There are many stainless steel finishes for option, these finishes vary from dull to mirror-like and have a special surface appearance, rough surface finishes are appropriate to some applications, and smooth surface finishes are better where the steel will be processed to the desired surface effect.
Selecting the right stainless steel finish for your application is very important. You are probably looking for a long lifespan, corrosion resistance and low maintenance needs. The right finishing is the way to guarantee that stainless steel will behave as expected, therefore, It is important to understand stainless steel finishes.
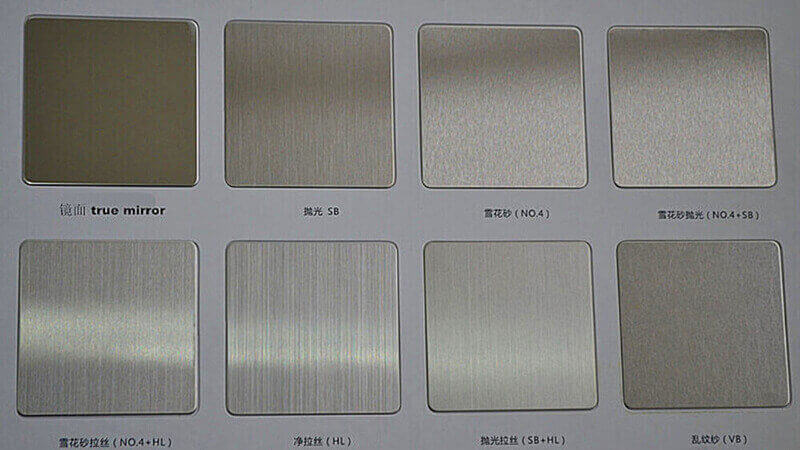
What Is Stainless Steel Finish?
Stainless steel is an alloy group having special properties, it must contain a minimum of 10.5% Chromium content, which is a necessary element, this is an extremely thin but stable and passive Chromium-rich oxide film on the surface to resist corrosion, with the addition of other elements, increasing the properties make it is a wide used material. Stainless Steel Finish is the visual appearance of the metal and is created through various processing methods, including rolling, polishing, and blasting. These finishes range from dull to bright and include special textures that may be mechanically applied for highly specialized applications.
Types of Stainless Steel Finishes
Multiple finishes for opting are an important advantage of stainless steel, compared to other metals. There are many different finishes on stainless steel, some finishes are generated from the mill, like 2B finish, and some finishes can be achieved from the fabrication process, standard finishes are categorized as either “Mill” or “Polished” based on ASTM A480 specification.
Mill Finishes
Mill finishes are the basic surface of stainless steel flat products, without additional processing, hot rolled finishes are usually dark and dull surfaces, when in heat treated and hot rolling condition, mill finishes surface is pickled to remove scale, it includes No. 1, No. 2D and No. 2B.
Polished Finishes
Polishing is a method of finishing the surface of material through the use of flexible polishing tools and abrasive particles, with the main objective of reducing the roughness of the surface of the workpiece to obtain a bright, flat surface. Polishing does not improve the dimensional or geometric accuracy of the workpiece, but rather focuses on achieving a smooth or mirror-gloss surface.
There are various methods of polishing treatments, commonly including mechanical polishing, chemical polishing and electrochemical polishing. Mechanical polishing typically uses a polishing wheel, which rolls and micro-cuts the surface of the workpiece with a high-speed rotating wheel to achieve a smooth surface. Chemical polishing, on the other hand, uses chemical reactions to remove tiny bumps on the surface of the workpiece to achieve a smooth finish. Electrochemical polishing, on the other hand, removes material from the surface of the workpiece through an electrochemical reaction, and is suitable for the polishing of specific materials.
No. 1
Hot rolled, annealed, pickled, dull non-reflective finish.
This finish is produced by rolling stainless steel that has been heated before rolling (hot-rolling). Very little finishing is required, which is why it is considered rough-finished, No. 1 finish has a rough, dull, and non-uniform appearance.
No. 2D
Cold rolled, annealed, pickled, smooth non-reflective finish.
No. 2D Finish is a uniform, dull silver-gray finish that is applied to thinner coils whose thickness has been reduced by cold rolling. After rolling, the coil is heat treated to produce a uniform microstructure (annealing) and to meet mechanical property requirements. Pickling or descaling is necessary after heat treatment to remove the chromium-depleted dark surface layer and restore corrosion resistance
No. 2B
Cold rolled, annealed, pickled, smooth reflective finish, the most widely used finish.
2B is typical cold rolling, smooth surface, light reflective mill finish, heat treated, it is the most widely used finish, 2B finish is a basic surface condition for many other polished finishes,
This is the most common finish produced and called for on sheet material. It is brighter than 2D is semi-reflective, and is more easily polished to the final finish required than is a 2D finish.
BA
Cold rolled, annealed, pickled, smooth reflective finish, the most widely used finish.
Bright Annealed (BA) is produced by heat-treating (annealing) in a controlled atmosphere furnace. It has a mirror-like appearance but may have some cloudiness and other imperfections.
