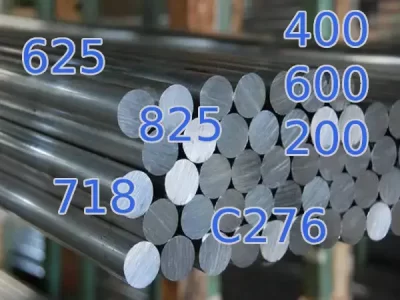
Nickel alloy is an alloy with nickel as a base element, generally referring to alloys containing more than 50% nickel, Nickel is a vital and versatile element to combine with other alloys to achieve outstanding heat and corrosion resistance.
Nickel alloys play an important role in use in tough industrial environments, due to their many characteristics and advantages, they have excellent resistance to oxidation and corrosion, high strength and are easily welded, these properties make them suitable for use in very high and low temperatures conditions.
Nickel-containing stainless steels exhibit important properties in formability, weldability and ductility while increasing corrosion resistance in certain applications, there are 75% of stainless steels contain Nickel element.
Nickel Alloy Composition
Alloy | UNS | Nickel | Copper | Iron | Manganese | Carbon | Silicon | Sulfur | Other |
---|---|---|---|---|---|---|---|---|---|
Monel 400 | N04400 | 63.0min | 28.0-34.0 | 2.50max | 2.00max | 0.30max | 0.50max | 0.024max | |
Inconel 600 | N06600 | 72.0min | 0.50max | 6.00-10.00 | 1.00max | 0.15max | 0.50max | 0.015max | Cr: 14.0-17.0 |
Inconel 601 | N06601 | 58.0-63.0 | 1.00max | Bal. | 1.00max | 0.10max | 0.50max | 0.015max | Al: 1.00-1.70 Cr: 21.0-25.0 |
Inconel 625 | N08825 | 58.0min | 5.00max | 0.50max | 0.10max | 0.50max | 0.015max | Co: 1.00max Al: 0.40max Ti: 0.40max Cr: 20.00-23.00 Mo: 8.00-10.00 P: 0.015max Nb: 3.15-4.15 | |
Incoloy 800 | N08800 | 30.0-35.0 | 0.75max | 39.50min | 1.50max | 0.10max | 1.00max | 0.015max | Al:0.15-0.60 Ti: 0.15-0.60 Cr:19.0-23.0 |
Incoloy 800H | N08810 | 30.0-35.0 | 0.75max | 39.50min | 1.50max | 0.05-0.10 | 1.00max | 0.015max | Al: 0.15-0.60 Ti: 0.15-0.60 Cr: 19.0-23.0 |
Incoloy 800HT | N08811 | 30.0-35.0 | 075max | 39.5min | 1.50max | 0.06-0.10 | 1.00max | 0.015max | Al: 0.85-1.20 Ti: 0.25-0.60 Cr: 19.0-23.0 |
Incoloy 825 | N08825 | 38.0-46.0 | 1.50-3.00 | 22.00min | 1.00max | 0.05max | 0.50max | 0.03max | Al: 0.20max Ti: 0.60-1.20 Cr: 19.50-23.50 Mo: 2.50-3.50 |
C-276 | N10276 | Bal. | 4.00-7.00 | 1.00max | 0.01max | 0.08max | 0.03max | Co: 2.50max Cr: 14.50-16.50 Mo: 15.00-17.00 Tu: 3.00-4.50 Va:0.35max P: 0.04max | |
Alloy 020 | 32.00-38.00 | 3.00-4.00 | Bal. | 2.00max | 0.07max | 1.00max | 0.035max | Cr: 19.00-21.00 Mo: 2.00-3.00 |
Nickel Alloy Equivalents
GB/T | ASTM | UNS | W.Nr. / EU | Alloy Company |
---|---|---|---|---|
Ni68Cu28Fe | Monel400 | N04400 | 2.436 | Monel 400(SMC) |
– | K500 | N05500 | 2.4375 | Monel K500(SMC) |
1Cr15Ni75Fe | 600 | N06600 | 2.4816 | Inconel 600(SMC) |
1Cr23Ni60Fe13Al | 601 | N06601 | 2.4851 | Inconel 601(SMC) |
20Cr25Ni60Fe10AlY | 602 | N06025 | 2.4633 | Nicrofer 6025HT(VDM) |
– | 617 | N06617 | 2.4663 | Inconel 617(SMC) |
