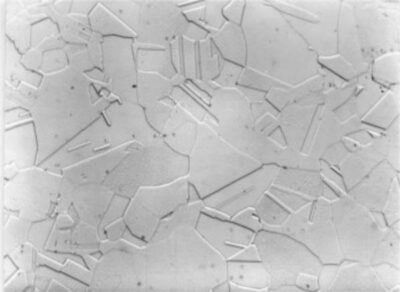
Austenitic stainless steel refers to the austenitic organization that has a matrix with a face-centered cubic crystal structure at room temperature, it contains chromium-nickel, Cr-Mn and chromium-nickel-manganese steels. Austenitic stainless steels are nonmagnetic, have good weldability, and possess high corrosion resistance.
Austenitic stainless steels are the most diversified and the largest family of stainless steels, making up about two-thirds of all stainless steel production, it is a versatile and popular material that offers numerous advantages in various applications. Its unique combination of strength, corrosion resistance, and formability makes it a popular choice for industries from construction to food processing.
Austenitic stainless steel is used in countless products, from kitchen utensils to chemical plants. Its hygienic qualities make it suitable for use in the medical field and the food industry, where cleanliness is essential. Due to its aesthetic appeal, it also plays a vital role in building structures.
Despite all these advantages, there are some disadvantages to using austenitic stainless steel. The higher cost compared to other types of stainless steel can be a limiting factor for budget-conscious projects or industries. Additionally, while it offers excellent corrosion resistance, it may not be suitable for highly acidic or chloride-containing environments.
Austenitic Stainless Steel Grade
They typically contain greater than 12% chromium, which provides corrosion resistance by forming a persistent, spontaneously regenerating chrome oxide surface layer. Other alloying elements, such as nickel, manganese, and molybdenum, are frequently added according to the application’s needs. Carbon is also present in minor amounts, either purposely supplied or as an impurity.
Austenitic stainless steels are distinguished from other highly alloyed steels and ferritic steels by their crystal structure: the austenitic alloys have an FCC crystal structure compared with the BCC structure of the ferritic alloys.
200 Series Stainless Steel
200 series stainless steel material is a chromium-manganese austenitic stainless steel alias, this type of material is in the chromium-nickel austenitic stainless steel based on adding manganese and nitrogen to the steel instead of the precious metal nickel elements and the development of this material in the austenitic elements, in addition to manganese and nitrogen, there is generally an appropriate amount of nickel, manganese in the steel to play a role in stabilizing austenite, due to the nitrogen is very good solid solution strengthening effect, improve the strength of austenitic The strength of stainless steel. 200 series stainless steel, nickel content is lower, so the price is about half of the 300 series. However, in terms of corrosion resistance and toughness, it is far inferior to the 300 series and is more suitable for use in areas such as cookware and food processing. Due to its limited resistance to atmospheric corrosion, it is not recommended for use in critical areas such as construction and medical devices.
300 Series Stainless Steel
One of the most common types of austenitic stainless steels is type 304 (UNS S30400), also known as 18/8 because it contains approximately 18% chromium and 8% nickel. More than half of the stainless steels produced worldwide are of type 304, and they are available in various products and finishes. SS304 is used not only in the oil and gas and chemical industries but also in the food industry for making kitchen appliances, sinks, pots, pans, and flatware. SS304 has higher corrosion resistance but poorer electrical and thermal conductivity and magnetic properties compared with carbon steel. The chemical composition of different austenitic stainless steels can be varied by lowering the carbon content; adding titanium, niobium, or tantalum to prevent chromium carbide formation; or adding molybdenum to increase the corrosion resistance to localized corrosion types like pitting and CLSCC.
Adding approximately 2% molybdenum to SS304 creates SS316 that has higher resistance against pitting corrosion than SS304. The other properties of SS304 and SS316 are similar as both are nonmagnetic, nonhardenable through heat treatment, resist general corrosion, and are easily formed and fabricated. SS316 is more expensive than SS304. Although cost is an important factor for material selection, SS316 is the only austenitic stainless steel grade that is used for valves in the Norwegian offshore industry owing to its higher resistance to the corrosive offshore environment compared with most of the other series 300 grades. Adding almost 1% molybdenum to SS316 produces SS317 which has even higher pitting resistance than SS316.
Super Austenitic Stainless Steel
Super Austenitic Stainless Steel is a class of high quality materials with high corrosion resistance, high strength and good toughness, 904L stainless steel is a super austenitic stainless steel with very high corrosion resistance, commonly used in strong corrosive environments. 254SMO stainless steel is a super austenitic stainless steel with higher levels of molybdenum and nitrogen, that offers excellent performance in the face of highly corrosive and high-temperature environments.
