Tube is mainly divided into seamless tube and welded tube in manufacturing technology, the main difference is whether the tube wall has a welded seam.
Seamless tube is made using a round billet as raw material for piercing, the manufacturing process of seamless pipes includes hot rolling, cold rolling, cold drawing, extrusion and many other methods. There are no welded seams on the surface, resulting in high strength and pressure resistance, and excellent performance in high-pressure and high-temperature environments.
Welded tube is made of a plate or strip after being rolled and shaped by a series of rollers and molds, two edges are welded to connect longitudinally, and there is a welded seam on the inner wall of the tube.
Seamless VS welded tube in the manufacturing process.
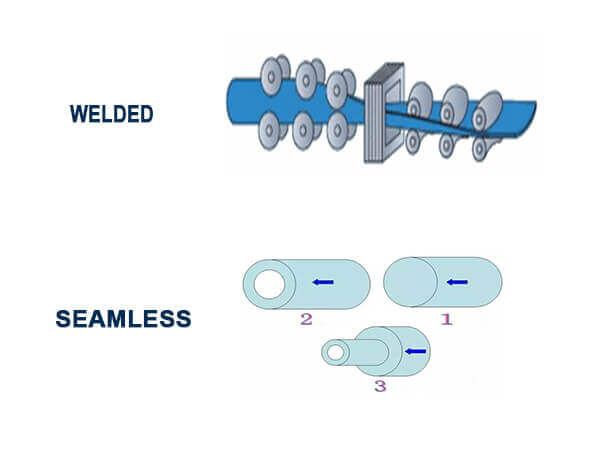
Welded Tube Manufacturing Process
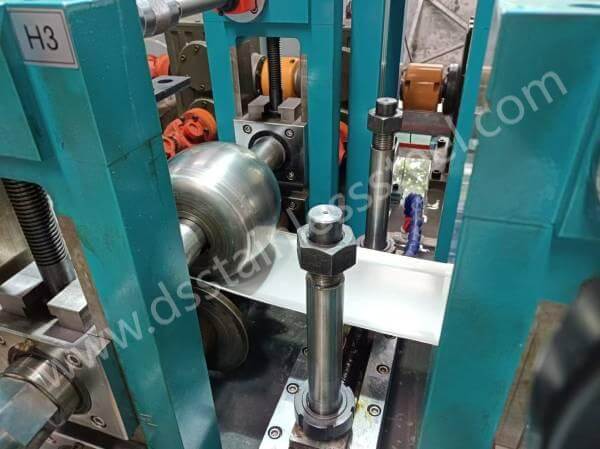
Welded tube is made from strip and coil that is passed through grooved rollers till the shape is formed and the free edges are properly shaped for welding, cold forming is performed step by step from flat strip into a round profile, and the edges are welded together as they approach the welding rolls.
The typical welding method for strip welded tubes is traditionally autogenous tungsten inert gas (TIG), TIG welding method has some advantages that can effectively protect weld seam.
DONGSHANG STAINLESS produces TIG welding stainless steel tubing for boiler, heat exchanger, condenser, with excellent performance in corrosive environments.
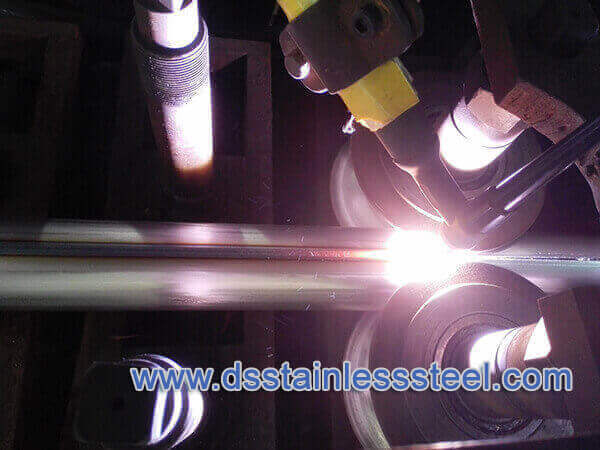
Depending on the outer dimension, wall thickness and final application, there are different ways of manufacturing welded tubes and pipes and different manufacturing methods, like laser welding, plasma welding, ERW, EFW, etc.
When large outside diameter or heavy wall or both welded tubes & pipes are produced, pipe is made from plate or sheet, the forming is done in a roller bending machine or a hydraulic press, then some steps are the same with strip welded tubes.
There are different welding methods and processes, for large diameter and heavy wall pipes, EFW, ERW and other welding methods can be adopted, for large-diameter pipes, double and spiral seams may needed.