0Cr20Ni65Mo10Nb4 | 625 | N06625 | 2.4856 | Inconel 625(SMC) |
0Cr30Ni60Fe10 | 690 | N06690 | 2.4642 | Inconel 690(SMC) |
0Cr20Ni32AlTi | 800 | N08810 | 1.4558 | Incoloy 800(SMC) |
1Cr20Ni32AlTi | 800H | N08810/8811 | 1.4876 | Incoloy 800H(SMC) |
0Cr21Ni42Mo3Cu2Ti | 825 | N08825 | 2.4858 | Incoloy 825(SMC) |
00Cr15Ni60Mo16W5Fe5 | C276 | N10276 | 2.4819 | Hastelloy C276(Haynes) |
00Cr17Ni57Mo13W3 | C22 | N06022 | 2.4602 | Hastelloy C22(Haynes) |
– | C2000 | N06200 | 2.4675 | Hastelloy C2000(Haynes) |
00Ni70Mo28 | B2 | N10665 | 2.4617 | Hastelloy B2(Haynes) |
00Mo28Ni65Fe1.5Cr1.5 | B3 | N10675 | 2.46 | Hastelloy B3(Haynes) |
0Cr20Ni35Mo3Cu3Nb | Alloy 20 | N08020 | 2.466 | Incoloy 020(SMC) |
00Cr27Ni31Mo3Cu | Alloy 28 | N08028 | 1.4563 | Sanicro 28 |
00Cr27Ni31Mo7CuN | Alloy 31 | N08031 | 1.4562 | Nicrofer 3127hMo(VDM) |
00Cr22Ni48Mo7Cu2Nb | G3 | N06985 | 2.4619 | Hastelloy G3(Haynes) |
00Cr30Ni43Mo5.5W2.5Cu2Nb | G30 | N06030 | 2.4603 | Hastelloy G30(Haynes) |
0Cr33Ni55Mo8 | G35 | N06035 | 2.4643 | Hastelloy G35(Haynes) |
0Cr15Ni70Ti3AlNb | X750 | N07750 | 2.4669 | Inconel X750(SMC) |
Types Of Nickel Alloy
- Pure nickel
- Nickel-Iron Alloys
- Nickel-Copper Alloys
- Nickel-Chromium Alloys
- Nickel-Molybdenum Alloys
- Nickel-Chromium-Iron Alloys
- Nickel-Chromium-Molybdenum Alloys
- Nickel-Chromium-Cobalt Alloys
- Nickel-Titanium Alloys
Nickel-based Alloys List
- Inconel 600: good resistance to high-temperature corrosion and oxidation resistance, excellent hot and cold processing and welding performance, below 700 ℃ with satisfactory thermal strength and high plasticity;
- Inconel 625: excellent resistance to pitting, crevice corrosion, intergranular corrosion and erosion in chloride media; acid-resistant and good weldability; low-cycle fatigue (English: Low-cycle fatigue) version of Inconel 625 is commonly used for bellows.
- Inconel 690: lower cobalt content, suitable for nuclear energy-related applications, and lower resistivity, such as pressurized water reactor nuclear power plant steam generator heat transfer tube is 690 material.
- Inconel 713C: precipitation-hardened nickel-chromium-based casting alloy.
- Inconel 718: with γ’ phase strengthening phase, welding performance is better.
- Inconel 751: add more aluminium content, so that the high-temperature range near 870 ℃ has a good breaking strength.
- Inconel 792: add more aluminum content, so that it has more corrosion resistance at high temperatures, suitable for the manufacture of gas turbines.
- Inconel 939: γ’ phase strengthening to increase welding performance.
- Incoloy 020: Excellent corrosion resistance in chemical environments containing sulphuric acid, chlorides, phosphoric acid and nitric acid.
- Incoloy 028: Resistant to both acids and salts, the copper content makes it resistant to sulphuric acid.
