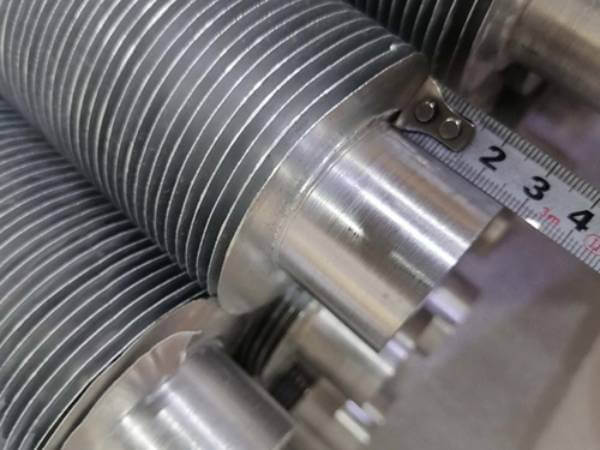
Finned tube is a kind of heat exchange component, the fin is designed to improve the efficiency on the surface of the core tube. The finned tube is an efficient performance enhancement method for conventional heat exchangers. The type of finned tube is chosen depending on the specific requirements of each process equipment unit. Commonly, tubes currently have circular cross-section fins. Convective heating surfaces with circular, square, or helical fins represent tube bundles or tube banks with staggered or in-line arrangements of tubes in cross-flow.
Finned tubes are used to achieve enhanced heat transfer by adding fins to an ordinary base tube. The base tube of the finned tube can be made of steel tube; stainless steel tube; copper tube and so on. The fins can also be made from steel strips, stainless steel strips, copper strips, aluminum strips, and so on, where the fins are added to the heat exchanger tubes to increase the heat dissipation area of the heat exchanger.
Finned Tube Specfications
Base tube material | Stainless steel: 304/304l, 316/316L/316Ti, 321 Carbon steel Titanium Copper Aluminum |
---|---|
Tube OD | 8 – 50.8 mm |
Tube wall thickness | 1 – 3 mm |
Tube length | Random |
Fin Height | 6 – 32mm |
Fin Segment Width | |
Fin Thickness | 0.3 – 1 mm |
Fin Pitch | 6 – 18 per inch |
Fin Materials | Aluminum Copper Carbon steel |
Fin serrate numbers | 6 – 32 |
Serrate fin depth | 8 – 40 mm |
Finned Tubes Processing
- Extruded fin tube
- Welding forming fin tube (high-frequency welding fin tube, submerged arc welding fin tube);
- Roll forming fin tube;
- Set forming fin tube;
- Casting finned tube;
- Tension wound finned tube;
- Inlaid finned tube.
Fin Shapes
- Square finned tube;
- Round finned tube;
- Spiral finned tube
- Longitudinal finned tube
