We produce chemical injection lines and control lines in stainless steel and nickel alloys, the grades include 316L, 2205, 2507, 625, and 825, etc, these materials possess strong, corrosion-resistant, and reliable properties, they can be used in harsh environments. The small diameter and capillary tubing for the Chemical Injection Control Line are offered in bright annealed (BA) condition, and other finishes are available.
These line tubes meet all ASTM standards and operate effectively in difficult environments to maintain production flow. Lines are pressure-tested and certified before deployment. They are available for any length, max length reaches 10000 meters in coil with fewer welds. The coiled tubing can offer a wide range of encapsulated forms.
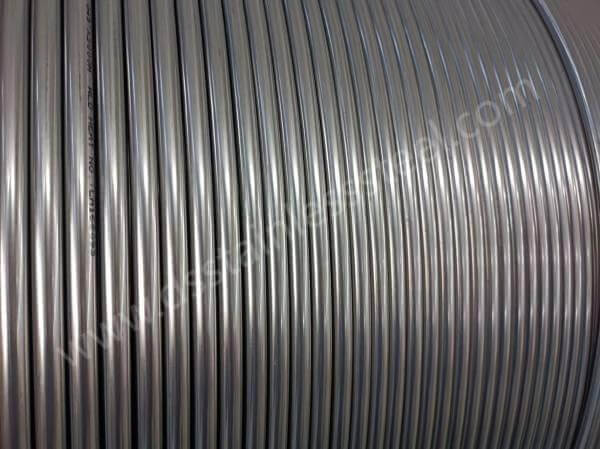
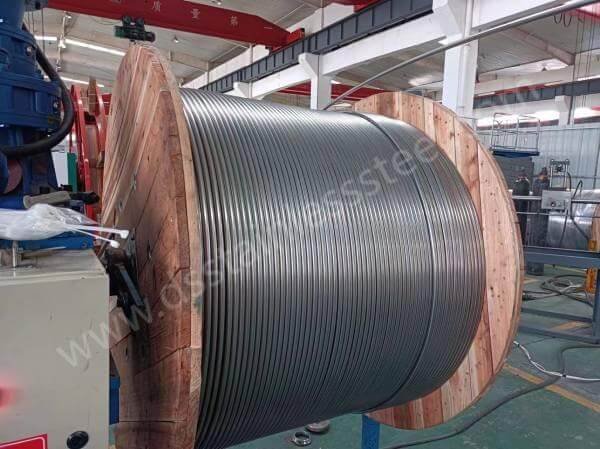
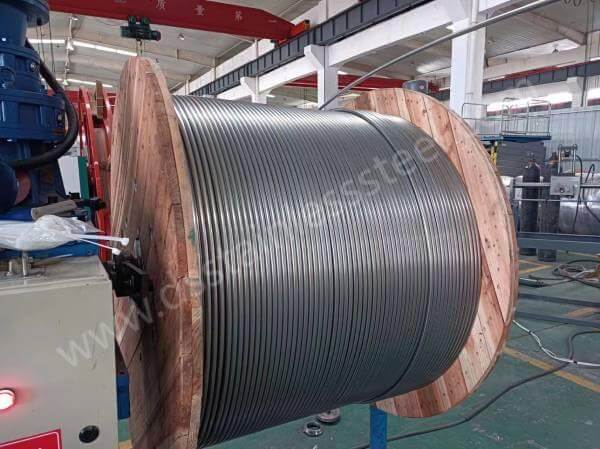
Chemical Injection Line and Control Line Coiled Tubing Specifications
Type | Stainless and Nickel Alloy Coil Tubing |
---|---|
tubing Specifications | ASTM A213/A269 seamless, A249/A269 welded tubing, A789 for duplex tubing |
Grades | 316/316L, 321, 2205, 625, 825, 800/800H |
Outside Diameter | 6.35, 7.94, 9.53, 12.7, 15.88, 25.4, 38.1 mm |
Wall Thickness | 0.71, 0.89, 1.0, 1.24, 1.65, 2.11 mm |
Length | Max 10000 meters |
Condition | Bright Annealing Finish |
Package | wooden drum or spool, metal reels |
Application | Subsea and downhole applications Harsh environments, such as high-pressure, high-temperature (HPHT) wells and corrosive conditions Tool recovery operations Chemical injection Annular gas venting Capillary pressure monitoring |
Stainless Steels and Nickel Alloys Grade
Grade | Standard | |
---|---|---|
Austenitic: | 316L | ASTM A-269 |
Duplex: | S31803/S32205 | ASTM A-789 |
S32750 | ASTM A-789 | |
Nickel alloy: | N08825 | ASTM B-704; ASTM B-423 |
N06625 | ASTM B-704; ASTM B-444 | |
CuNi alloy | Monel 400 | ASTM B-730; ASTM B-165 |
Mechanical Properties
Grade | Yield strength, psi (MPa) | Tensile strength, psi (MPa) | Elongation % |
---|---|---|---|
TP 316L | 32,000 (220) | 75,000 (515) | 35 |
Alloy 825 | 35,000 (240) | 80,000 (550) | 30 |
2205 | 70,000 (485) | 99,000 (680) | 25 |
