made of thick-walled (wall thickness generally between 30 to 103 mm) non-magnetic drill collar. In addition to its role with ordinary chrome molybdenum alloy steel made of thick-walled drill collar in the drilling operation together on the bottom of the wellhead to exert a certain amount of pressure to break the formation, but also plays a role in attenuating the magnetic field with the non-magnetic collars on the top and bottom of the ferromagnetic alloy steel connected to the role of the magnetic field of the drilling column. Non-magnetic drill collars can be categorized into non-magnetic Monel alloy steel drill collars, non-magnetic beryllium-copper alloy steel drill collars and non-magnetic face-centered cubic lattice austenitic stainless steel drill collars, etc., according to the steel used for manufacturing. Austenitic stainless steel non-magnetic drill collars are cheaper than the first two alloy steel non-magnetic drill collars, but the magnetic properties are not as stable as the first two. The drill collar in the weak magnetic field (i.e., the earth’s magnetic field) when used in a certain period to maintain good magnetic properties, but if long-term in the weak magnetic field and a variety of alternating stress will produce a certain amount of remanent magnetism. In the case of a strong magnetic field, a certain amount of remanent magnetization will be generated under the action of a strong magnetic field. In both cases, the residual magnetism will make the relative permeability and magnetic uniformity deviate from the standard requirements. And because in the processing and use process, unstable austenite organization in the external forces (such as knocking, collision, cold hardening, etc.), may be transformed to martensite, so that the local parts of the original weak magnetism into ferromagnetism, leading to the emergence of non-magnetic collars with high magnetism, so that the magnetic uniformity of the change.
Oil and Gas Pipelines and Their Equipment.
Duplex stainless steels are now widely used in the development of major piping systems for all major oil companies and are also the main material used in offshore oil and gas extraction and transportation engineering. Standard duplex stainless steels perform well in sweet, wet, and sour service environments. In contrast, ordinary carbon steel is not effective in preventing internal corrosion due to its high internal corrosion rate, even though additional corrosion inhibitors can be used to prevent external corrosion. Not only that, at ambient temperatures above 50℃, it may also lead to stress corrosion cracking (SCC). So duplex stainless steel has gradually replaced 300 stainless steel. With the H (2) S outside, some high containing H (2) S, CO (2), Cl (-), O (2), and other corrosive media such as oil and gas wells developed in the transmission of oil and gas in the concentration of the increase, accompanied by the increase in the transmission temperature, pressure and pipeline temperature, super duplex stainless steel began to be used in piping systems, valves, heat exchangers, pressure vessels.
Oil and Petroleum Refining.
With the oil processing industry modernization, large-scale and efficient development, corrosion is more and more prominent, the a need for more and more low C, ultra-low C, high purity ferrite, and other highly stainless seamless steel pipe and stainless steel welded pipe. In petroleum processing, new and existing pipelines such as atmospheric decompression, distillation, catalytic cracking, delayed coking, desulfurization and hydrogenation refining are subject to different degrees of corrosion. In addition to the inner shell with stainless steel plate, it heating furnace tubes, heat exchanger tubes, condenser tubes, and circulating and conveying pipelines, but also uses corrosion-resistant stainless steel tubes. Duplex stainless steel and the usual 18-8 austenitic stainless steel compared to the yield strength of austenitic steel is about 2 times, toughness is better than ferrite stainless steel, processing and forming of good, welded without the need for heat treatment, especially for resistance to H (2) S stress corrosion and Cl (-) stress corrosion of the environment. High-purity ferritic stainless steel, used to resist a variety of oxidizing media, moderate reducing media and halogenated media caused by pitting corrosion, crevice corrosion, and stress corrosion, better than 316L, has been widely used in heat exchangers, refinery equipment, chlorinated or corrosive harsh environments.Incoloy800 series is a Fe-Ni-Cr alloy, the higher Cr content on the surface of the alloy forms a layer of good protection of chlorinated film, and higher Ni content makes the surface chlorinated film good adhesion, so it has good oxidation resistance, get vulcanization ability. The higher content of Cr makes the surface of the alloy form a protective chlorinated film, and the higher content of Ni makes the surface of the chlorinated film have good adhesion, so it has very good oxidation resistance and vulcanization ability. This series has been widely used in ethylene cracking furnace tubes, heat exchangers, hydrocracking, hydrodesulfurization and other devices. In addition to steel pipe, petroleum refining equipment manufacturing and maintenance also use 321-316L and other grades of medium and thick plate, cold rolled stainless steel sheet for petrochemical containers (usually 0.3-0.6mm, 1219-1520mm, SUS316, surface condition NO.2B/2D).