- Incoloy 330: Exhibits good strength at elevated temperatures and good resistance to oxidizing and reducing environments.
- Incoloy 800: Excellent resistance to stress corrosion rupture in chlorides, low concentrations of NaOH in aqueous solutions, and high temperature and pressure water, remaining stable and retaining its austenitic structure even after prolonged exposure to high temperatures.
- Incoloy 803: Designed for sulfur-rich environments.
- Incoloy 825: Excellent corrosion resistance in reducing and oxidizing acids, resistance to stress corrosion cracking, pitting and crevice corrosion, excellent corrosion resistance to sulphuric and phosphoric acid and good hot and cold working properties, easy cold forming and welding.
- Incoloy 908: High tensile strength, resistance to fatigue crack extension, good weldability, metallurgical stability and ductility, high fracture and impact toughness, low coefficient of thermal expansion, resistance to oxygen embrittlement, and non-cracking properties for hot working.
- Incoloy 907: High strength and low coefficient of thermal expansion at elevated temperatures.
- Incoloy 945X: Designed for chlorine-rich environments, molybdenum increases its crevice corrosion and pitting resistance.
- Incoloy MA956: Made by mechanical alloying rather than a monolithic melting process, it is difficult to weld and needs to be heated to 200C to form.
- Monel 400: High strength and excellent corrosion resistance in acidic and alkaline environments, particularly suitable for reducing conditions, it also has good ductility and thermal conductivity. Typical applications are in marine engineering, chemical and hydrocarbon processing, heat exchangers, valves and pumps.
- Monel 401: Characterised by easy tungsten inert gas shielded welding, resistance welding and brazing. Used for specialized electrical and electronic applications.
- Monel 404: Can be welded and forged using common welding techniques but cannot be hot worked, has low temperature, low permeability and good brazing properties. Typically used for transistors and metal seals.
- Monel 405: Easy to cut, mainly used as raw material for automatic screw machines, generally not recommended for other applications.
- Monel 450: Good fatigue strength and high thermal conductivity. They are generally used for condenser, distiller, evaporator and heat exchanger tubes and brine piping.
- Monel K-500: Has essentially the same properties as Monel 400 and is commonly used in pump shafts, impellers, scrapers, oil well drill collars, instruments and electronic components.
- Monel 502: has good creep resistance and oxidation resistance, and can also be processed like austenitic stainless steel.
- Hastelloy B-2: Excellent corrosion resistance in reducing environments.
- Hastelloy B-3: An upgraded version of B2 with excellent corrosion resistance to hydrochloric acid at any temperature and concentration;
- Hastelloy C-4: better thermal stability, good toughness corrosion resistance at 650~1040°C;
- Hastelloy C-22: uniform corrosion resistance in oxidizing media is better than C-4 and C-276, with excellent resistance to localized corrosion;
- Hastelloy C-276: good resistance to oxidizing and moderate reducing corrosion, excellent resistance to stress corrosion;
- Hastelloy C-2000: the most versatile corrosion-resistant alloy with excellent resistance to uniform corrosion in both oxidizing and reducing environments;
- Hastelloy G-30: a high chromium content nickel-based alloy with excellent performance in phosphoric acid and other strong oxidizing mixed acid media;
- Hastelloy X: Combined high strength, oxidation resistance and ease of processing.