2507 | 80,000 (550) | 116,000 (800) | 25 |
Standard Controlled Line Sizes
Tube OD | OD X Wall |
---|---|
⅛ in. | 0.125 x 0.028 in. (3.18 x 0.71 mm) |
0.125 x 0.035 in. (3.18 x 0.89 mm) | |
¼ in. | 0.25 x 0.035 in. (6.35 x 0.89 mm) |
0.25 x 0.049 in. (6.35 x 1.25 mm) | |
0.25 x 0.065 in. (6.35 x 1.65 mm) | |
⅜ in. | 0.375 x 0.035 in. (9.53 x .89 mm) |
0.375 x 0.049 in. (9.53 x 1.25 mm) | |
0.375 x 0.065 in. (9.35 x 1.65 mm) | |
½ in. | 0.5 x 0.049 in. (12.7 x 1.25 mm) |
0.5 x 0.065 in. (12.7 x 1.65 mm) | |
0.5 x 0.083 in. (12.7 x 2.11 mm) | |
⅝ in. | 0.625 x 0.049 in. (15.88 x 1.25 mm) |
0.625 x 0.065 in. (15.88 x 1.65 mm) | |
0.625 x 0.083 in. (15.88 x 2.11 mm |
Maximum Pressure (P) for TP 316L at 100°F (38°C)
Outside diameter, in. | Wall thickness, in. | Working pressure psi (MPa) | Burst pressure psi (MPa) | Collapse pressure psi (MPa) |
---|---|---|---|---|
1/4 | 0.035 | 6,600 (46) | 22,470 (155) | 6,600 (46) |
1/4 | 0.049 | 9,260 (64) | 27,400 (189) | 8,710 (60) |
1/4 | 0.065 | 12,280 (85) | 34,640 (239) | 10,750 (74) |
3/8 | 0.035 | 4,410 (30) | 19,160 (132) | 4,610 (32) |
3/8 | 0.049 | 6,170 (43) | 21,750 (150) | 6,220 (43) |
3/8 | 0.065 | 8,190 (56) | 25,260 (174) | 7,900 (54) |
3/8 | 0.083 | 10,450 (72) | 30,050 (207) | 9,570 (66) |
1/2 | 0.049 | 4,630 (32) | 19,460 (134) | 4,820 (33) |
1/2 | 0.065 | 6,140 (42) | 21,700 (150) | 6,200 (43) |
1/2 | 0.083 | 7,840 (54) | 24,600 (170) | 7,620 (53) |
5/8 | 0.049 | 3,700 (26) | 18,230 (126) | 3,930 (27) |
5/8 | 0.065 | 4,900 (34) | 19,860 (137) | 5,090 (35) |
5/8 | 0.083 | 6,270 (43) | 26,910 (151) | 6,310 (44) |
3/4 | 0.049 | 3,080 (21) | 17,470 (120) | 3,320 (23) |
3/4 | 0.065 | 4,090 (28) | 18,740 (129) | 4,310 (30) |
3/4 | 0.083 | 5,220 (36) | 20,310 (140) | 5,380 (37) |
Seamless Coiled Tubing
Seamless coiled tubing is manufactured by cold drawing and cold rolling process, a based billet is extruded into a tube and drawn to finished size. orbital welds are used to join lengths of the seamless coil to achieve smooth, strong tube lengths suitable for any good application, strong and error-free orbital welds join the lengths of the seamless coil together for the desired tube lengths.