Grades of Austenitic Stainless Steel and Chemical Compositions (mass%)
Grade | Carbon | Nitrogen | Manganese | Silicon | Chromium | Nickel | Molybdenum | Cupper | Other | PREN |
---|---|---|---|---|---|---|---|---|---|---|
S20100 | 0.15 | 0.25 | 5.5–7.5 | 1.00 | 16.0–18.0 | 3.5–5.5 | 19 | |||
S30100 | 0.15 | 2.00 | 1.00 | 16.0–18.0 | 6.0–8.0 | 17 | ||||
S30400 | 0.08 | 0.10 | 2.00 | 1.00 | 18.0–20.0 | 8.0–10.5 | 19 | |||
S30500 | 0.12 | 2.00 | 0.75 | 17.0–19.0 | 10.5–13.0 | 18 | ||||
S31600 | 0.08 | 0.10 | 2.00 | 1.00 | 16.0–18.0 | 10.0–14.0 | 2.0–3.0 | 25 | ||
S31700 | 0.08 | 0.10 | 2.00 | 1.00 | 18.0–20.0 | 11.0–15.0 | 3.0–4.0 | 31 | ||
S31254 | 0.03 | 0.18–0.25 | 1.00 | 0.80 | 19.5–20.5 | 17.5–18.5 | 6.0–6.5 | 0.50–1.00 | 44 | |
S31008 | 0.08 | 2.00 | 1.50 | 24.0–26.0 | 19.0–22.0 | 25 | ||||
S32100 | 0.08 | 0.10 | 2.00 | 0.75 | 17.0–19.0 | 9.0–12.0 | 5x(C+N)−0.70 Ti | 18 | ||
S34700 | 0.08 | 2.00 | 0.75 | 17.0–19.0 | 9.0–13.0 | 10xC−1.00 Nb | 18 | |||
S30815 | 0.05–0.10 | 0.14–0.20 | 0.80 | 1.40–2.00 | 20.0–22.0 | 10.0–12.0 | 0.03–0.08 Ce | 24 |
Source: PREN = %Cr+3.3[(%Mo)+0.5(%W)]+16(%N).
Properties of Austenitic Stainless Steel
High Corrosion Resistance
Austenitic stainless steels are known for their excellent properties, making them a popular choice across a variety of industries. One of its key properties is its high corrosion resistance, which makes it suitable for applications that are often exposed to wet or harsh environments. This stainless steel contains chromium and nickel, making it resistant to rust and corrosion.
Fabricability
Austenitic stainless steel has excellent formability properties. It can be easily made into different shapes and sizes without compromising its structural integrity. This property allows manufacturers to create complex designs and customized products to meet specific requirements.
Excellent Toughness
Another advantage of austenitic stainless steel is its excellent toughness at both low and high temperatures. It maintains ductility even under extreme conditions, making it ideal for applications involving temperature fluctuations or low-temperature environments.
Excellent Weldability
This stainless steel has excellent weldability and can be easily joined to other materials or components. Its ability to withstand the welding process without significant loss of mechanical properties makes it highly versatile in the manufacturing process.
Austenitic stainless steel has good weldability, mainly due to its non-magnetic, high toughness and high plasticity properties. Austenitic stainless steel at room temperature with austenitic organisation, the main components include chromium (Cr), nickel (Ni), carbon (C), etc., of which the chromium and nickel content of 18% and 8% to 25%, carbon content of about 0.1%. Because of its non-magnetic, high toughness and high plasticity, austenitic stainless steel is not easy to produce cracks in the welding process, and the welded joints have good mechanical properties.
In the welding process, austenitic stainless steel can be welded by various welding methods, such as manual arc welding, gas shielded welding and so on. After welding, the mechanical properties of the welded area are similar to those of the parent material, which can meet the needs of most applications
Aesthetic Appeal
In addition, austenitic stainless steel has excellent aesthetic appeal due to its smooth surface finish and lustrous appearance. This factor makes it widely used in architectural structures, interior design elements and decorative items where visual appeal is important.
Disadvantages of Austenitic Stainless Steel
HighCost
A major disadvantage is its relatively high cost compared to other types of stainless or carbon steel. The additional alloying elements required to achieve the desired properties result in higher prices.
Lower Strength
Another limitation is its lower strength compared to martensitic or ferritic stainless steel. While this may not be a problem in many applications, situations where maximum strength is required may require consideration of alternative materials.