Nickel Alloy Standard Specifications
- ASTM B160 Standard Specification for Nickel Rod and Bar
- ASTM B162 Standard Specification for Nickel Plate, Sheet, and Strip
- ASTM B127 Standard Specification for Nickel-Copper Alloy Plate, Sheet, and Strip
- ASTM B163(ASME SB163) Standard Specification for Seamless Nickel and Nickel Alloy Condenser and Heat-Exchanger Tubes
- ASTM B164 Standard Specification for Nickel-Copper Alloy Rod, Bar, and Wire
- ASTM B165(ASME SB165) Standard Specification for Nickel-Copper Alloy Seamless Pipe and Tube
- ASTM B166 Standard Specification for Nickel-Chromium-Aluminum Alloy, Nickel-Chromium-Iron Alloys, Nickel-Chromium-Cobalt-Molybdenum Alloy, Nickel-Iron-Chromium-Tungsten Alloy, and Nickel-Chromium-Molybdenum-Copper Alloy Rod, Bar, and Wire
- ASTM B167(ASME SB167) Standard Specification for Nickel-Chromium-Aluminum Alloys (UNS N06699), Nickel-Chromium-Iron Alloys (UNS N06600, N06601, N06603, N06690, N06693, N06025, N06045, and N06696), Nickel-Chromium-Cobalt-Molybdenum Alloy (UNS N06617), Nickel-Iron-Chromium-Tungsten Alloy (UNS N06674), and Nickel-Chromium-Molybdenum-Copper Alloy (UNS N06235) Seamless Pipe and Tube
- ASTM B168 Standard Specification for Nickel-Chromium-Aluminum Alloys (UNS N06699), Nickel-Chromium-Iron Alloys (UNS N06600, N06601, N06603, N06690, N06693, N06025, N06045, and N06696), Nickel-Chromium-Cobalt-Molybdenum Alloy (UNS N06617), Nickel-Iron-Chrom
- ASTM B333 Standard Specification for Nickel-Molybdenum Alloy Plate, Sheet, and Strip
- ASTM B408 Standard Specification for Nickel-Iron-Chromium Alloy Rod and Bar
- ASTM B407(ASME SB407) Standard Specification for Nickel-Iron-Chromium Alloy Seamless Pipe and Tube
- ASTM B409 Standard Specification for Nickel-Iron-Chromium Alloy Plate, Sheet, and Strip
- ASTM B423(ASME SB423) Standard Specification for Nickel-Iron-Chromium-Molybdenum-Copper Alloy (UNS N08825, N08221, and N06845) Seamless Pipe and Tube
- ASTM B424 Standard Specification for Nickel-Iron-Chromium-Molybdenum-Copper Alloys Plate, Sheet, and Strip
- ASTM B443 Standard Specification for Nickel-Chromium-Molybdenum-Columbium Alloy and Nickel-Chromium-Molybdenum-Silicon Alloy Plate, Sheet, and Strip
- ASTM B444(ASME SB444) Standard Specification for Nickel-Chromium-Molybdenum-Columbium Alloys (UNS N06625 and UNS N06852) and Nickel-Chromium-Molybdenum-Silicon Alloy (UNS N06219) Pipe and Tube
- ASTM B446 Standard Specification for Nickel-Chromium-Molybdenum-Columbium Alloy (UNS N06625), Nickel-Chromium-Molybdenum-Silicon Alloy (UNS N06219), and Nickel-Chromium-Molybdenum-Tungsten Alloy (UNS N06650) Rod and Bar
- ASTM B564 Standard Specification for Nickel Alloy Forgings
- ASTM B575 Standard Specification for Low-Carbon Nickel-Chromium-Molybdenum, Low-Carbon Nickel-Chromium-Molybdenum-Copper, Low-Carbon Nickel-Chromium-Molybdenum-Tantalum, Low-Carbon Nickel-Chromium-Molybdenum-Tungsten, and Low-Carbon Nickel-Molybdenum-Chromium
- ASTM B622(ASME SB622) Standard Specification for Seamless Nickel and Nickel-Cobalt Alloy Pipe and Tube
- ASTM B637 Standard Specification for Precipitation-Hardening and Cold Worked Nickel Alloy Bars, Forgings, and Forging Stock for Moderate or High Temperature Service
- ASTM B668(ASME SB668) Standard Specification for UNS N08028 and N08029 Seamless Pipe and Tube
- ASTM B690(ASME SB690) Standard Specification for Iron-Nickel-Chromium-Molybdenum Alloy (UNS N08367) Seamless Pipe and Tube
- ASTM B670 Standard Specification for Precipitation-Hardening Nickel Alloy (UNS N07718) Plate, Sheet, and Strip for High-Temperature Service
- ASTM B729(ASME SB729) Standard Specification for Seamless Nickel-Iron-Chromium-Molybdenum-Copper Nickel Alloy Pipe and Tube
- ASTM B865 Standard Specification for Precipitation Hardening Nickel-Copper-Aluminum Alloy Bar, Rod, Wire, Forgings, and Forging Stock
Properties of Nickel Alloy
- Corrosion resistance: nickel alloy has excellent corrosion resistance in aqueous solutions containing halide ions and is suitable for various corrosive media.
