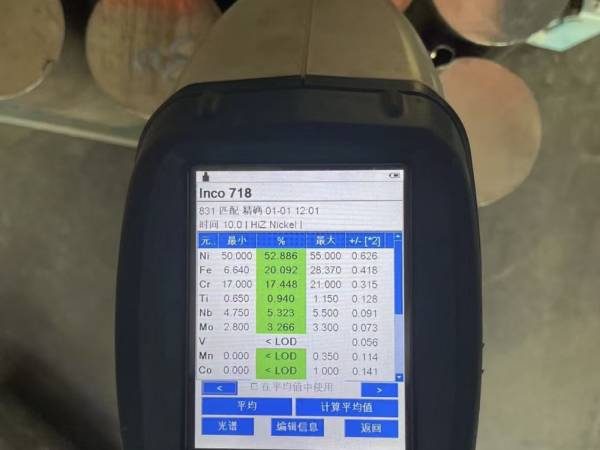
Inconel 718 (UNS N07718) is a nickel alloy produced in bar, wire, billet, strip, rod, sheet, plate, and forging, the Inconel 718 specifications include ASTM B 670, ASTM B 637, AMS 5596, AMS 5597, AMS 5589, AMS 5590, AMS 5662, AMS 5663, and AMS 5664. Inconel 718 material is a high nickel content alloy whose price is higher than other Inconel alloys.
Inconel 718 (UNS N07718) is a precipitation-hardening nickel-iron-based high-temperature superalloy containing niobium and molybdenum. Inconel 718 possesses excellent mechanical properties, high-temperature strength, and resistance to oxidation and corrosion. Inconel 718 is commonly used in various industries, including aerospace, oil and gas, automotive, and power generation.
Inconel 718 Composition
Inconel 718 is primarily composed of 50-55% nickel, with significant amounts of chromium, iron, niobium, molybdenum, and more minor additions of other elements, such as aluminum and titanium. These alloying elements contribute to unique properties. The chromium (Cr) content is in the range of 17-21%, which further enhances the oxidation resistance of the alloy and enables it to exhibit good corrosion resistance in corrosive atmospheres, especially those containing chlorides and acid gases. The addition of niobium (Nb) and molybdenum (Mo) is a distinctive feature of Alloy 718 in the ranges of 4.75-5.50 percent and 2.8-3.3 percent, respectively. Niobium and molybdenum are used as the main strengthening elements to increase the strength and creep resistance of the alloy through a precipitation-hardening process. Alloy 718 also contains trace amounts of titanium (Ti) and aluminum (Al) in proportions of 0.65-1.15% and 0.2-0.8%, respectively.
Element | Percentage |
---|---|
Carbon | 0.08 Max |
Manganese | 0.35 Max |
Phosphorus | 0.015 Max |
Sulfur | 0.015 Max |
Silicon | 0.35 Max |
Chromium | 17-21 |
Nickel | 50-55 |
Molybdenum | 2.80-3.30 |
Columbium | 4.75-5.50 |
Titanium | 0.65-1.15 |
Aluminum | 0.20-0.80 |
Cobalt | 1.00 Max |
Boron | 0.006 Max |
Copper | 0.30 Max |
Tantalum | 0.05 Max |
Iron | Balance |
Inconel 718 Mechanical Properties
Forms | Yield Strength Min (0.2% offset) | Ultimate Tensile Strength Min | Elongation (% in 2″) |
---|---|---|---|
Sheet and strip | 80,000 psi (550 MPa) | 140,000 psi (965 MPa) | 30 (min) |
Plate | 105,000 psi (725 MPa) | 150,000 psi (1,035 MPa) | 30 (min) |
Inconel 718 Physical Properties
Properties | Value |
---|---|
Density (g/cm3) | 8.2 |
Magnetic Permeability (20°C) | <1.002 |
Melting range [°C] | 1,260 – 1,335 |
Young’s Modulus (kN/mm2) | 200 |
Specific Electrical Resistance, 20°C (µΩ-m) | 1.25 |
Mean coefficient of thermal expansion, 20-100°C (m/m/degC) | 12.1 x 10-6 |
Specific Heat, 20°C (J/kg.K) | 435 |
Thermal Conductivity, 20°C (W/m.K) | 11.1 |
Curie Temperature (degC) | -112 (aged) |
Inconel 718 Equivalent
- Nickel 718
- Alloy 718
- ATI 718
- UNS N07718
- DIN 2.4668
Inconel 718 Specifications
- AMS 5596 Sheet, Strip and Plate
- AMS 5597 Sheet, Strip and Plate
- AMS 5589 Seamless Tube
- AMS 5590 Seamless Tube
- AMS 5662 Bars, Forgings and Rings
- AMS 5663 Bars, Forgings and Rings
- AMS 5664 Bars, Forgings and Rings
- AMS 5832 Welding Wire
- ASTM B637 Forgings
- ASTM B670 Plate, Sheet and Strip
Inconel 718 Properties
- High Strength: Excellent tensile, fatigue, creep and fracture strength at high temperatures.
