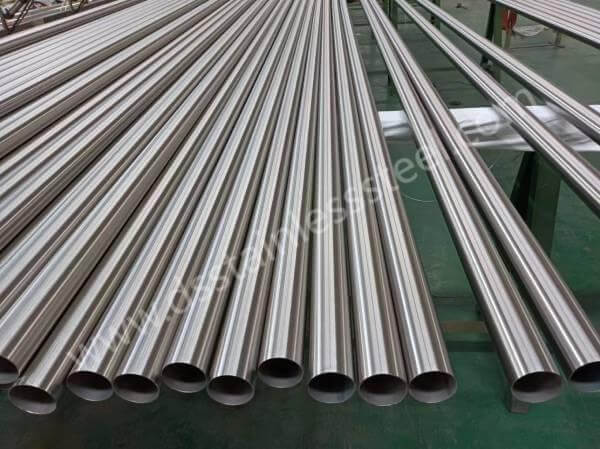
We offer polished stainless steel tubing and pipe with a wide range of sizes, polished welded tubing undergoes multiple passes through the polishing heads to remove any unwanted residue to achieve a bright surface, and inner and outer surfaces are polished to achieve a smooth surface, mechanical polishing and electro polished are the two methods to polish stainless steel tube.
Polished stainless steel tubing forms have round tubing, square tubing and rectangular tubing in standard 180 grit, 240 grit, 320 grit and mirror finishes, tube sizes range from OD ½” to 8″ and wall thickness 0.049″ to 0.250″.
Stainless Steel Grades
There are a variety of stainless steel grades for polished tubing, they are also food-grade stainless steels, exhibiting high strength and excellent corrosion resistance, common grades include 304, 304L and 316L.
Grade | C | Mn | P | S | Si | Cr | Ni | Mo |
---|---|---|---|---|---|---|---|---|
304 | 0.08 | 2 | 0.045 | 0.03 | 1 | 18 – 20 | 8 – 11 | |
304L | 0.035 | 2 | 0.045 | 0.03 | 1 | 18 – 20 | 8 – 13 | |
316L | 0.035 | 2 | 0.045 | 0.03 | 1 | 16 – 18 | 10 – 14 | 2 – 3 |
304 and 316 are the two most common stainless steel grades used for stainless steel tubing. Other advantages of stainless steel are its superior corrosion resistance, ease of cleaning, low maintenance requirements, and low cost. Although stainless steel may have a greater starting cost than other metals, stainless steel tubes have cheaper maintenance and replacement costs.
Advantages Of Polished Tubing
Polished finishing makes welding seam integrity with base metal after heat treatment, and have a visible bright surface, furthermore, it can make a uniform and smooth surface, and is easy to clean, with no dark scale on the tubing surface, polished tubing has a low Ra value in roughness, it is a value-adding service.
- Improve surface finish and “RA” Value
- Reduce product adhesion
- Improve surface cleanability and form a reflective surface
- Improve aesthetic appeal
- Remove scales and oxidation
- Prevent corrosion
ASTM A270 And 3A Polished Tubing
Stainless Steel Welded Tubing is usually polished conforming to ASTM A270 and 3A standards, this polished tubing undergoes multiple passes through the polishing heads to remove any unwanted residue on interior and exterior surfaces.
This tubing undergoes a rigorous quality inspection, including destructive and non-destructive examination, at the mill before shipment.
There are several polishing types of equipment to use, either outside surface or inside surface, we can offer sanitary and food grade standards for special applications.
Stainless Steel Polished Grits
- 120 grit
- 180 grit
- 320 grit
- 400 grit
- 600 grit
- 800 grit
Polishing Measurement
Ra refers to the roughness average, which is the measure of the roughness of a surface and is measured in micrometers (μm), Ra value describes the Average scratch depth of the tubing surface, the lower the Ra value, the smoother and more polished the surface, we provide minimum Ra value is 0.05 μm, “Ra,” or surface roughness, is confirmed using microscopic and profilometry testing.