- High-temperature strength: nickel alloy can maintain high strength at high temperatures and has excellent mechanical properties such as resistance to submergence and fatigue.
- Oxidation resistance: nickel alloy shows good oxidation resistance under high-temperature environments.
- Memory: Some special alloys have memory and can recover their original shape under specific conditions.
- Electromagnetic properties: Nickel alloys also have special electromagnetic properties for applications requiring special electromagnetic properties.
- Machinability and weldability: Nickel alloys have good machinability and weldability and are easily machined into a variety of shapes and structures.
Trade Names Of Nickel Alloys
Hastelloy
Hastelloy is the trade name for a range of nickel-based alloys developed and produced by Haynes International, USA. These alloys are known for their excellent corrosion resistance and high-temperature strength, maintaining stable mechanical properties and corrosion resistance in extreme environments. The main components of Hastelloy alloys include elements such as nickel, chromium, molybdenum and iron, and some may also contain other alloying elements such as copper and tungsten to enhance their specific properties.
Hastelloys are divided into several main series, such as B, C, G, etc., each of which optimizes its chemical composition and properties for specific applications.
- Hastelloy B series: Usually containing molybdenum, these alloys are highly resistant to a wide range of non-oxidizing acids, hydrochloric acids, and media containing chlorides.
- Hastelloy C series (e.g. C-276): Containing a high proportion of molybdenum and chromium, as well as tungsten, they exhibit excellent corrosion resistance to oxidizing and non-oxidizing media, especially those containing chlorides.
- Hastelloy G series: Designed to resist corrosion in oxidizing media such as sulphuric and phosphoric acid.
Hastelloy is widely used in the chemical, petrochemical, oil and gas extraction, pulp and paper, nuclear energy, and aerospace industries, especially in equipment that handles or comes into contact with highly corrosive chemicals, such as reaction vessels, heat exchangers, piping systems, and pumps, among other components.
Incoloy
Incoloy alloy is a class of nickel-iron-based alloys, similar to Inconel alloys, with good corrosion resistance, high-temperature strength and heat resistance. Incoloy was first developed by the American company Inco in the 1920s, and is designed to resist oxidation and carbonization at elevated temperatures, Incoloy was later supplemented with other elements such as chromium, molybdenum, cobalt and copper to improve its corrosion resistance and high-temperature performance.
There are many types of Incoloy alloys: common ones such as Incoloy800, Incoloy800H, Incoloy800HT, Incoloy825, Incoloy840, Incoloy901, Incoloy925, Incoloy20, Incoloy330, Incoloy 25- 6Mo, etc.
Inconel
Inconel is a nickel-based alloy widely used in aerospace, astronautics and chemical industries for its high temperature, strength and corrosion resistance. Due to its excellent thermal stability and mechanical properties, Inconel is widely used in the manufacture of high-temperature engine parts, gas turbine blades and chemical reactors, among other demanding applications. Its chemical composition contains elements such as chromium, molybdenum, cobalt and iron, as well as small amounts of carbon, silicon and manganese, in addition to nickel.
Due to its excellent high-temperature mechanical properties and corrosion resistance, Inconel is widely used in a variety of high-temperature industrial applications. In aerospace, it can be used to produce high-temperature parts for jet engines, turbine engine impellers, etc. In the chemical industry, Inconel can be used to manufacture chemical reactors, boiler piping, various high-temperature oxidisers and so on. In addition, Inconel is widely used in nuclear power plants, electric vehicles and high-end manufacturing.