- Corrugated Finned Tube;
- Helical Serrated Finned Tubes;
- Needle-shaped finned tube;
- Integral Plate Finned Tubes (Plate Fin);
- Inner finned tube.
Finned Tube Material
- Copper finned tubes;
- Aluminium finned tubes;
- Carbon steel finned tubes;
- Stainless steel finned tubes;
- Cast iron (cast steel) finned tubes;
Finned Tube Applications
- Finned tubes for air-conditioning;
- Finned tubes for air-cooling;
- Boiler: finned tubes for water-cooled wall, economizer and air preheater respectively;
- Finned tubes for industrial waste heat recovery;
- Other special-purpose finned tubes;
Finned Tube Drawing
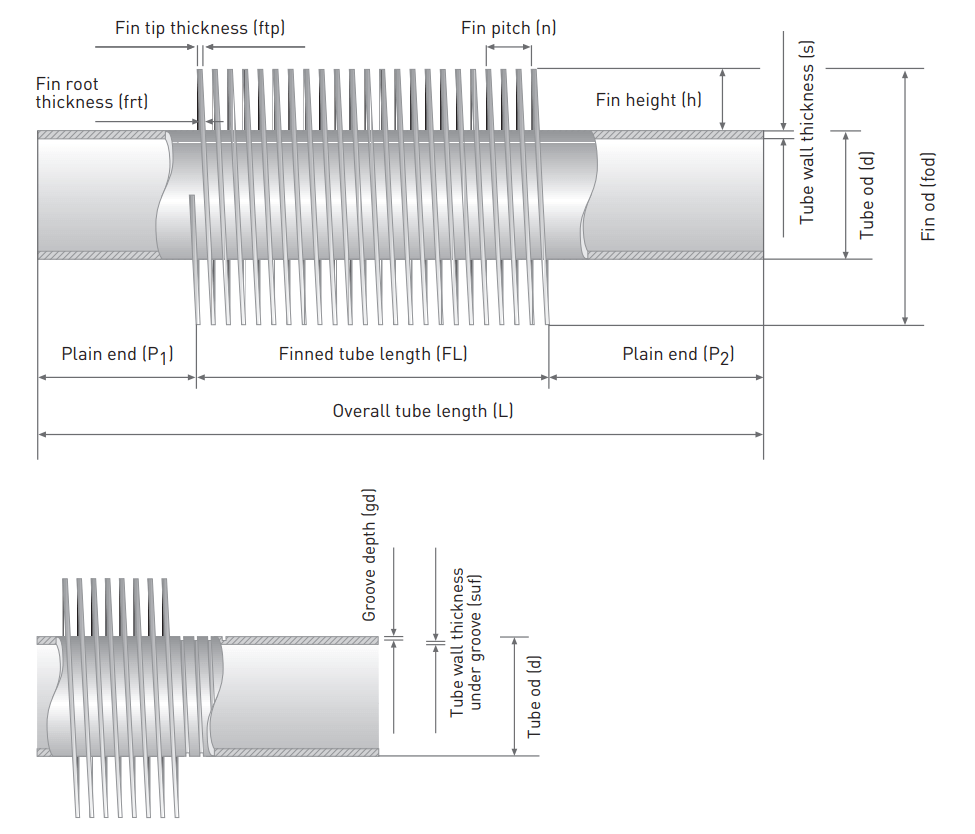
Extruded Fin Tube
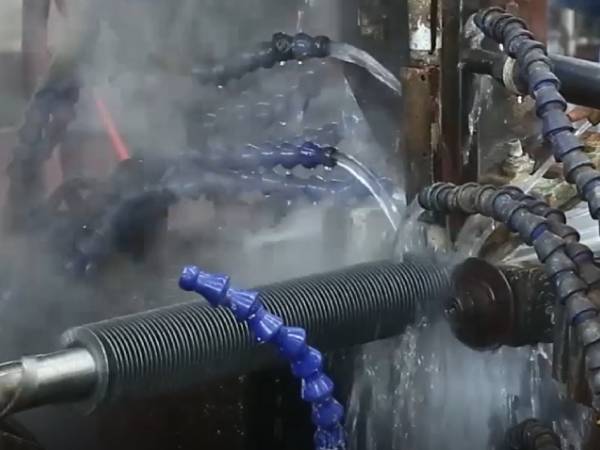
Extruded Fin Tube, also known as Bimetallic Fin Tube, consists of a base tube and aluminum fins closely fitted to the outside. The base tube is made from various materials, such as carbon steel, stainless steel, or copper tubes. The unique feature of this type of finned tube is that the aluminum tube is cleverly sleeved around the outside of the base tube and then extruded into the fin shape by special rolling equipment. This process not only enhances the bonding between the fins and the base tube but also forms a thin aluminum base layer on the outside of the base tube, which wraps the base tube tightly, thus ensuring the overall strength and stability of the finned tube.
L-Foot Fin Tube
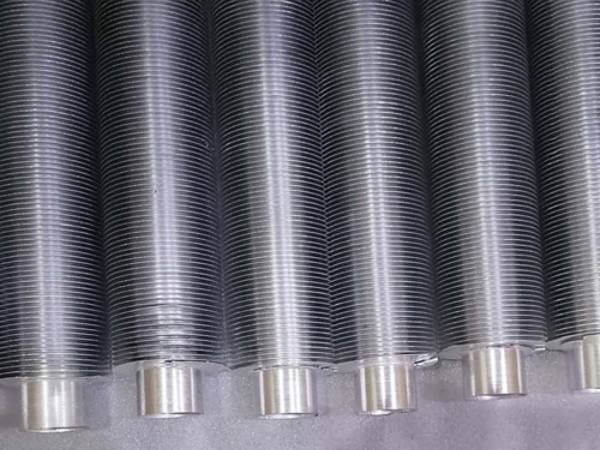
The aluminum or copper fins are folded into an L-shape and wound in a continuous spiral under tension around the outer surface of the base tube. The trapezoidal cross-section formed by the calendering of the L-type finned tube matches the size of the density distribution of heat flow, and the tube sheet combines tightly with high thermal efficiency.