- Coil
- Inspection and analysis
- Slitting
- Auto-welding
- Seam-grinding
- Solution treatment
- Cut to length
- Straightening
- Picking
- End-facing
- Eddy current test
- Hydrostatic test
- Final inspection
- Marking
- packing
Advantages of Welded Tube
- Lower cost compared to the equivalent seamless alternative.
- Short lead time.
- Better surface finishing of outside and inside, the internal material surface for welded tubes can be checked before manufacture.
- Thinner wall thickness, and more uniform.
- Tighter tolerance.
Seamless Tube Manufacturing Process
Seamless tubes are generally made in complex steps starting with the drilled hollows from billets, then rolling and drawing the material to the desired sizes, cold pilgering is the preferred production process since this technique provides a high forming rate, narrow tolerances and good productivity yields, but cold drawing gives narrower tolerance ranges and better surface quality. Seamless tube dimension is difficult to control compared to the welded tube in outside diameter and wall thickness.
1. Round Bar
Round steel from the raw material warehouse, according to the requirements of the process to calculate the length of round steel cutting, segmented line on the round steel, bow sawing machine start the wheel blade along the segmented line cut, cut off the round steel according to the type of steel, heat number, production batch number, specifications are stacked separately, the end of the end of the use of different colors of paint to distinguish.
2. Inspection and Analysis
3. Cut to length
4. Centering
the cross arm drilling machine involves first locating the center point in a section of round steel, creating a sample eye, and then fixing it vertically on the drilling table for accurate centering. After centering, the round steel is stacked according to steel type, heat number, specification and production lot number.
5. Peel
6. Heating
Round steel heating equipment includes gas-fired tilting-bottom furnace and gas-fired box-type furnace, which are used to heat the large-volume incoming materials with gas-fired tilting-bottom furnace, and to heat the small-volume incoming materials with gas-fired box-type furnace. When entering the furnace, the round steel of different steel types, furnace numbers and specifications are separated by the old outer film, and when the round steel is heated, the steel turner will turn the steel with tools to ensure the round steel is heated evenly.
7. Perforation
Use perforating machine and air compressor. According to the specifications of the perforated round steel, select the corresponding guide plate and molybdenum top head, use the perforating machine to perforate the heated round steel, and the perforated barren pipe is randomly put into the pool to be cooled sufficiently.
8. Inspection
Inspection of the internal and external surfaces of the barren pipe is smooth and even, and there shall be no presence of flower skin, cracks, interlayers, deep pits, severe thread marks, tower irons, grease strips, wrapped heads and sickle heads. The surface defects of the barren pipe can be eliminated by local grinding. The inspected and qualified barren pipe or the inspected and qualified barren pipe after repairing and grinding of minor defects shall be bundled by the workshop bundler according to the requirements, and stacked according to the steel type, heat number, specification and production lot number of the barren pipe respectively.
9. Pickspanng
After straightening, the steel pipe needs to be pickled to remove the oxidized skin and impurities on the surface of the barren pipe. Steel pipe pickling is carried out in the pickling workshop, and the steel pipe is slowly lifted into the pickling tank for pickling with a traveling crane, and after pickling, the steel pipe is first cleaned in the water washing tank, and then the inner holes and outer surfaces of the steel pipe are rinsed with high-pressure clean water one by one.
10. Inspection of Surface
11. Lubricating
12. Cold drawing / cold rolspanng
The steel pipe is rolled through the rolls of the cold rolling mill, and is continuously cold deformed to change the size and length of the steel pipe. Cold rolled steel pipe is molded at a faster speed, with a large amount of deformation and a high yield.
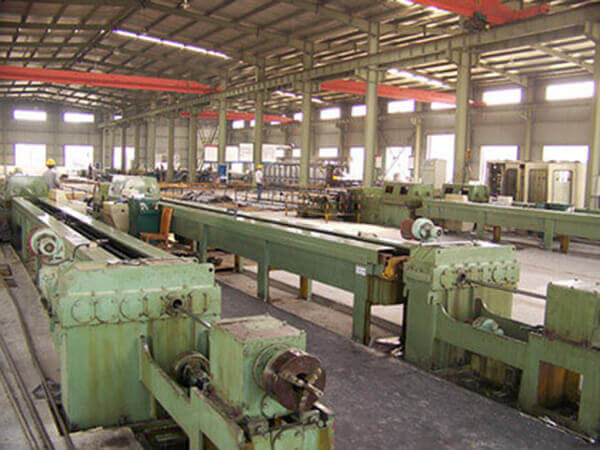
13. Degreasing
the purpose of degreasing is to remove the mill oil attached to the inner wall and outer surface of the steel pipe after rolling by shabu-shabu, so as not to contaminate the surface of the steel when annealing and to prevent carbonization.