Monel
Monel is a nickel-copper alloy developed and produced by the American company Inco. Monel alloys have excellent corrosion resistance and high-temperature strength. Monel 410, 505, 506 are casting alloys; Monel 410 is a standard casting alloy; Monel 505 and Monel 506 are high-silicon high-strength and high-silicon medium-strength casting alloys; Monel 4XX and 5XX are deformed alloys; Monel 400 is a general-purpose alloy; Monel 404 is commonly used for waveguide materials, and it is a high-copper Monel alloy; Monel K500 is an age-hardening alloy; Monel 501 is an age-hardening alloy with easy-cutting characteristics; Monel 502 is an age-hardening low-carbon, low-titanium alloy; and Monel 406 is a low-carbon, high-nickel alloy.
Monel alloys are used in a wide range of applications including, but not limited to, pump shafts and impellers, conveyor scrapers, oil well drilling rings, elastomeric components, valve gaskets, and more. Due to their excellent corrosion resistance and high strength, Monel alloys are also used in the manufacture of various types of heat transfer equipment, boiler feedwater heaters, petroleum and chemical pipelines, vessels, towers, tanks, valves, pumps, reactors, shafts and more.
Nimonic
Nimonic is a nickel-based alloy with excellent high temperature, high strength and corrosion resistance. Nimonic alloys are mainly made of nickel (Ni) as the base element and contain various alloying elements such as chromium (Cr), cobalt (Co), iron (Fe), molybdenum (Mo), titanium (Ti) and other alloying elements. The reasonable ratio of these elements gives Nimonic alloys excellent high-temperature performance. Specifically, the addition of chromium and aluminum enhances the oxidation resistance of the alloy, titanium and aluminum work together to increase the strength and stability of the alloy, while molybdenum and tungsten help to improve the corrosion resistance of the alloy.
Nimonic high-temperature alloys have excellent mechanical properties including high-temperature strength, oxidation resistance, thermal fatigue strength and low creep. These properties allow Nimonic alloys to perform well in high-temperature environments, withstanding extreme thermal stresses and pressures while maintaining stable performance.
- Nimonic 75: is a low-strength alloy containing chromium (Cr) and cobalt (Co), with excellent high-temperature creep and corrosion resistance, mainly used in the manufacture of catheters and spark plugs, etc.
- Nimonic 80A: A high-strength alloy containing manganese (Mn) and titanium (Ti), with excellent high-temperature strength, high-temperature creep and oxidation resistance. It is mainly used in the manufacture of aero-engine impellers and turbine blades.
- Nimonic 90: a high-strength alloy containing molybdenum (Mo) and aluminium (Al), with very high-temperature strength and high-temperature creep properties, mainly used in the manufacture of fuel elements, fuel tubes and nuclear reactor structures.
- Nimonic 105: a high-strength alloy containing niobium (Nb) and titanium (Ti), with very high high-temperature strength and good creep resistance, mainly used in the manufacture of high-temperature aero-engine components and heat exchangers.
- Nimonic 115 is an ultra-high strength alloy containing tungsten (W) and titanium (Ti), with extremely high high temperature strength, high-temperature creep and oxidation resistance, mainly used in the manufacture of conduits and turbine blades.
Invar
Invar alloy, also known as low-expansion alloy, is a kind of iron (Fe) and nickel (Ni) combination of magnetic metal alloy, the main composition is 36% nickel, 64% iron, face-centred cubic structure.Invar alloy’s outstanding advantage is the coefficient of thermal expansion is very low, in addition to low thermal conductivity, high toughness, high section shrinkage, ductility is good, strength and hardness is low, good plasticity, etc., is an important structural material.
Iron and nickel both have positive thermal expansion characteristics, but when they are combined in a certain ratio, they form a material that can tenaciously exhibit almost ‘zero thermal expansion’ over a wide range of temperatures and pressures, an anomalous phenomenon known as the Inva effect. This property makes the alloy ideal for use in applications where extreme precision is required, such as the manufacture of parts for clocks, telescopes and other precision instruments.
MU-METAL
MU-METAL is an iron-nickel alloy, has a wide range of nickel content, between 35 and 90 percent. The most important characteristic of PoMo alloys is their high weak field permeability. Their saturated magnetic induction is generally between 0.6 and 1.0 T.