Working temperature: 230°C
Characteristics: The use of a winding process, high production efficiency, uniform sheet spacing, good heat transfer, and high finning ratio, the base tube can be protected from air erosion.
Applications:
- Air conditioning and refrigeration: such as the condenser and evaporator of air conditioners, can enhance the heat exchange effect and optimize cooling and heating.
- In industrial production: chemical industry, petrochemical heating furnaces and coolers help with accurate temperature control.
- The electric power industry, such as waste heat recovery equipment in power plants, and air preheaters, facilitates the use of energy and improves system efficiency.
- Food processing industry: used in drying and sterilization equipment, to ensure accurate temperature control.
- Automobile manufacturing, commonly used in car radiators, to maintain the normal operating temperature of the engine.
- Pharmaceutical industry: the fin tube plays a key role in the drying, heating and cooling aspects of drug production.
- The textile industry: is used in textile machinery heating and cooling devices to ensure the stability of the production process.
- HVAC systems: such as centralized heating and ventilation of the heat exchanger, improve energy efficiency.
- Electronic equipment cooling, for high-power electronic equipment cooling, to prevent overheating damage.
LL-Foot Fin
Known as Double L fin, the fins are created from strips in a similar way to the L type except that the foot is prepared into a carefully controlled stepped double L shape, rolled into a taper that allows it to curl. The LL-Foot Fin – Overlapped L is next helically coiled onto a tube under tension. The fin clings the tube, with one fin overhanging the foot of the next fin and the base tube completely covered. The tube is well protected from corrosion as a result of this. In corrosive settings, this form of tube is frequently used as an alternative to the more expensive extruded type fin.
G-Type Embedded Fin Tube
Metal is merely shifted, not removed, by a helical groove 0.2-0.3 mm (0.008-0.012 in) plowed into the outside of the base-tube wall. The displaced metal is rolled back on each side of the fin to hold it in place after the aluminum fin is physically wound into the groove under strain. This is why it’s also known as an embedded finned tube. The thickness beneath the groove is the effective thickness of the base-tube wall. This kind provides great thermal and mechanical contact between the fin and the groove. Even though the base tube metal is exposed to the outside, testing conducted under server settings revealed that long-term corrosion is required before any bond failure develops. The G-type fin tube can withstand temperatures of up to 750 degrees Fahrenheit (450 C degrees)
KL Footed Fin
The KL fin is also known as the knurled L fin. This finned tube is almost identical to the Wrap-On fin and is made using both Wrap-On and Embedded techniques. The fins are made from strips that have been prepared into an L shape that is comparable to the L type, then rolled into a taper that causes it to curl. It is then helically wound onto the tube in a continuous loop under tension. The tube is hugged by the fin. A spinning tool knurls the base tube, and then the foot of the fin is knurled into the knurling of the base tube, resulting in a tight bond and improved thermal performance.
The foot of one fin bumps up against the next fin if the correct fin strip is utilized, and there is no space between the fins. This helps to protect the tube from corrosion. In a similar way to L fins, the fins are attached at each end to prevent unwinding. In applications involving metal, KL -Foot tension wound finned tubes are typically employed. Up to 320°C (608°F) maximum operating temperature
Low Fin Tube
Integral Fin Tube is another name for the ‘Low Fin Tube.’ In today’s industry, this style of fin tube is commonly employed. Low Fin Tubes/Integral Fin Tubes are becoming more popular in fluid heat exchangers. Unlike other Fin Tubes, their use isn’t restricted to air-to-liquid heat exchangers. As a result, they’re also found in a variety of Shell and Tube heat exchangers.
The fins are made by rolling the fin inside the base tube. The height of the fins is extremely low. However, by increasing the number of fins per inch or the fin density, the heat transmission area can be considerably improved. The rolling is done using a specific machine, and the finished product is available in both straight and U-bend configurations.
Welded Fin Tube
The finning in this sort of Fin Tube is Spirally Wound, as the name implies. Spirally winding the fin around the Base Tube and Pipe is how the fins are made. During winding, the fin is continuously welded to the tube using high-frequency welding, resulting in the strongest bond possible.
This sort of Fin Tube is employed in applications where there is mechanical stress, such as constant vibrations.
