Martensitic Stainless Steel has a body-centered tetragonal (BCT) crystal structure (martensitic) in the hardened condition. They are ferromagnetic, hardenable by heat treatments, and generally resistant to corrosion only in relatively mild environments, chromium content is in the range of 10.5 to 18%, and the carbon content lies between 0.1 and 1.2%, through the heat treatment process, martensitic stainless steels can form a special crystal structure known as martensite, this structure gives the steel its high hardness and strength properties. Standard martensitic stainless steel grades include 403, 410, 414, 416(Se), 420, 431, 440A, 440B and 440C.
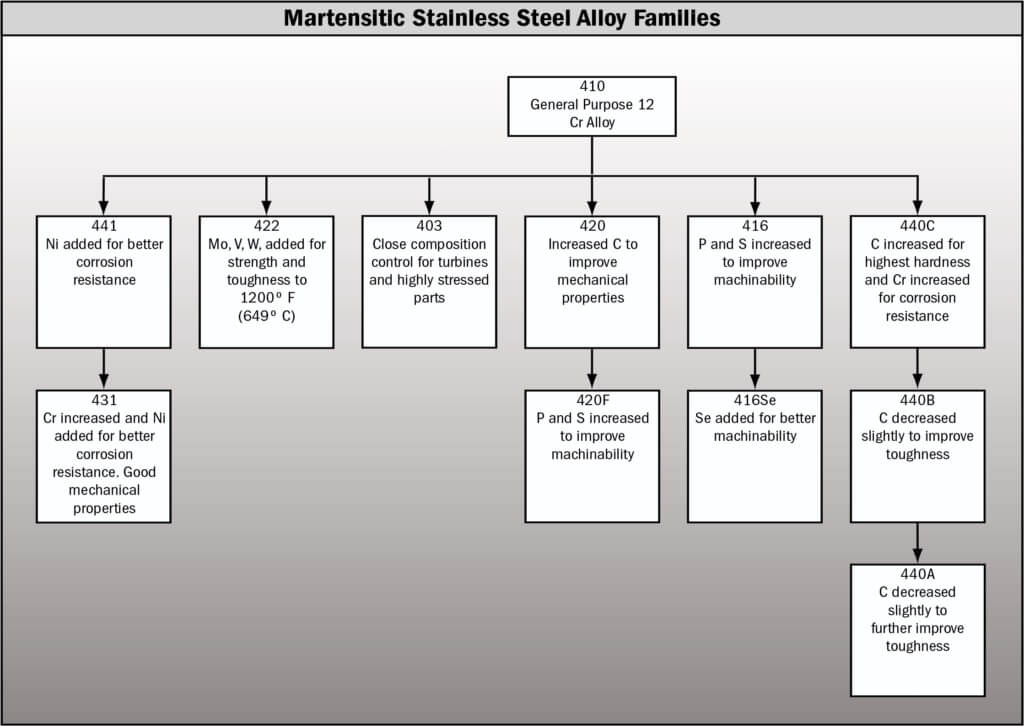
Martensitic stainless steel needs to be quenched during the manufacturing process to obtain the desired microstructure and mechanical properties. Its high hardness, good wear resistance, and fatigue resistance, are suitable for manufacturing parts and tools that need to withstand high stress or abrasion resistance. At the same time, martensitic SS has good corrosion resistance and can work in a variety of corrosive media.
Martensitic Stainless Steel Grades and Composition
AISI Grade | C | Mn | Si | Cr | Ni | Mo | P | S | Comments/Applications |
---|---|---|---|---|---|---|---|---|---|
410 | 0.15 | 1 | 0.5 | 11.5–13.0 | – | – | 0.04 | 0.03 | The basic composition. Used for cutlery, steam, and gas turbine blades and buckets, bushings |
416 | 0.15 | 1.25 | 1 | 12.0–14.0 | – | 0.6 | 0.04 | 0.15 | Addition of sulfur for machinability, used for screws, gears etc. 416 Se replaces sulfur by selenium |
420 | 0.15–0.40 | 1 | 1 | 12.0–14.0 | – | – | 0.04 | 0.03 | Dental and surgical instruments, cutlery |
431 | 0.2 | 1 | 1 | 15.0–17.0 | – | 1.25–2.00 | 0.04 | 0.03 | Enhanced corrosion resistance, high strength |
440A | 0.60–0.75 | 1 | 1 | 16.0–18.0 | – | 0.75 | 0.04 | 0.03 | Ball bearings and races, gage blocks, molds and dies, cutlery |
440B | 0.75–0.95 | 1 | 1 | 16.0–18.0 | – | 0.75 | 0.04 | 0.03 | As 440A, higher hardness |
440C | 0.95–1.20 | 1 | 1 | 16.0–18.0 | – | 0.75 | 0.04 | 0.03 | As 440B, higher hardness |
Features and Advantages
- High hardness and strength: through heat treatment, martensitic SS can achieve very high hardness. In general, its strength and hardness are higher than ferritic and austenitic stainless steel. Therefore, it is very suitable for application scenarios that require high-strength materials.
