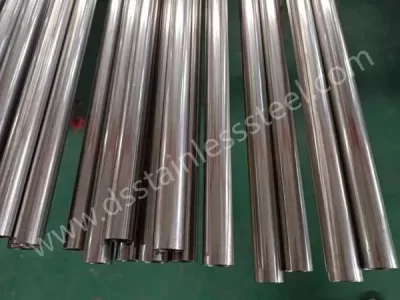
Nickel 200 tube is supplied following ASTM/ASME specifications by cold working and hot working methods, the standards include ASTM B161, B163, B725, B730, B751, B775 and B829, B161 and B163 UNS N02200 seamless tubes, B725 and B730 for welded pipes, UNS N02200 equivalent is 2.4066 steel no, UNS N02200 is equivalent of nickel 200.
Nickel 200 alloy is an alloy with excellent chemical and material properties. It has good corrosion resistance, heat resistance, oxidation resistance, mechanical properties, machinability and wear resistance, and is therefore used in a wide range of industrial applications. Pure nickel alloy 200 is widely used to manufacture chemical equipment, reactors, pipelines, etc. In the field of electronics, due to its good electrical and thermal conductivity, pure nickel alloy 200 is widely used in the manufacture of electronic equipment, wires and cables. In the energy field, due to its high heat transfer performance and high strength, pure nickel alloy 200 is widely used in the manufacture of nuclear energy equipment, solar panels and so on.
Nickel 200 Specifications
Price | USD 13.2 / kg |
---|---|
Standard | ASTM B161, B163, B725, B730, B751, B775, B829 |
Tube Type | Seamless Tube & pipe, welded tube & pipe |
Alloy | UNS N02200 200 nickel |
Finish | Annealed Stress-Relieved |
Tube Form | Straight Tubes U-Bend Tubes |
Outside Diameter | 6 – 610 Mm 1/8″ – 30″ |
Thickness | 0.8 – 30 Mm SCH 5, SCH10, SCH 40, SCH 80, SCH 80S, SCH 160, SCH XXS |
Nickel 200 Composition
The chemical composition of pure nickel alloy UNS N02200 is mainly nickel and small amounts of iron, chromium, manganese and other elements. Among them, the content of nickel is up to 99% or more, which is the main element to ensure the corrosion resistance of the alloy. Adding iron, chromium, manganese and other elements can improve the alloy’s processing performance and mechanical properties.
Alloy | Nickel, min | Copper, max | Iron, max | Manga-Nese, Max | Carbon, max | Silicon, max | SuLfur, Max |
---|---|---|---|---|---|---|---|
Nickel 200 | 99.0 | 0.25 | 0.40 | 0.35 | 0.15 | 0.35 | 0.01 |
Nickel 200 Mechanical Properties
Material And Condition | Tensile Strength Min. Ksi(MPa) | Yield Strength(0.2% Offset)Min,Psi(MPa) | Elongation In 2in. Or 50mm(Or 4D)Min. % | Rockwell Hardness(Or Equivalent) For Annealed Ends |
---|---|---|---|---|
Annealed | 55(379) | 15(103) | 40 | … |
Stress-Relieved | 65(448) | 40(276) | 15 | B65 max |
Nickel 200 Alloy Pipes & Tubes Quality
ASTM B161 B163, B725, B730, B751, B775, B829 Nickel 200 Seamless Pipes and Tubes are manufactured in the form of cold-worked seamless process, Annealed and Stress-Relieved surface finishes are available, tension test shall be performed; wherein, the tensile properties for the material specified as small-diameter and light-wall tube shall be in conformity with the tensile strength, yield strength, and elongation requirements. Each pipe or tube shall also be subjected to a nondestructive electric test or hydrostatic test following a referenced ASTM document to determine the allowable fiber stress for the annealed and stress-relieved materials, Rockwell hardness, grain size and hardness conversion shall be performed under the referenced ASTM document.