No. 3
Non-reflective finish, light polishing using the grinding belt, 100 – 120 grit.
It is obtained by either mechanically polishing with gradually finer abrasives or by passing the coil through special rolls, which press a pattern into the surface, simulating the appearance of mechanical abrasion. It has a moderately reflective finish
No.4 – Brushed Finish
Reflective dull polishing, brushed finish, using 120 – 320 grit belt after light grinding.
Brushed finish has a strong decorative surface, and is not too reflective, it is one of the most popular finishes available, particularly for kitchen appliances, there is a light groove on the surface of stainless steel, so it is not suitable for used corrosion environment, because this finish may lead to corrosion attack, it is applied in ornamental purpose in the most case, the final finish can be anywhere between 120 and 320 grit. Higher grit numbers produce finer polishing lines and more reflective finishes.
No. 6
Cold rolled, dull satin finish by Tampico brushing a No.4 finish.
A dull, silver-white finish with relatively short linear polishing lines. It has a lower reflectivity than the No. 4 finish. It is produced by Tampico brushing a No. 4 finish sheet in an oil and abrasive medium
No. 7
High reflective finish, by a finely ground surface, 320 grit is buffed.
No. 7 Finish has a high degree of reflectivity and a mirror-like appearance. A No. 4 finish that has been polished to 320 grit is buffed for up to 10 minutes, but existing grit lines are not removed.
No.8 – Mirror finish
High reflective, bright polishing, smooth surface, mirror finish.
Mirror finish is a highly reflective surface by polishing, It is produced in the same manner as the No. 7 finish except that the buffing is continued for an additional five to ten minutes. In comparison to a No. 7 finish, the grit lines are much less visible, but they can be seen if the finish is examined closely. The resulting finish is mirror-like but not a perfect mirror.
Electro-Polished Finishes
Electropolishing is an advanced industrial metal finishing process also known as electro-chemical or electrolytic polishing that is used as an alternative to abrasive polishing methods. It has the benefit of often being less time-consuming and more thorough than conventional mechanical finishing.
Electropolishing is often compared to electroplating, another method of altering a metallic object’s surface. However, instead of adding layers of material to the surface, it draws out the impurities at the surface.
This leaves the surface smooth, highly polished, and free of burrs – and unlike with chrome-plating or similar finishing techniques, and electropolished finish doesn’t chip or peel away.
The precision of the electropolishing process is an advantage over mechanical polishing, which can lead to a noticeable decrease in the dimensions of a metal part, and it can be controlled to remove less than a ten-thousandth of an inch
from the surface.
Patterned Finishes
Stainless steel sheets can be given patterned rolled finishes. BS EN 10088-2 covers the specification of both hot and cold rolled products with a one-side patterned only as a special finish “M”. This includes “chequer” plates (“1” ex-mill finish) and fine textures finishes (“2” ex-mill finish). The specific design of the patterns is not defined in the standard and has to be agreed upon.
These three-dimensional relief effect patterns can be produced by either texture rolling or pressing (embossing). BS EN 10088-2 only covers single-sided patterns with a plain, flat surface on the reverse side. Products are also available with a reversed relief effect
pattern on both sides. These are formed by rolling sheets through pairs of mating, matched male-female patterned rolls.
Colored Finishes
Stainless steel can be colored either by the application of paint or by chemical treatments. Paint systems rely upon introducing a second layer of material onto the surface whereas chemical systems rely upon altering the thickness and nature of the passive film on the stainless steel item. A particular attraction of chemically colored stainless steel is that it appears to change color under different shades and angles of artificial and natural light.
The process is normally restricted to cold rolled sheet products, and although it is possible to color fabricated components. Chemical coloring of stainless steel sheets uses a mixture of chromic and sulphuric acids that develop the thickness of the naturally occurring passive film on the steel surface, depending on the immersion time.
Brushing
Although brushing normally involves the use of a fine abrasive action on the surface of the metal, in contrast to grinding and polishing there is no deliberate attempt to remove a surface layer. Rather it is modified by the action of bristles or a nylon fabric medium, (Scotch-Brite), that may have some fine abrasive or lubricant included.
Although it can be a single-stage process, following a suitable polishing preparation stage, brushing can be done in several stages to obtain a particular finish. Brushed finishes have the same special finish code, 2J in BS EN 10088-2 as dull polished.
Buffing
In buffing no attempt is made to remove metal from the surface. Buffing is only intended to smooth and brighten the existing surface. Traditionally buffing uses cotton or felt-based media, often with lubricants applied to the buffing wheel.
Whenever buffing is considered as the final finishing operation, the pretreated, (or existing), surface must be defined and controlled. Buffing cannot be used as a substitute for polishing to obtain finishes such as 1P/2P on ‘intermediate’ abraded ground or polished surfaces. It will only smooth down the surface and will not impart the same characteristics as if the surface has been abraded with successively finer grit sizes, (i.e. as in polishing).
Buffing cannot be used as a shortcut to obtaining a polished finish. If the surface that is to be finished by buffing is too coarse, there is a risk that traces of the underlying surface finish will be visible on the finally buffed surface.