- Corrosion resistance: excellent performance at high and low temperatures, suitable for various corrosive media.
- High-temperature performance: at 700 ℃ still maintains high strength, and has excellent oxidation resistance. Inconel 718 retains its strength and mechanical properties at elevated temperatures, making it suitable for applications that involve high temperatures and thermal stress, such as gas turbines, jet engines, and rocket motors.
- Fatigue resistance: Inconel 718 has good fatigue resistance, which means it can withstand repeated stress cycles without failure. This property makes it suitable for cyclic loading applications, such as turbine disks and rotor blades.
- Weldability: Inconel 718 can be welded using various techniques, including gas tungsten arc welding (GTAW), plasma arc welding (PAW), and electron beam welding (EBW). However, proper welding procedures and post-weld heat treatment are required to ensure optimal properties.
- MAGNETICITY: Inconel 718 has low magnetic properties, making it ideal for some magnetically sensitive applications such as magnetic field detectors in aerospace.
Heat treatment
The annealing temperature range for Inconel 718 is typically between 982°C and 1010°C, the temperature range allows the alloy to achieve optimum grain growth control and improve its tensile strength and fatigue resistance.
Inconel 718 undergoes a precipitation-hardening heat treatment to enhance its mechanical properties. This heat treatment involves solution annealing at a specific temperature followed by aging to develop the desired strength and hardness.
Machinability
Inconel 718 alloy has good machinability, which allows it to play an important role in various industrial applications.
The machinability of Inconel 718 is characterized by its excellent plasticity and welding properties. The alloy maintains good strength and corrosion resistance at high temperatures, thanks to its good machinability. Specifically, 718 maintains good tensile and yield strengths at temperatures as high as 660°C, a characteristic that makes it an excellent performer in high-temperature, critical-part applications. In addition, the machinability of Inconel 718 alloy allows the material to be easily machined and shaped in various ways, which not only enhances the productivity of the product but also ensures the high quality of the finished product. The alloy’s plasticity and weldability are particularly important during processing, as it allow forming by forging, rolling, machining, etc., and support for welding and heat treatments, further expanding its range of applications!
Inconel 718 Forms
- Forgings: used in the manufacture of various static and rotating parts in aero-engines.
- Bars: including forged, rolled and cold-drawn bars for a variety of machining applications.
- Sheets and strips: used to manufacture parts that require good forming properties and high strength.
- Wire: Used in the manufacture of fasteners, elastic elements, etc.
- Tubes: Used in the manufacture of piping systems subject to high temperatures and pressures.
- Rings: for engine components.
- Ring parts: used for sealing and supporting parts of turbine engines.
- Plates: Used in the manufacture of various structural components and pressure vessels.
Inconel 718 Applications
- Aerospace: engine components, gas turbines, seals, fasteners.
- Nuclear energy industry: fuel components, heat exchangers, pressure vessels.
- Petroleum and chemical industry: pumps, valves, reactors, heat exchangers.
- Marine engineering: for marine environments due to its excellent corrosion resistance.
- Medical devices: used in the manufacture of certain medical devices due to its biocompatibility and corrosion resistance.
Inconel 718 vs 625
Inconel 718 and Inconel 625 are both high-temperature resistant nickel-based alloy materials, but the heat-resistant temperature is different. the heat-resistant temperature of Inconel 718 is around 700℃, while the heat-resistant temperature of Inconel 625 is around 450℃. Regarding chemical composition, Inconel 718 contains more nickel, chromium, molybdenum and other elements, while Inconel 625 contains more chromium, molybdenum, niobium and other elements. Regarding physical properties, Inconel 718 has better corrosion resistance and high-temperature strength, while Inconel 625 has better fatigue resistance and corrosion resistance, and still maintains good plasticity and toughness at high temperatures.
UNS N07718 Composition
- Nickel (Ni): 50-55 per cent
- Chromium (Cr): 17-21 per cent
- Iron (Fe): 18-23 per cent
- Niobium (Nb): 4.75-5.5 per cent
- Molybdenum (Mo): 2.8-3.3 per cent
- Cobalt (Co): 1.0% max
- Aluminium (Al): 0.2-0.8%
- Titanium (Ti): 0.2-0.8 per cent
- Carbon (C): 0.08% max
- Manganese (Mn): 0.35% max
- Silicon (Si): 0.35% max
- Phosphorus (P): 0.015% max
- Sulphur (S): 0.015% max
- Copper (Cu): 0.5% max