Welded Coiled Tubing
Tubing lines are welded and drawn to homogenize the seam weld for a better sealing surface, rounder OD, and an improved external surface finish. After welding, the line is drawn through a reduction die and reworked externally to homogenize the seam weld. By drawing through a die, the line has an improved surface of tubes, a truly round OD, and an improved external surface finish, the ASTM B704 specification is for 625 and 825 nickel alloy welded tubes.
Coiled Tubing Control Line Forms and Applications
Hydraulic control tubing, hydraulic control lines, tubing encapsulated cables, chemical injection lines, pre-insulated tubes, multi-core tube bundles, umbilical cables, and cable-alloy pipes, fishing lines. The lines are widely used in petroleum, chemical, natural gas, shipbuilding, food, environmental protection, and other industries.
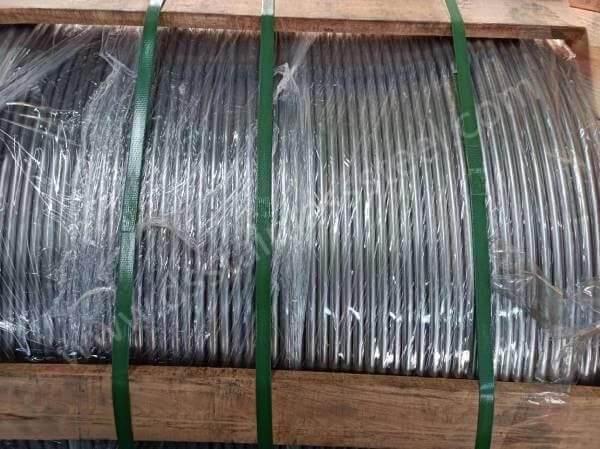
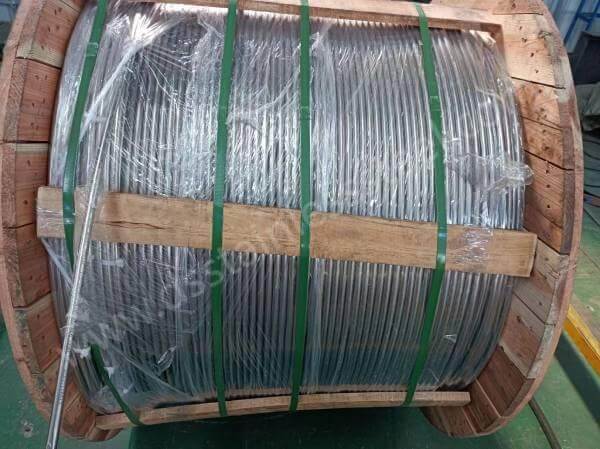
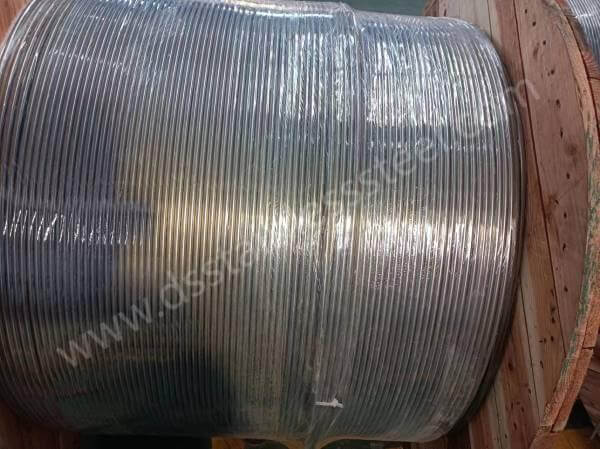
Quality and Tests
- NDT (Pressure test, Eddy Current test)
- Mechanical Test (Tension Test, Flaring Test, Flattening Test, Hardness Test, Hydraulic test)
- Metal Test (Metallographic Analysis, Impact Test/low temperature)
- Chemical Analysis (Photoelectric Emission Spectroscopic)
Coiled Tubing Sizes
Imperial size | Metric size | ||
---|---|---|---|
OD inch | WT inch | OD mm | WT mm |
1/8 (0.125) | 0.028 | 3.18 | 0.71 |
0.035 | 3.18 | 0.89 | |
3/16 (0.188) | 0.028 | 4.76 | 0.71 |
0.035 | 4.76 | 0.89 | |
0.049 | 4.76 | 1.24 | |
1/4 (0.250) | 0.035 | 6.35 | 0.89 |
0.049 | 6.35 | 1.24 | |
0.065 | 6.35 | 1.65 | |
0.083 | 6.35 | 2.11 | |
3/8 (0.375) | 0.035 | 9.53 | 0.89 |
0.049 | 9.53 | 1.24 | |
0.065 | 9.53 | 1.65 | |
0.083 | 9.53 | 2.11 | |
1/2 (0.500) | 0.035 | 12.7 | 0.89 |
0.049 | 12.7 | 1.24 | |
0.065 | 12.7 | 1.65 | |
0.083 | 12.7 | 2.1 |
Coiled tubing
Coiled tubing (CT) refers to a continuous and long length of small diameter metal pipe, generally, this type of tubing unit consists of other components, the unit size can be small or large depending on application, and a reel may be used for storage and transportation.
We have specialized in stainless steel coiled-shape tubing for years, having the facility to produce superior coil tubing, with a variety of sizes and dimensions.