Small-Diameter and Light-Wall Tube
Outside Diameter | Outside Diameter | Inside Diameter | Wall Thickness, % | |||
---|---|---|---|---|---|---|
Plus | Minus | Plus | Minus | Plus | Minus | |
Under 3⁄32 (2.4) | 0.002 (0.05) | 0 | 0 | 0.002 (0.05) | 10 | 10 |
3⁄32 to 3⁄16 (2.4 to 4.8), excl | 0.003 (0.08) | 0 | 0 | 0.003 (0.08) | 10 | 10 |
3⁄16 to 1⁄2 (4.8 to 12.7), excl | 0.004 (0.10) | 0 | 0 | 0.004 (0.10) | 10 | 10 |
1⁄2 to 1 1⁄4 (12.7 to 31.8), incl | 0.005 (0.13) | 0 | 0 | 0.005 (0.13) | 10 | 10 |
Nickel 200 Physical Properties
Properties | ||
---|---|---|
Density | 8.89 g/cm³ | 0.321 lb/in³ |
Melting point | 1446°C | 2635°F |
Coefficient of expansion | 13.3 μm/m °C (20 – 100°C) | 7.4 x 10-6 in/in °F (70 – 212°F) |
Rigid modulus | 81 kN/mm² | 11748 ksi |
Modulus of elasticity | 204 kN/mm² | 29588 ksi |
Forms & Other Designations
Forms | Standard |
---|---|
Rod and bar | ASTM B160, DIN 17752, ISO9723 |
Pipe and Tube | ASTM B161, B163, B725, B730, B751, B775, B829, DIN 17751, ISO 6207 |
Plate, Sheet & Strip | ASTM B162, DIN 17750, ISO 6208 |
Fittings | ASTM B366 |
Forgings | ASTM B564, ISO 9725, DIN17754 |
Wire | DIN 17753, ISO 9724 |
Nickel UNS N02200 Rod and Bar
ASTM B160 Nickel UNS N02200 Rod and Bar: B160 covers nickel (UNS N02200), low carbon nickel (UNS N02201), and solution-strengthened nickel (UNS N02211) in the form of hot-worked, cold-worked, or annealed rods and bars of round, square, hexagonal, or rectangular solid section.
DIN 17752 Rods and bars of nickel and wrought nickel alloys – Properties.
Nickel UNS N02200 Pipe and Tube
ASTM B161 Nickel UNS N02200 Seamless Pipe and Tube, B161 specification covers the standard requirements for nickel (UNS N02200) and low-carbon nickel (UNS N02201) in the form of cold-worked seamless pipe and tube.
ASTM B163 Nickel UNS N02200 Seamless Tube, B163 specification covers seamless tubes of nickel and nickel alloy for use in condenser and heat-exchanger service. Dimensions cover outside diameter and average wall, or outside diameter and minimum wall tube.
ASTM B725 Nickel UNS N02200 Welded Pipe: B725 specification covers UNS N02200 nickel alloy and UNS N02201 and N04400 low carbon nickel alloy welded pipes used for general corrosive service and for mechanical applications. Each pipe should either be welded and annealed or welded and stress-relieved and made from the flat-rolled alloys by an automatic welding process without any filler metal additions. The pipes should also be cold-worked after welding to ensure the development of optimum corrosion resistance in the weld area and base metal during the final heat treatment.
ASTM B730 Nickel UNS N02200 Tube: Specification for Welded Nickel (UNS N02200/UNS N02201) and Nickel Copper Alloy (UNS N04400) Tube, B730 covers nickel (UNS N02200), low-carbon nickel (UNS N02201), and nickel-copper alloy (UNS N04400) in the form of welded and annealed or welded and stress-relieved tube intended for general corrosive service and for mechanical applications.
ASTM B751 Nickel UNS N02200 Tube: Standard Specification for General Requirements for Nickel and Nickel Alloy Welded Tube.
ASTM B775 Nickel UNS N02200 Pipe: Standard Specification for General Requirements for Nickel and Nickel Alloy Welded Pipe
ASTM B829 Nickel UNS N02200 Pipe and Tube: Standard Specification for General Requirements for Nickel and Nickel Alloys Seamless Pipe and Tube.