- Good corrosion resistance: although not as good as austenitic stainless steel, martensitic SSl still performs well in most environments. Its corrosion resistance can be greatly improved by proper alloy design and heat treatment.
- Adjustable mechanical properties: the mechanical properties of martensitic stainless steel can be adjusted through the heat treatment process. This adjustability allows engineers to adjust the hardness, toughness and strength of the steel according to specific needs, so as to obtain the optimal material properties.
- Versatility in manufacturing processes: martensitic stainless steel is easy to machine, weld and form, making it easy to use in a variety of manufacturing processes. This greatly improves its applicability in industry.
- Magnetic: Martensitic stainless steel has a certain degree of magnetism, which is determined by its organizational structure. The martensite in martensitic steel has a higher magnetic permeability compared to other phase organizations, which means that it has a higher ability to magnetize under a magnetic field. Although martensitic stainless contains iron, chromium, and other elements, its magnetic properties are not as strong as iron, steel, and other materials.
Limitation
- Poor toughness. this toughness characteristic means that martensitic stainless steels are more prone to rupture or fracture when subjected to impact or high stress. This low toughness limits its use in applications that require high-impact strength or high-stress tolerance.
- Corrosion under certain conditions. this is mainly due to its higher carbon content, which results in poor corrosion resistance in harsh environments such as salt water exposure or acidic solutions. This susceptibility to corrosion is a significant disadvantage compared to other types of stainless steel and may limit its use in practical applications. Therefore, when selecting martensitic stainless steels for fabrication or construction, special attention needs to be paid to their potential corrosion problems and appropriate preventive measures need to be taken.
- Poor weldability: This is mainly due to their high carbon content which leads to cracking during welding. The high carbon content makes it easier for martensitic stainless steel to form a hard and brittle martensitic organization during welding, which is more sensitive to cracking. Therefore, when welding martensitic stainless steel, special attention needs to be paid to the selection of suitable welding materials and processes to reduce the risk of cracking.
- Martensitic stainless steel is susceptible to cooling cracks during rapid cooling. This is mainly because the excessive cooling rate leads to an increase in thermal and organizational stresses, which exceed the material’s ability to withstand, thus triggering cracks. Such cracks not only affect the mechanical properties of the material but also may reduce its service life. Therefore, when treating martensitic stainless steel, special attention needs to be paid to controlling the cooling rate to reduce the risk of cooling cracks.
Applications
- Knives and cutting tools: Due to its high hardness and good wear resistance, martensitic stainless steel is widely used in the manufacture of knives, surgical knives and industrial cutting tools, etc.
- Aerospace and defense industry: In the aerospace and defence industry, high strength and corrosion resistance of materials are the basic requirements. Martensitic stainless steel is widely used in demanding areas such as aircraft components and missile casings.
- Construction and infrastructure: In certain construction and infrastructure construction, martensitic stainless steel is used to manufacture high-strength structural components, bridges and tunnels, etc. due to its high durability and good mechanical properties.
- Oil and gas industry: The oil and gas extraction environment is extremely harsh, and the material requirements for equipment are very high. Martensitic stainless steel is widely used in drilling equipment, pumps and valves because of its corrosion resistance and high strength.
Welding Martensitic Stainless Steel
1. Preheat Before Welding
Welding martensitic stainless steel should be preheated before welding, especially in the use of welding materials with the same composition as the base material, to prevent cold cracking. The preheating temperature is generally selected at 200 ~ 329 ℃, preferably not higher than the martensite transition temperature. Carbon content is the most important factor in determining the preheating temperature, for high carbon content, the preheating temperature should be higher. Other factors affecting the choice of preheating temperature are the material’s thickness, filler metal type, welding method, constraints, and so on. Carbon content of less than 0.1% can not be preheated, there are also recommended preheating temperatures, such as preheating 400 ~ 450 ℃, but pay attention to the adverse effects of high-temperature preheating. Carbon content greater than 0.2%, welding is more difficult, in addition to preheating, the need to maintain the interlayer temperature.