14. Heat Treatment
Heat treatment is to restore the plastic shape of the material by recrystallization and to reduce the deformation resistance of the metal. The heat treatment equipment is a natural gas solution heat treatment furnace.
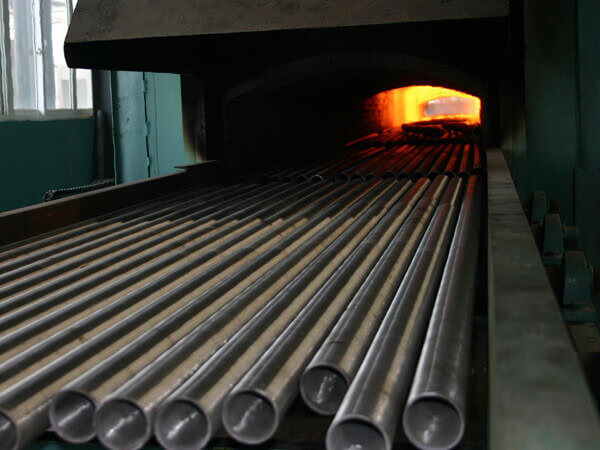
15. Straightening
16. Cut
17. Picking
After cutting the steel pipe for finished pickling, the purpose of which is surface passivation, so that the surface of the steel pipe to form a layer of oxidized protective film to enhance the performance of the steel pipe.
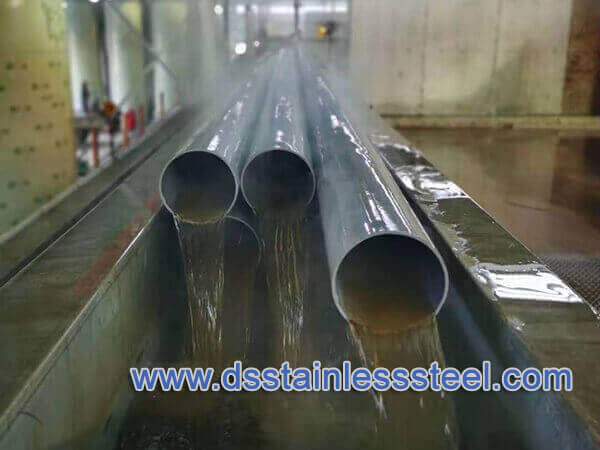
18. Final Inspection
Finished product inspection and testing process is mainly table inspection → eddy current probe → super probe → water pressure → air pressure several tests. Table inspection is mainly to manually check the surface of the steel pipe has no defects, the length of the steel pipe, whether the outer wall size is qualified; eddy current detection is mainly through the eddy current flaw detection machine to see whether there are holes in the steel pipe; ultrasonic flaw detection is mainly the use of ultrasonic flaw detection machine to check whether the steel pipe inside and outside of the cracks; water pressure, air pressure is the use of water compressors, air compressors to detect whether the steel pipe is leaking, leakage, so as to ensure that the steel pipe is intact.
19. Marking
Advantages of Seamless Tube
- Heavy and thick wall thickness.
- No weld seam. generally be considered as having better properties and corrosion resistance
- Better ovality or roundness
Seamless VS Welded Tube, What is the Difference?
The Difference | Seamless Tube | Welded Tube |
---|---|---|
Manufacturing Process | Drawn from a solid billet | Welding from strip, plate or sheet |
Surface | No seam | Better surface, a welding seam on the surface |
Cost | High cost and more expensive | Low cost and cheaper |
Size | Can be a heavy wall | More shapes, uniform thickness |
Lead times | More time due to complex processes, especially for small tubes | Fast relatively |
Strength | Stronger and more durable | Weeker |
Corrosion resistance | Better | Not good as seamless tube |
Applications | High-pressure and high-temperature | Structural and mechanical purpose |
Choosing Welded or Seamless Tube?
Despite many advantages of welded tubes, seamless tube is still treated better than welded type, especially used in rough environments, considered as higher strength, higher pressure, and better corrosion resistance.
Seamless and welded are mainly two tube types in the production process, there is a debate about whether seamless is better than welded for a long time.
Although with improved metallurgy and welding processes in welded tubes, the arguments typically focus on structural integrity and corrosion resistance in weld areas.
In reality, seamless & welded manufacturing processes both can provide tubes & pipes with quality, reliability and excellent corrosion resistance, which generally complement each other.
Depending on the specific application and cost aspect, decide which type is a better choice to use. Tubes and pipes can be produced in both seamless and welded types depending on application requirements, with Austenitic stainless steels, duplex and special grades.