Nickel UNS N02200 Plate, Sheet and Strip
ASTM B162 UNS N02200 Plate, Sheet and Strip: specification covers rolled nickel (UNS N02200) and low-carbon nickel (UNS N02201) plate, sheet, and strip. The material shall conform to the chemical requirements for nickel, copper, iron, manganese, carbon, silicon, and sulfur. The material shall conform to the mechanical property requirements for tensile strength, yield strength, elongation, and Rockwell hardness. For deep drawing and spinning quality sheet and strip, the material shall conform to specified values for grain size and hardness properties. The material shall be uniform in quality and temper, smooth, commercially straight or flat, and free of injurious imperfections.
Nickel UNS N02200 Fitting
ASTM B366 Nickel UNS N02200 Fitting: Standard Specification for Factory-Made Wrought Nickel and Nickel Alloy Fittings, B365 covers wrought welding fittings, including threaded fittings, for pressure piping, factory-made from nickel and nickel alloys. The term welding applies to butt-welding or socket-welding parts such as elbows, bends, caps, tees, reducers, lap-joint, and stub ends. This specification does not apply to cast welding fittings. Grades of nickel and nickel alloys included in this specification are designated with a prefix, WP or CR, based on dimensional and rating standards. WP grades have class designations (Class S, Class W, Class WX, and Class WU) to indicate whether seamless or welded construction is utilized and to indicate the nondestructive test method and extent of nondestructive examination (such as radiography and/or ultrasonic test). The material for wrought welding fittings may consist of forgings, rods, bars, plates, sheets, and seamless or welded pipe that conform to all the specified requirements. Forging or shaping operations may be performed by hammering, pressing, piercing, extruding, upsetting, rolling, bending, or fusion welding, or by a combination of two or more of these operations.
Nickel UNS N02200 Forging
ASTM B564 UNS N02200 Forging: Standard Specification for Nickel Alloy Forgings
Nickel UNS N02200 Wire
Nickel 200 Alloy Features
- High purity: Nickel 200 is a highly pure metallic material containing very few impurities, giving it excellent chemical stability and conductivity properties.
- Corrosion Resistance: Nickel 200 alloy has excellent corrosion resistance and exhibits good corrosion resistance in both acidic and alkaline media. It has good corrosion resistance to most acids, alkalis, salts and organic substances. Although most useful in reducing environments, it can also be used under oxidizing conditions that cause the development of a passive oxide film.
- Thermal stability: It maintains good thermal stability at high temperatures and can maintain good mechanical properties and oxidation resistance at high temperatures.
- Electromagnetic properties: It has good electrical conductivity and magnetism, and can be used to manufacture electronic components and magnetic materials.
- Mechanical Properties: It has good ductility and plasticity, and can withstand a certain degree of deformation and load. which can meet the manufacturing requirements of various complex shapes and high-precision parts.
- Welding properties: At the same time, Nickel 200 alloy has excellent welding properties, which can meet the requirements of various welding processes, such as fusion welding and pressure welding. This makes it widely used in power electronics and medical devices, such as the manufacture of battery electrodes, electronic components and medical device parts.
- Wear resistance: Although the hardness of Ni200 nickel alloy is relatively low, it still has good wear resistance under certain specific conditions.
- Oxidation resistant: Nickel 200 nickel alloy has good oxidation resistance in air, which can effectively prevent surface oxidation and discoloration. This makes Ni200 nickel alloy also valuable for applications in areas such as decoration and handicraft manufacturing.
- Non-magnetic: Nickel 200 nickel alloy is a non-magnetic material and is suitable for use in applications that are sensitive to magnetic fields.
- High-temperature stability: Nickel 200 nickel alloy can maintain stable performance in high-temperature environments, and is not prone to structural changes or excessive thermal expansion.
- Heating and Pickling: Nickel 200 may be annealed over a wide range of temperatures above its recrystallization temperature. For heavily coldworked material, the temperature may be as low as 1100° to 1200°F (595° to 650°C), but from a practical viewpoint, the range is usually about 1300 to 1700°F (705° to 925°C).
- Cold Forming: Nickel 200 can be worked by all conventional cold-forming methods. Generally, the alloy will behave similarly to mild steel, except that, because of the higher elastic limit of Nickel 200, greater power will be required to perform the operations. Thus, manual operations such as spinning and hand hammering are limited to simple shapes. Severe work can be done manually only with the assistance of frequent anneals to restore softness.