Structure And Architecture
As inox is highly durable and impervious to rust, it is frequently used for a variety of architectural components, including cladding, handrails, fittings for doors and windows, street furniture, rebar, lighting fixtures, and masonry supports. It is also valued in architectural design for its aesthetic appearance.
Medical And Pharmaceutical Equipment
Stainless steel products such as infusion racks, stethoscopes, syringe tubes, tweezers, tweezer tubes, povidone-iodine cartridges, sieve frames, sterilizing squares, sterilizing boxes, small medicine spoons, tongue depressors, and so on have been widely used in hospitals. For example, medical stents, bone drills, walking aids, instrument cabinets, adjustable cabinets, scalpels, surgical scissors, surgical forceps, surgical shadowless lamps and hole shadowless lamps, depth irradiation shadowless lamps, cold single hole lamps, medical carts, operating beds, gynecological examination beds, nursing care beds, washing tanks, stainless steel test tube racks, medical equipment trolleys, stretchers. These are usually made of antimicrobial stainless steel.
Food, Beverage And Kitchen Appliances
Stainless steel is an ideal material for use in food and beverage industries because of its safe and easy-to-clean features, not only in the process but also in storage.
The material’s corrosion resistance and easily sterilized surface make it particularly useful for the food and beverage industry, which requires high standards of cleanliness. In this industry, stainless steel is used in food preparation and catering equipment, piping and containers used for brewing and distilling, and a wide range of food processing equipment.
Automotive Industry
The application of stainless steel in the automotive industry can be roughly summarized into five categories: stainless steel for automotive exhaust systems, stainless steel for automotive fuel tanks, stainless steel for automotive frames, automotive stainless steel parts and automotive decorative stainless steel.
Automotive fuel tank with stainless steel is mainly stainless steel plate, require excellent stamping and forming properties, welding performance and high corrosion resistance (internal fuel corrosion resistance and external corrosion resistance to harsh environments), the use of more austenitic stainless steel, such as SUS304L. Stainless steel for the automotive frame with a high-strength stainless steel plate for automobiles, such as ferritic stainless steel made of the overall body shell, service life Generally 15-20 years.
Stainless steel is also used in a variety of automotive parts, such as stainless steel seals, stainless steel plate heat exchangers (the material is mostly used in SUS304, SUS430 and SUS409L), automotive engine systems and transmission systems with stainless steel fasteners (commonly used stainless steel SUS410, SUS304, SUS316, SUS430JIL, SUH660, etc.).
Stainless steel is also used in automobile decoration, such as inserts, antennas, wheel covers, or handrails of large buses, safety rails, handrails, and so on. Stainless steel tubes are mainly used in the domestic passenger car exhaust system and vehicle decoration, which is mainly used in the automobile exhaust system application.
Jewelry
Stainless steels have a bright surface, even a mirror surface, after concern processing, it can be finished for decorative use, like Jewelry, rings, watches, etc.
3D Printing
Stainless steels are ideal materials to resist corrosion and keep good mechanical properties, The 316L type is a common grade to use in 3D print industries. Currently, the stainless steel used for metal 3D printing mainly includes three kinds: austenitic stainless steel 316L, martensitic stainless steel 15-5PH, and martensitic stainless steel 17-4PH.
Stainless steel is currently the most widely used material for metal 3D printing, commonly austenitic stainless steel and martensitic stainless steel. Stainless steel has excellent rust, wear and corrosion resistance, and its strength exceeds that of many steels and can be used in 99% of industrial applications; at the same time, under the same weight, stainless steel materials usually have the lowest price, which is one of its biggest advantages.