MU-METAL alloys often refer to iron-nickel alloys with a nickel content in the range of 30 to 90%. It is a very widely used soft magnetic alloy. Through the appropriate process, the magnetic properties can be effectively controlled, such as the initial permeability of more than 105, the maximum permeability of more than 106, the coercivity as low as 2 ‰ Oster, the rectangular coefficient close to 1 or close to 0. The pomol alloy with a face-centered cubic crystalline structure has a very good plasticity, and it can be processed into ultra-thin strips as thin as 1 μm and a variety of use forms. Commonly used alloys are 1J50, 1J79, 1J85 and so on.
Advantages of nickel alloy
- Good corrosion resistance, Nickel alloy has excellent corrosion resistance and can be used in some strong acid, alkali, seawater and other harsh environments. For petrochemical, chemical, aviation, nuclear industry and other fields, nickel alloy is an irreplaceable important material.
- High-temperature strength and heat resistance, Nickel alloy has good high-temperature strength and heat resistance and can maintain stable mechanical properties, chemical properties and physical properties at high temperatures. Therefore, nickel alloy is widely used in aviation, aerospace, nuclear industry and other high-temperature environment parts and structural materials.
- Easy processing and plasticity, Nickel alloy is easy to process into various shapes, has good plasticity and formability, and is suitable for hot processing, cold processing and welding and other processing techniques. Various complex structural parts and equipment can be made according to different process demands.
Disadvantages of nickel alloy
- Expensive, The cost of nickel alloy is relatively high, mainly because of the high cost of its raw materials, processing difficulty and complexity of the production process and other reasons. The price of nickel alloy is several times or even dozens of times that of ordinary steel, so it is difficult to be widely used on some occasions due to cost and other reasons.
- High hardness, difficult to process, Although nickel alloy is easy to process into various shapes, it is difficult to process due to its relatively high hardness, and it is necessary to choose the appropriate processing technology, or it may lead to problems such as rupture of the material.
- Poor solderability, The weldability of nickel alloys is relatively poor, making them susceptible to problems such as thermal cracking and deformation. It is necessary to choose a suitable welding process and welding materials for nickel alloy to solve these problems effectively.
Nickel Alloy Applications
Aerospace field
Nickel alloy is widely used in the aerospace field. Since nickel alloy has the characteristics of high-temperature strength, good oxidation resistance and strong corrosion resistance, it is widely used in the manufacture of aero-engine, rocket engines, aircraft structures and other components. For example, nickel-based high-temperature alloy is an important aero-engine material with excellent high-temperature performance and oxidation resistance, which can withstand extreme conditions such as high temperature, high pressure and high speed.
Petrochemical field
Nickel alloys also play an important role in the petrochemical field. Since petrochemical production involves a lot of high temperature, high pressure, corrosion and other harsh environments, materials with excellent corrosion resistance and high-temperature performance are required. Nickel alloys are widely used in the manufacture of petrochemical equipment, such as reactors, heat exchangers, pipelines and so on, because of their good corrosion resistance, high-temperature strength and stability.
Nuclear industry
Nickel alloys also have important applications in the nuclear industry. Due to the extremely harsh working environment in nuclear reactors, materials with extremely high corrosion resistance, high-temperature strength and stability are required. Nickel alloys are widely used in the manufacture of nuclear reactors, such as reactor pressure vessels, heat exchangers, pipelines, etc., because of their excellent physical and chemical properties.
Shipbuilding industry
Nickel alloys are also widely used in the marine industry. As ships operate in the marine environment for a long time, they need to withstand harsh conditions such as corrosion of seawater and erosion of marine organisms, so they need to use materials with excellent corrosion resistance and stability. Nickel alloys are widely used in the manufacture of ships, such as hull structures, propellers, thrusters and so on, because of their good corrosion resistance and mechanical properties.
Medical field
Nickel alloys also have important applications in the medical field. Due to their good biocompatibility and corrosion resistance, nickel alloys are widely used in the manufacture of medical devices and implants, such as dental implants, artificial joints, and pacemakers. In addition, nickel alloys are used in the manufacture of structural components for medical devices, such as ultrasonic probes and MRI machines.