Polished Stainless Steel Tubing Sizes
Outside Diameter | Nominal Wall Thickness | Weight | ||
---|---|---|---|---|
(in) | (mm) | (in) | (mm) | (kg/m) |
1/2 | 12.7 | 0.065 | 1.65 | 0.454 |
3/4 | 19.1 | 0.065 | 1.65 | 0.717 |
1 | 25.4 | 0.065 | 1.65 | 0.976 |
1 1/2 | 38.1 | 0.065 | 1.65 | 1.50 |
2 | 50.8 | 0.065 | 1.65 | 2.02 |
2 1/2 | 63.5 | 0.065 | 1.65 | 2.54 |
3 | 76.2 | 0.065 | 1.65 | 3.06 |
4 | 101.6 | 0.083 | 2.11 | 5.23 |
6 | 152.4 | 0.109 | 2.77 | 10.32 |
8 | 203.2 | 0.109 | 2.77 |
Polished Stainless Steel Tubing Applications
Stainless steel polished tube is widely used in food processing, bear, beverage, and drinking water, it is also used for construction purposes, like handrails requires a bright surface, and polishing inside surface for stainless steel sanity tubing conforming to ASTM A270 specification.
- Food, Beverage, and Dairy
- Pharmaceuticals
- Handrail
- Kitchen equipment
- Exhaust pipe
Mechanical Polishing
Mechanical Polishing is a process of grinding the surface of the metal using an abrasive belt and mechanical tools at multiple stages to achieve a desired smooth surface and roughness value, meanwhile, it alters the microstructure of the surface.
Stainless steel tubing is polished mechanically to pass through a set of abrasive wheels and tapes with a polishing machine, with polishing paste to improve polishing efficiency, finally, this process makes the desired polishing level using the different grinding belts to remove the surface layer.
There are Dry and Wet mechanical polishing for selecting, wet style is a better option.
Electropolishing
Electropolishing is a process that uses a metal workpiece as an anode and performs electrolysis in a suitable electrolyte to selectively remove its rough surface and improve the surface finish, it is also called Electrochemical or anodic polishing.
Theory
During electropolishing, current flows on the surface of the metal product as the anode, which will form an oxide film, a salt film, or an oxygen adsorption layer on the surface, so that the metal dissolution rate of the anode drops sharply, that is, in a passive state. But this passivation film layer may be dissolved in the electrolyte, and the anode is reactivated. At a certain current density, metal passivation and metal dissolution proceed alternately.
Electrolyte
The electrolyte usually uses phosphoric acid as the main component, and it also needs to add certain oxidants (such as sulfuric acid, chromic anhydride, etc.). Without electricity, the electrolyte should have no significant corrosive effect on the metal being polished. It also requires that the electrolyte has a high solubility for the anode dissolution product and is easily removed. In addition, the electrolyte is required to have good stability, low cost and low toxicity. If necessary, a small number of organic substances (such as glycerin, methylcellulose, etc.) can be added to the electrolyte as a corrosion inhibitor. Use perchloric acid-acetic acid electrolyte for electropolishing to obtain a high-finish surface.
Process
After being energized, a polarized film is formed on the surface of the polished metal, allowing metal ions to diffuse through this thin flag. The current density of microscopic and macroscopic bumps or rough spots on the surface and the burr area is greater than the rest of the surface, and it dissolves at a faster rate to achieve the purpose of leveling and deburring. By prolonging the polishing time, and increasing the polishing temperature and current density, a bright surface can be obtained.
Mechanical Polishing Vs. Electropolishing
Mechanical Polishing and Electropolishing are the main methods to polish stainless steel tubing, mechanical polishing performs well for general industries, when a higher polishing level is required, like in the pharmaceutical and semiconductor industries, Electropolishing has its advantages.
- Improve Cleanability
- Enhance Durability
- Improve Sterility
- Increase Corrosion Resistance
Mechanically polished surfaces retain the basic alloy composition with only slight depletion of the other alloy elements, whereas electropolished surfaces contain essentially only chromium and iron, and no stress resides.