Ground and Polished (satin) Finishes
Mechanically ground and polished finishes for stainless steel flat products are specified in BS EN 10088-2 in Table 6 as ‘special finishes’. Typical Ra surface roughness measurements in micro-meters are based on manufacturers’ or surface finishing contractors’ data. Normally only one surface is required to meet the agreed standard of finish. Stainless steel long products to BS EN 10088-3 only have two special finishes defined G, centreless ground, and P, polished.
Abbreviation | Finishing Process Route | Notes | Typical (Ra) micro-metres |
---|---|---|---|
1G or 2G | Ground | Can be based on either 1 or 2 ex-mill finishes. Smoother than G with a unidirectional texture, not very reflective. The grade of brush or polishing belt or surface roughness can be specified. | – |
1J or2J | Brushed or dull polished | Can be based on either 1 or 2 ex-mill finishes. Smoothest of the special non-reflective finishes supporting the appropriate steel types’ corrosion resistance for most external applications and marine environments. Transverse Ra should be below 0.5 micro m. with clean-cut surfaces. | 0.5-1.5 |
1K or 2K | Satin polished | Can be based on either 1 or 2 ex-mill finishes. Smoothest of the special non-reflective finishes supporting the appropriate steel types’ corrosion resistance for most external applications and marine environments. Transverse Ra should be below 0.5 micro m. with clean cut surfaces. | less than 0.5 |
1P or 2P | Bright polished | Can be based on either 1 or 2 ex-mill finishes. Mechanically polished non-directional reflective finish with a high degree of image clarity (includes mirror finishes). | less than 0.1 |
Buffed finishes
There is currently no provision for specifying buffed finishes on stainless steel flat products in BS EN 10088-2. BS 1449-2 (1983), which was replaced by BS EN 10088-2, was the previous standard for stainless steel flat products and did define two buffed finishes, 3B, dull buffed and 7, bright buffed. The American standard that defines stainless steel flat product finishes, ASTM A480 also includes a No 7 bright buffed finish. A comparison of buffed, ground and polished finishes is included in the table below. Note there is no No5 finish in ASTM A480.
The table shows how the BS EN 10088-2 flat product codes compare with the superseded BS 1449-2 and DIN
BS EN Code | Description | BS 1449-2 | DIN | ASTM |
---|---|---|---|---|
1D | Hot rolled, heat treated, pickled | 1 | IIa (c2) | 1 |
2B | Cold rolled, heat treated, pickled, skin passed | 2B | IIIc (n) | 2B |
2D | Cold rolled, heat treated, pickled | 2D | IIIb (h) | 2D |
2R | Cold rolled, bright annealed | 2A | IIId (m) | BA |
2G | Cold rolled, ground | 3A | – | No.3 |
2J | Cold rolled, brushed or dull polished | 3B (or 4) | – | No.4 |
2K | Cold rolled, satin polished | 5 | – | No.6 |
2P | Cold rolled, bright polished | 8 | – | No.8 |
What is the Surface Roughness of Stainless Steel?
Surface roughness is a measure of the texture of a manufactured surface. RA or Average roughness is most commonly used in North America. It is the average of the peaks and valleys of a surface over a set sampling length. Values are typically given in microinches or micrometers.
Rz, or mean roughness depth, is most commonly used in Europe and is the average of the highest peak to the lowest valley over 5 sampling lengths.
Surface roughness can have a crucial impact on the durability and performance of the material and must also be closely considered and controlled.
Stainless Steel Finishes, Grit And Roughness
Metal surface roughness is measured using special means, Ra is a roughness unit, roughness of different finishes has different values.
There is no standard to specify stainless steel finish’s relation with roughness value Ra, in practice, they can be roughly converted as follows:
Common Name | Ra (um) | Grit Number | USA Finish |
---|---|---|---|
50 | — | — | |
25 | — | — | |
12.5 | — | — | |
Mill Plate | 6.3 | 60 | #1 |
3.2 | — | — | |
Satin Sheet | 1.75 max, 1-1.5 | 80 | #2 |
1.6 | — | — | |
1.3 | 100 to 120 | #3 | |
Commercial #4 | 1-1.5 | 120 | #4 |
Sanitary/Dairy Finish | 1.05 max, 0.75-0.875 | 150 | #4 |
ANSI #4 | 0.8 | — | — |
3A Sanitary Finish | 0.8 max, 0.5-0.8 | 180 | #4 |
Biotech Finish | 0.625 max, 0.5-0.625 | 200 to 220 | #4 |
Fine Satin Finish | 0.375-0.5 | 240 | #6 |
0.4 | — | — | |
Semi-Bright Finish | 0.3 max, 0.2-0.3 | 320 | #7 |
0.3 | — | — | |
0.2 | — | — | |
Mirror Finish | 0.1-0.2 | 400 | #8 |
Supermirror Finish | <0.1, 0.075-0.2 | 500 | #8 |
Supermirror Finish | 0.1 | 500 | #8 |
0.05 | — | — | |
0.025 | — | — |