Electronics industry
Nickel alloys also play an important role in the electronics industry. Due to their good electrical conductivity, thermal stability and corrosion resistance, nickel alloys are widely used in the manufacture of electronic components, such as resistors, capacitors and inductors. In addition, nickel alloys are used in the manufacture of structural components for electronic devices, such as brackets for semiconductor devices and packages for integrated circuits.
Nickel-Based Alloys Adding Elements And Functions
To further improve the physical and chemical properties of nickel to meet the requirements of scientific technology and industrial development, it is necessary to add an appropriate amount of alloying elements to nickel, they are Non-ferrous metal materials.
There are two types of alloying elements added: one is solid solution strengthening elements that can form a solid solution with nickel, such as copper, cobalt, iron, chromium, molybdenum, tungsten, manganese, etc.; the other is forming an intermediate compound strengthening phase with nickel Elements such as aluminum, silicon, beryllium, titanium, zirconium, hafnium, vanadium, niobium and tantalum. In addition, for specific purposes and applications, some trace elements are sometimes added, such as rare earth elements, boron, magnesium, calcium, strontium, and barium. When solid solution strengthening elements are added to nickel, its strength, hardness, shock resistance, corrosion resistance, oxidation resistance, high temperature strength and certain physical properties, such as magnetism, thermoelectric potential, resistivity, etc., are significantly improved, while the expansion coefficient, The thermoelectric potential and the temperature coefficient of resistance of copper are greatly reduced. When alloying elements that can form a strengthening phase are added to nickel, the properties of the material, especially the high-temperature mechanical properties, corrosion resistance and certain physical properties, will be further improved. The addition of trace elements to the alloy is either to eliminate the harmful effects of harmful impurities on the performance of the alloy, or to obtain some special physical properties of the alloy, or to strengthen the alloy grain boundary, so as to ensure that the alloy products have a better use effect and more Long service life.
Classification By Use
Superalloy
The main alloying elements are chromium, tungsten, molybdenum, cobalt, aluminum, titanium, boron, zirconium and so on. Among them, chromium plays the role of anti-oxidation and anti-corrosion, and other elements play a strengthening role. It has high strength and resistance to oxidation and gas corrosion under high temperature of 650~1000℃. It is the most widely used and the highest-temperature strength alloy among high-temperature alloys. Used to manufacture high-temperature parts for aero-engine blades and rocket engines, nuclear reactors, and energy conversion equipment.
Corrosion-Resistant Alloy
The main alloying elements are copper, chromium, and molybdenum. It has good comprehensive performance and can resist various acid corrosion and stress corrosion. The earliest application was nickel-copper alloy, also known as Monel alloy; in addition to nickel-chromium alloy, nickel-molybdenum alloy, nickel-chromium-molybdenum alloy, etc. Used to manufacture various corrosion-resistant parts
Wear-Resistant Alloy
The main alloying elements are chromium, molybdenum and tungsten, and also contain small amounts of niobium, tantalum and indium. In addition to its wear resistance, its oxidation resistance, corrosion resistance, and welding performance are also good. It can be used to manufacture wear-resistant parts, and it can also be used as a coating material.
Precision Alloy
Including nickel-based soft magnetic alloys, nickel-based precision resistance alloys and nickel-based electrothermal alloys. The most commonly used soft magnetic alloy is Permalloy with about 80% nickel. It has high maximum permeability and initial permeability, and low coercivity. It is an important core material in the electronics industry. The main alloying elements of nickel-based precision resistance alloys are chromium, aluminum, and copper. This alloy has higher resistivity, lower temperature coefficient of resistivity, and good corrosion resistance. It is used to make resistors. Nickel-based electric heating alloy is a nickel alloy containing 20% of chromium, has good resistance to oxidation and corrosion, and can be used for a long time at a temperature of 1000~1100℃.
Shape Memory Alloys
Nickel alloy containing 50% (at)% of titanium. The recovery temperature is 70℃, and the shape memory effect is good. A small amount of nickel-titanium composition can change the recovery temperature within the range of 30~100℃. They are mostly used to manufacture self-expanding structural parts used in spacecraft, self-excited fasteners for the aerospace industry, artificial heart motors used in biomedicine, etc.