Coiled Tubing Types
Welded coiled tubes and seamless coiled tubes are both offered as standards, the common specification is ASTM A269, the cold drawing manufacturing process improves tubing performance, and annealing pickling and bright annealing finishes are for specific uses.
After the straight tubing is finished, the tubing is coiled, and a slightly formed circle shape into a reel, maximum length up to 1000 meters.
Stainless Steel Grades
Stainless steel is a large group with good corrosion resistance, meanwhile, the material has perfect toughness and formability under annealed conditions, which properties make tubing easy to fabricate and bend.
300 series stainless steels are widely used because these grades provide balanced characteristics for application, typical grades are TP304, and TP316L stainless steel.
Duplex steel is also for coil tubing, particularly in a corrosion environment, common grade is 2205 duplex.
- Austenitic: 304, 304L, 316, 316L, 316H, 316Ti, 317/317L, 347/347H, 321/321H, 310/S, 904L, 254SMO
- Ferritic: 409, 430, 439, 441, 434, 436, 444, 446
- Martensitic: 403, 410, 410S, 414/L, 418, 420, 440, 416
- Duplex: 2205, S31803, S32750, S32760
Sizes
Stainless steel coiled tubing dimensions range from 3.0 mm to 45 mm in outside diameter, and 0.3 mm to 2.0 mm in wall thickness, maximum length reaching 1000 meters, welded capillary coiled tubing provides thinner wall for specific purposes.
Quality Inspection
Then tubing is in straight condition, eddy current test is conducted via an in-line device, to detect leaks and defect situations, small size weights in the coiling can be carried out by air underwater testing.
Advantages
Coiled tubing usually is long length tube coil, compared to straight tubing, it does not require connecting the tubing end with a fitting, therefore, it saves time for installation, and it is cost cost-effective way, with less maintenance.
Application
Industrial use: heat exchanger, boiler, petroleum, chemical, fertilizer, chemical fiber, pharmaceutical, nuclear power.
Fluid use: beverage, beer, milk, water supply system, medical equipment.
Mechanical structure: printing and dyeing, printing, textile machinery, medical equipment, kitchen equipment, automobile and ship accessories, construction and decoration.