Nickel 200 Alloy Applications
- Chemical industry: Ni 200 alloy is often used in the chemical industry for the preparation of acid and alkali containers, chemical valves, volumetric apparatus, and absorption towers, as well as in a variety of acids, alkalis and solutions in the heat transfer tube, storage tanks and other equipment.
- Battery industry: Ni 200 alloy is often used in the battery industry to make battery poles, with good corrosion resistance and conductivity, suitable for acid or alkaline batteries.
- Food processing: Ni200 alloy is widely used in the food processing industry to make food heating equipment, steam chambers, yoghurt pots, etc., with excellent corrosion resistance and hygienic properties.
- Medical devices: Ni200 alloy is widely used in medical devices, such as artificial heart valves, artificial joints, dental inserts, etc. due to its harmless and corrosion-resistant properties.
- Aerospace: Ni200 alloy is often used to make fuel cells, turbine blades, engine parts, etc. in the aerospace field due to its high strength and corrosion resistance.
Nickel 200 alloy is a versatile, high-temperature nickel-based alloy with high purity, excellent corrosion resistance, mechanical properties and high-temperature performance. The alloy has a wide range of applications in the chemical, battery, food processing, medical device and aerospace industries. It is available in the form of plates, tubes, rods, wires, etc., and can be custom-processed to meet specific needs.
Difference Between Nickel 200 and 201
Nickel 200 and Nickel 201 have significant differences in chemical composition, physical properties, corrosion resistance and application areas.
Chemical composition
- Nickel Alloy 200 (Ni-200) is a pure nickel alloy containing a minimum of 99.2% nickel in its chemical composition. It is a very pure nickel alloy and is often chosen for use in environments where It is a very pure nickel alloy and is often selected for use in environments with very high corrosion requirements.
- Nickel Alloy 201 is also a nickel alloy with a lower carbon content. It contains a minimum of 99.0% nickel, while the carbon content is limited to less than 0.02%. Compared to Nickel Alloy 200, Nickel Alloy 201 has a lower carbon content.
Mechanical properties
At room temperature, the mechanical properties of Ni200 and Ni201 are similar, both have good plasticity and toughness. However, at high temperatures, due to differences in composition and microstructure, the mechanical properties of the two will appear to have larger changes.
Physical Properties
- Nickel 200 is a non-magnetic alloy because it has a high purity of nickel.
- Nickel 201, although also a non-magnetic alloy, may be slightly magnetic at high temperatures due to its slightly higher carbon content than Nickel Alloy 200.
- Density: The density of Ni200 is close to that of pure nickel, about 8.9g/cm³, while the density of Ni201 is slightly higher than that of Ni200, about 8.95g/cm³.
- Melting point: due to the different composition, Ni200 and Ni201 melting point there are some differences. Ni200 melting point is higher, about 1455 ℃, while Ni201 melting point is slightly lower, about 1350 ℃.
- Thermal conductivity: Ni201’s thermal conductivity is better than Ni200 because it contains a certain amount of chromium, chromium can improve the thermal conductivity of the material.
Corrosion Resistance
- Ni200 and Ni201 have excellent caustic resistance and good electrical and magnetostrictive properties.
- Both have good corrosion resistance and are suitable for a wide range of reducing chemicals.
- Ni201 contains a certain amount of chromium, so its corrosion resistance is better than that of Ni200.In an oxidizing environment, Ni201 can form a dense oxide film on its surface, effectively resisting corrosion. In the reducing environment, the corrosion resistance of Ni201 is also improved due to the addition of chromium. However, it should be noted that in extreme environments such as high sulfur and high temperature, Ni201’s corrosion resistance may be affected.
Areas of Application
- Nickel 200 is typically used in environments with very high corrosion requirements.
- Nickel 201 is used in higher temperature applications such as the handling and manufacture of sodium hydroxide above 300°C, soap manufacture, viscose rayon manufacture, benzene, methane and ethane production, reactors and vessels, etc.
In summary, the choice to use nickel 200 or nickel 201 depends on the specific environment and conditions of use. Understanding the differences between these materials will help to utilize their advantages and provide more reliable support and security for industrial production.