Limitation to Resist Stress Corrosion Cracking
Despite the overall excellent corrosion resistance, certain corrosive chemicals (e.g., sulfuric acid) can cause stress corrosion cracking in austenitic stainless steels under certain conditions.
Austenitic vs Ferritic Stainless Steel
- Microstructure: Ferritic stainless steels have a body-centered cubic (BCC) crystal structure, while austenitic stainless steels have a face-centered cubic (FCC) crystal structure. This microstructural difference affects their properties and performance.
- Composition: Ferritic stainless steels usually contain chromium as the main alloying element (in the range of 10-30%), almost no nickel, and may contain small amounts of other alloying elements such as manganese, silicon and molybdenum. On the other hand, austenitic stainless steels contain chromium (usually 16-26 percent) and nickel (usually 6-22 percent) as the main alloying elements, as well as small amounts of other elements such as manganese, nitrogen and molybdenum.
- Properties: Ferritic stainless steel is known for its good corrosion resistance in mild environments, moderate strength and magnetic properties. It is also relatively less ductile and less tough than austenitic stainless steels. On the other hand, austenitic stainless steels offer excellent corrosion resistance in a variety of environments, have high strength and ductility, and are non-magnetic in the annealed state.
- Applications: Ferritic stainless steels are typically used in applications requiring corrosion resistance in mild environments and moderate mechanical properties, such as automotive exhaust systems, kitchen utensils and decorative parts. Austenitic stainless steels are used in a wide range of applications due to their excellent corrosion resistance and mechanical properties, including, but not limited to, food processing equipment, chemical processing plants, pharmaceuticals, medical equipment and marine applications.
Austenitic vs Martensitic Stainless Steel
Crystal Structure
- Austenite: has a face-centered cubic structure, carbon and nitrogen and other interstitial atoms are located in the center of the octahedral interstitials of the austenite cell and the center of the face-centered cubic cell and the midpoints of the prisms.
- Martensite: with body-centered square structure, usually showing flaky or lath-like, high-carbon steel quenched to obtain needle martensite.
Physical Properties
- Density: The volume of austenite expands as it transforms to martensite, so that the density of martensite is lower than that of austenite.
- Hardness: martensite has high strength and high hardness, but poor toughness, showing hard and brittle; austenite hardness is lower, but has good plasticity and some toughness.
- Magnetism: austenite does not have ferromagnetism, while martensite has ferromagnetism.
Application
- Martensite: Due to its high strength and hardness, it is commonly used in the manufacture of knives, scissors, bearings and moulds, which require high mechanical properties. It is also used in petrochemicals, power generation equipment and high-temperature valves.
- Austenitic: Because of its excellent corrosion resistance and processing performance, it is widely used in food processing equipment, medical equipment, chemical equipment and building decoration. It is especially used in applications where corrosion resistance and good processing performance are required, such as marine engineering and the chemical industry.
Chemical composition
- Austenitic stainless steel: contains low carbon content (less than 0.1%) and high content of chromium (16% -25%) and nickel (8% -10%), with good ductility and toughness, can not be heat-treated to improve the hardness.
- Martensitic stainless steel: the main components include high carbon (0.1%-1.2%) and chromium (12%-18%), its mechanical properties can be improved by quenching and tempering treatment.
FAQ
Stainless steel 316 is austenitic stainless steel, its corrosion resistance, and high-temperature strength has been greatly improved due to the addition of Mo elements, high temperature resistance can reach 1200-1300 degrees, and can be used in harsh conditions.
Austenitic stainless steelhas many excellent properties that make it widely used in several fields, austenitic stainless steel has an austenitic organisation at room temperature, which gives it non-magnetic properties, high toughness and high plasticity, but low strength. This material is mainly strengthened by cold working and has good machinability. In addition, austenitic stainless steels have excellent corrosion resistance, especially in oxidising environments, and good heat resistance.
Austenitic stainless steels mainly include 304, 304L, 316, 316L etc, these materials have excellent corrosion resistance and formability and are widely used in food, medical, chemical and other fields. Among them, 304 is the most commonly used austenitic stainless steel, containing 18-20 percent chromium and 8-10 percent nickel.
When viewed under a microscope, austenitic stainless steels usually have finer and more uniform grains than ferritic stainless steels, and are brighter in color and more regular in form.
Austenitic stainless steels are known for their excellent corrosion resistance, high strength and good mechanical properties. The main components of austenitic stainless steel include high levels of chromium and nickel, which gives it excellent corrosion resistance and makes it suitable for a wide range of wet or corrosive environments. In addition, austenitic stainless steel has good ductility and formability, allowing it to be easily moulded into intricate designs, as well as good weldability and low-temperature toughness.