The nearly flawless heat transfer efficiency is also ensured by the welding link between the Tube and the Fin. It may also provide the widest temperature variations.
These Fin Tubes are used in RADIATORS, AIR PREHEATERS, WASTE HEAT RECOVERY SYSTEMS, BOILER FIN TUBES, and other industries such as power plants, chemical plants, steel plants, and chiller plants.
Serrated Fin Tube
Serrated fins are produced by slitting the fin strip equally spaced during production. A base 5mm (0.19”) high remains unslitted to form the continuous fin foot. When the finstrip is helically wound onto the tube the serrated part of the fin strip divides the outer end thus forming rectangular segments.
Solid and serrated fins can have more surface area depending on tube diameter, fin height, fin thickness, and serration size. Serrated fins promote slightly higher heat transfer but also have slightly higher pressure drop. The thermal performance of the two kinds of fins is similar when compared at the same pressure drop. Solid fins are somewhat heavier and usually more expensive than serrated fins.
Longitudinal Finned Tube
Longitudinal Finned Tube is produced by high-frequency resistance welding fins in the longitudinal direction with the length of the tubes. Fin strip material shall be compatible with and suitable for standard frequency resistance welding to the specified tube material. Before applying the fins, the tube outside surface shall be properly prepared to ensure that the fin-to-tube weld is sound. The fin strip is first bent into a U-shaped channel so that each leg of the U will be a fin. The channels were cut into a suitable length and oriented along the length of the tubes and resistance welded in place. The channels weld in pairs, opposed — therefore the number of fins specified always be multiple.
Stainless Steel Finned Tube
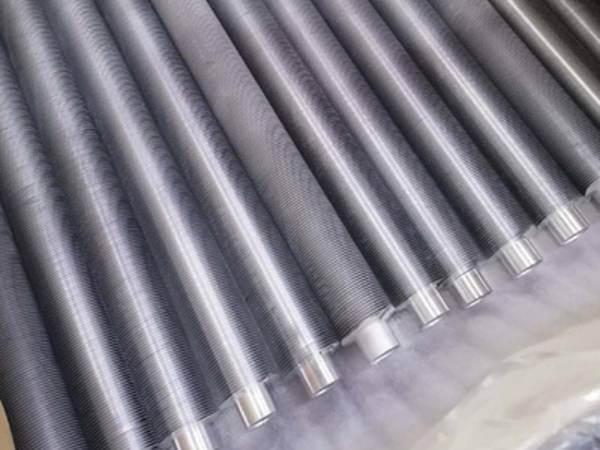
Stainless steel finned tube contact thermal resistance is low, the product can be in a wide range of temperature changes to maintain a stable low value, the entire product of the heat transfer coefficient is high, in the use of sudden changes in temperature and vibration has a good resistance, the unit length of the heat transfer area is large, the heat transfer is high, the structure, the life expectancy is long; fins have a smooth surface, no burrs, no wrinkles, not easy to scaling, easy to clean and remove the surface of the water, low flow resistance, can be a long-term Maintain good heat transfer performance.
Stainless steel finned tube has high strength, small flow loss, strong corrosion resistance, not easy to deform under long-term hot and cold working conditions, and long working life. The whole rolled fins are smooth, with no burrs, no wrinkles, and easy to clean, in the heating and air conditioning project for wet cooling is easy to exclude the fins outside the surface of the condensate, in the drying and heating and other heat exchange occasions are not easy to dust, scaling.
Stainless steel finned tube in the production process is mainly 304 stainless steel processing made in the use of the two mediums mainly for heat exchange, laser welded stainless steel finned tube process, excellent performance, is the boiler, power generation, petrochemical, HVAC, refrigeration, air-conditioning and other industries, heat exchange, waste heat recycling of alternative products.
Stainless steel finned tube in use can effectively improve the efficiency of the heat exchanger, to a certain extent, to effectively extend its life, reduce the volume and save materials, the whole rolled finned tube without contact thermal resistance, heat transfer performance, high strength, resistance to heat vibration and mechanical vibration, good thermal expansion performance.
Finned Tubes for Close-Coupling
- The use of electric power welding will clean the surface of the tube wall coated with solder, and then the fins strung to the tube, and then the finned tube at both ends were connected to the power supply, the high temperature will prompt the metal in the flux completely melted, the tube and the fins will be welded up to play the effect of the dense joint.