2. Temperature Before Tempering After Welding
Workpiece welding should not be directly from the welding temperature temperature tempering treatment. Because in the welding process, austenite may not be fully transformed, such as immediately after welding temperature tempering, there will be carbide precipitation along the austenite grain boundaries and austenite to pearlite transformation, resulting in coarse grain size of the organization, seriously reducing toughness. Therefore, before tempering, the weldment cooling, so that the weld and heat-affected zone of austenite basic decomposition is complete. For the stiffness of small components, can be cooled to room temperature and then tempered. For the large thickness of the structure, especially when the carbon content is high, need to use a more complex process: after welding cold to 100 ~ 150 ℃, insulation 0.5 ~ 1.0h, and then heated to the tempering temperature.
3. Heat Treatment
The purpose of heat treatment is to reduce the hardness of the weld and heat-affected zone and improve its plasticity and toughness while reducing the welding residual stress. Post-weld heat treatment includes tempering and complete annealing. Only to get a low hardness, such as the need for post-weld machining, only the use of complete annealing, the annealing temperature of 830 ~ 880 ℃, insulation 2h furnace cooling to 595 ℃, and then air-cooled. High chromium martensitic stainless steel is generally welded in the quenched + tempered tempered state, after welding by high-temperature tempering treatment, so that the welded joints have good mechanical properties. If welded in the annealed condition, there will still be uneven martensitic organization after welding, the whole weldment also needs to be tempered to make the joints have uniform properties.
The choice of tempering temperature should be adapted to the requirements of mechanical properties and corrosion resistance of butt joints in engineering projects. The tempering temperature is generally selected from 650 to 750°C, held at least 1h, and then air cooled. The tempering temperature should not be too high to prevent austenite transformation again. Higher tempering temperature is often used for high-temperature use of welded structures. Tempering at high temperatures precipitates more carbides, on the corrosion resistance is unfavourable. For the structure mainly used for corrosion resistance, should be low-temperature stress relief annealing.
Martensitic stainless steel common welding methods are manual arc welding, tungsten argon arc welding and CO₂ welding. Hand-to-arc welding is the most commonly used method of martensitic low stainless steel welding, using the same composition as the base metal electrode welding, electrode flux type the low nitrogen type, before welding must be as high as 350 ~ 400 ℃ high-temperature baking, to eliminate moisture, reduce the diffusion of hydrogen content and reduce the susceptibility to cold cracking. When heat treatment cannot be carried out after welding, austenitic electrode welding is used, and the welding specification refers to the requirements of an austenitic electrode.
Tungsten argon arc welding is generally used for thin plate welding, using DC positive polarity. Tungsten argon arc welding quality is better, with less tendency to cold cracking, generally thin plate without preheating.
FAQ
Martensitic stainless steel has excellent mechanical properties and corrosion resistance, applicable to a variety of industrial and civil fields. Martensitic stainless steel is a class of hardenable stainless steel that, through heat treatment can adjust its mechanical properties. In addition, martensitic stainless steel also has high mechanical properties and low sensitivity to heat treatment overheating.
410 stainless steel is martensitic stainless steel. 410 stainless steel is a stainless steel grade produced following the American ASTM standard. 410 stainless steel has good corrosion resistance and machinability and is usually used for making knives, valves and so on. In addition, 410 stainless steel also has high hardness and good thermal strength, cold deformation properties and shock absorption.
420 stainless steel is indeed a martensitic stainless steel. 420 stainless steel is a high carbon martensitic stainless steel with high carbon content and good wear and corrosion resistance. Its chemical composition includes 12.50 percent to 14.50 percent chromium, 0.15 percent to 0.40 percent carbon, and other.
440C is a martensitic stainless steel.440C stainless steel has a high carbon content (0.95 to 1.20 percent) and a high chromium content (16 to 18 percent), which gives it high hardness, high strength and good wear resistance.440C stainless steel is usually heat-treated (quenched and tempered) to obtain its high hardness and strength, and its hardness can reach HRC 58 or above.
Martensitic stainless steel knives have high hardness and strength which makes them suitable for use in knife manufacturing. Martensitic stainless steel is a class of stainless steel whose properties can be adjusted by heat treatment (quenching, tempering), with high strength and corrosion resistance, so it is used to make knives quality. Martensitic stainless steel cutting tools in the cutting process, high cutting temperature, chips are not easy to break, sharp cutting edge, suitable for cutting a variety of ingredients.
Martensitic stainless steel is a non-toxic material that contains no elements or compounds that are harmful to the human body. Nor are any harmful substances, including lead and mercury, used in the manufacturing process. Martensitic stainless steel is highly thermally stable and can maintain its structure and properties at high temperatures. This material will not release harmful substances from baking at high temperatures, nor will it deform or become brittle with high temperatures.