Stainless Steel Elements
Various chemical elements play an important role in stainless steel, each of the different grades of stainless steel contains different alloying elements that contribute to its properties such as resistance to corrosion, strength, and flexibility, several critical elements with explanations are listed below:
Carbon (C)
Yield point and tensile strength increased with carbon content increasing, but ductility and impact resistance decreased. When carbon content exceeds 0.23%, the welding performance of steel will be not good, carbon content is generally not more than 0.20%. High carbon content can also affect the corrosion resistance of the steel, and make it easy to rust. In addition, carbon can increase cold brittleness and aging of steel, like 304 and 304L, 304L is low carbon 304.
Silicon (Si)
In the process of making steel, silicon is a reducing agent and oxidizing agent, containing 0.15 – 0.30% of silicon content. If silicon content is more than 0.50-0.60%, silicon significantly improves elastic limit, yield point, and tensile strength, so it is widely used in spring steel. Adding 1.0 – 1.2% silicon in the quenched and tempered steel, strength can be increased by 15 – 20%. The combination of Silicon, Molybdenum, Tungsten and Chromium has the effect of improving the corrosion resistance and oxidation resistance. Low carbon steel containing silicon 1 – 4%, with high permeability, is used in the electrical industry silicon steel sheet. Silicon content increasing, not good for welding.
Manganese (Mn)
In the process of making steel, manganese is a good agent and desulfurization agent, manganese content in common steel of 0.30 – 0.50%. Carbon steel, adding more than 0.70% manganese, not only has enough toughness, but has higher strength and hardness, improves steel quenching and performance of thermal processing. Manganese content increased, weakened the corrosion resistance of steel, and reduced the welding performance. Manganese can improve the strength of steel.
Phosphorus (P)
In general, phosphorus is a harmful element in steel, increasing the cold brittleness of steel to result in welding performance deterioration, and reducing ductility to influence the cold bending performance. It usually requires the phosphorus content in steel to be less than 0.045%.
Sulfur (S)
Sulfur in normal circumstances is also a harmful element. generating heat, reducing ductility and toughness. Sulfur on the welding performance is also bad, reducing corrosion resistance. So the sulfur content is less than 0.055%. The requirement of high-quality steel is less than 0.040% of sulfur. The addition of 0.08-0.20% to the steel can improve the machinability, often referred to as free-cutting steel
Chromium (Cr)
Chromium can improve oxidation resistance and corrosion resistance, so it is an important alloying element of stainless steel. In structural steel and tool steel, chromium can significantly improve the strength, hardness, and wear resistance, but at the same time reduce ductility and toughness
Nickel (Ni)
Nickel element can improve the strength of steel, and maintain good ductility and toughness. Nickel has higher corrosion resistance to acid and alkali and has the ability of anti-rust and heat resistance at high temperatures. Improve toughness, so that the steel has high strength, but also maintains good ductility and toughness. Nickel can improve corrosion resistance and low-temperature impact toughness. Nickel-based alloys have a higher thermal performance
Molybdenum (Mo)
Molybdenum can make the grain refinement, and improve the quenching and thermal properties. Under high temperatures to maintain sufficient strength and creep resistance (long-term at high temperature under stress, deformation, said creep). Mechanical properties can be improved with the addition of molybdenum in structural steel
Titanium (Ti)
Titanium steel is a strong deoxidizing agent, making the internal structure of the steel dense, fine grain size, and reducing the aging sensitivity and cold brittleness. Improving the welding performance. Adding proper titanium to Austenitic stainless steels, avoiding Intergranular corrosion
Copper (Cu)
Copper can improve the strength and toughness, especially in atmospheric corrosion performance. The disadvantage is prone to cracking during thermal processing, and the copper content of more than 0.5% ductility is significantly reduced. When the copper content is less than 0.50%, no effect on the welding property
Nitrogen (N)
Nitrogen can improve the strength of steel.
References
- https://en.wikipedia.org/wiki/Stainless_steel
- https://www.aperam.com/stainless/what-is-stainless-steel/
- https://www.assda.asn.au/benefits-of-stainless-steel
- https://stainless-steel-world.net/