- Dip-plating method, dip-plating before the need to clean the fin and tube surface oil and oxides, the use of hydrochloric acid or sulfuric acid to add the appropriate amount of oxidant to clean, if the copper fins can only use dilute sulfuric acid to clean the clean fins should also be immersed in a solution containing ammonium chloride, and then placed in a molten tin tank or zinc tank to go, after the melting of the tin and zinc solution will flow directly into the gap between the fins and tubes, not only can effectively fill the gap, after the solution cools down but also form a protective coating, the dip-plating method is relatively costly. After melting the tin solution and zinc solution will flow directly into the fins and tubes between each other in the gap, not only can effectively fill the gap, in the solution after cooling also forms a protective coating, dip plating method is relatively more expensive, and the cost is also high.
- The contact welding method, will be a single side of the string directly welded to the pipe, the welding process can not occur deformation of the pipe can be put into the mandrel to assist in welding, and fins in the perforated position will be the phenomenon of folding, the need to use to the equipment will be more complex, must be selected accordingly to weld the equipment can be.
- The expansion of the way, the main use of hydraulic methods, will have been completed string of finned tube expansion, finned tube and tube confinement between close, not suitable for steel, with better ductility of non-ferrous metal material finned tube applicable.
Fin Pitch
Normally, the finned tube heat exchanger spacing and sheet height mainly affect the finning ratio, which has a great relationship with the membrane heat transfer coefficient of the medium inside and outside the tube. If the difference between the membrane heat transfer coefficient inside and outside the tube is large, the finned tube with a larger finning ratio should be selected, such as steam heating air. When there is a phase change in the medium on one side, the difference in the heat transfer coefficient will be larger, such as the exchange of hot and cold air, when the hot air falls below the lu point, you can use finned tube heat exchanger. In the case of air-to-air heat exchange without phase change, or water-to-water heat exchange, a bare tube is usually more suitable. Of course, the low-finned tube can also be used, because at this time belongs to the weak heat-giving coefficient, strengthening either side of it with the corresponding effect. However, too large a finning ratio is not obvious, good tube inside and outside the contact area at the same time to strengthen, you can use the spiral tube or grooved tube.
The distance between the fins is mainly to consider the accumulation of dust, dust, simple cleaning and other factors, and at the same time need to strictly comply with the requirements of the equipment on the pressure drop and so on. Arrangement, the spacing between the tube is not easy to be too large, generally > 1mm or more suitable for the tube. In the process of heat exchange, air flows through the finned tube heat exchanger, mainly fins positive and negative two sides involved in heat exchange. With two finned tubes in the middle part of only a small amount of radiation heat transfer, the heat transfer effect is not obvious. This part of no fins, and no resistance, and air is easy to penetrate. In the process of air heating, the cold air without heat exchange will form a neutralization with the heated air passing through the middle of the fins, which reduces the effect of heat exchange. Compared with the outer finned tube heat exchanger, the tube spacing is only 0.5mm larger than the outer diameter of the fins, which shows the importance of the tube spacing when the finned tubes are arranged.
Finned tube radiator is one of the most widely used heat transfer equipment in gas and liquid heat exchangers. It achieves the purpose of strengthening heat transfer by adding fins to the common base tube. The base tube can be made of steel, stainless steel, copper, etc. The fins can also be made of steel strips, stainless steel strips, copper strips, aluminum strips, etc.
Disadvantages of Finned Tube Heat Exchanger
- Larger size and higher cost: The fin design increases the heat dissipation area and improves the efficiency of heat dissipation, but as a result, it may also increase the size and weight of the equipment and may not be well suited for installations where space is limited. High-quality metal materials have good thermal conductivity, but may also increase the cost of the equipment.
- Difficult to clean and maintain: The presence of fins makes it relatively difficult to clean and maintain the radiator as they tend to accumulate dust and debris, which affects heat dissipation. Users need to clean and maintain the radiator regularly to ensure its proper operation.
- Relatively high manufacturing costs: The need for additional fins and complex machining processes increases the manufacturing cost of the radiator, which in turn increases the selling price of the product.
- Poor adaptability to the environment: finned tube radiators require high ambient temperatures and air circulation, which may affect their cooling effect and service life if the environmental conditions are poor.
- Limited pressure tolerance and corrosion resistance: the presence of fins makes the structure of the pipe complex, which may cause it to be easily deformed or damaged under high-pressure environments, while the corrosion resistance may also be affected.