ASTM A814 TP 304/304L 316/316L Welded Stainless Steel Pipe is made by a machine welding or an automatic welding process, welding from one or both sides and producing full penetration welds with no addition of filler metal in the welding operation. ASTM A814 Welded Stainless Steel Pipe is used for high-temperature and general corrosive services. Pipe covers two classes of flanged and cold-bending quality cold-worked straight-beam single or double welded austenitic steel pipe Pipes of Class SW shall be single-welded with no addition of filler metal and Class DW pipes shall be double-welded with no addition of filler metal.
ASTM A814 Welded pipe sizes range from 1/8″ to 4 inch in outside diameter, Schedule covers 10, 40, 80 for wall thickness, annealed and pickled finishing.
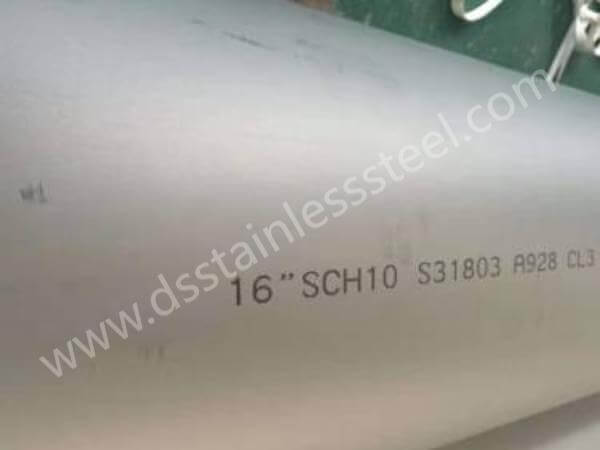
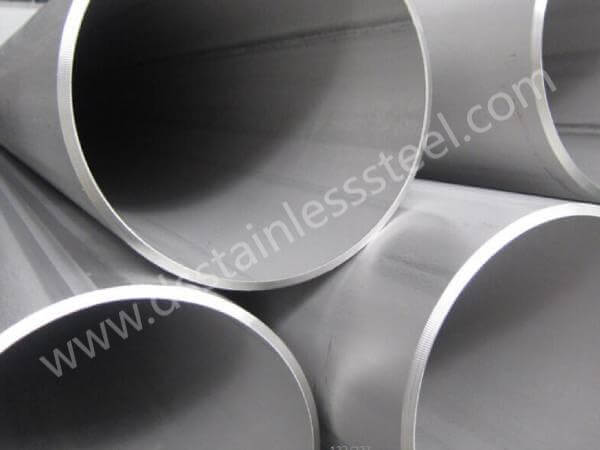
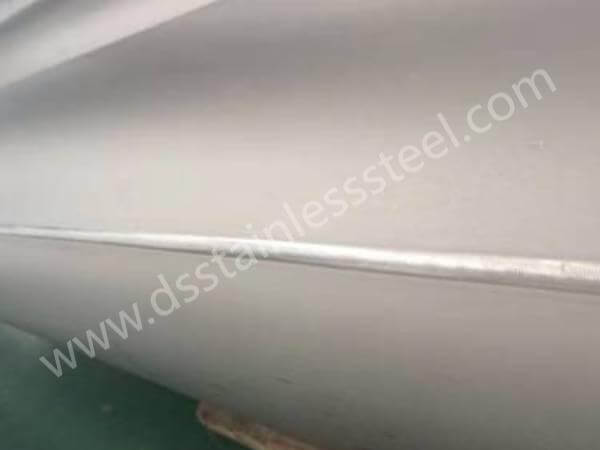
ASTM A814 Welded Stainless Steel Pipe Dimensions
NPS NO. | Outside Diameter | OD Tolerance | Schedule | Wall | |
---|---|---|---|---|---|
In. 【mm】 | In. 【mm】 | In. 【mm】 | In. 【mm】 | ||
1⁄8 | 0.405 [10.29] | +0.004 [0.10] | 10 | 0.049 [1.24] | ±0.004 [0.10] |
−0.002 [0.05] | 40 | 0.068 [1.72] | ±0.005 [0.12] | ||
80 | 0.095 [2.41] | ±0.006 [0.15] | |||
1⁄4 | 0.540 [13.72] | +0.005 [0.12] | 10 | 0.065 [1.65] | ±0.005 [0.12] |
−0.003 [0.08] | 40 | 0.088 [2.24] | ±0.006 [0.15] | ||
80 | 0.119 [3.02] | ±0.009 [0.23] | |||
3⁄8 | 0.675 [17.15] | +0.006 [0.15] | 10 | 0.065 [1.65] | ±0.005 [0.12] |
−0.004 [0.10] | 40 | 0.091 [2.31] | ±0.006 [0.15] | ||
80 | 0.126 [3.20] | ±0.010 [0.25] | |||
1⁄2 | 0.840 [ 21.34] | +0.007 [0.18] | 5 | 0.065 [1.65] | ±0.005 [0.12] |
−0.005 [0.12] | 10 | 0.083 [2.11] | ±0.006 [0.15] | ||
40 | 0.109 [2.77] | ±0.009 [0.23] | |||
80 | 0.147 [3.73] | ±0.011 [0.28] | |||
3⁄4 | 1.050 [26.67] | +0.010 [0.25] | 5 | 0.065 [1.65] | ±0.005 [0.12] |
−0.007 [0.18] | 10 | 0.083 [2.11] | ±0.006 [0.15] | ||
40 | 0.113 [2.87] | ±0.009 [0.23] | |||
80 | 0.154 [3.91] | ±0.011 [0.28] | |||
1 | 1.315 [33.40] | +0.010 [0.25] | 5 | 0.065 [1.65] | ±0.005 [0.12] |
−0.007 [0.18] | 10 | 0.109 [2.77] | ±0.009 [0.23] | ||
40 | 0.133 [3.38] | ±0.011 [0.28] | |||
80 | 0.179 [4.55] | ±0.014 [0.36] | |||
11⁄4 | 1.660 [42.16] | +0.012 [0.30] | 5 | 0.065 [1.65] | ±0.005 [0.12] |
−0.008 [0.20] | 10 | 0.109 [2.77] | ±0.009 [0.23] | ||
40 | 0.140 [3.56] | ±0.011 [0.28] | |||
80 | 0.191 [4.85] | ±0.014 [0.36] | |||
11⁄2 | 1.900 [48.26] | +0.015 [0.38] | 5 | 0.065 [1.65] | ±0.005 [0.12] |
−0.008 [0.20] | 10 | 0.109 [2.77] | ±0.009 [0.23] | ||
40 | 0.145 [3.68] | ±0.011 [0.28] | |||
80 | 0.200 [5.08] | ±0.015 [0.38] | |||
2 | 2.375 [60.33] | +0.018 [0.46] | 5 | 0.065 [1.65] | ±0.005 [0.12] |
−0.008 [0.20] | 10 | 0.109 [2.77] | ±0.009 [0.23] | ||
40 | 0.154 [3.91] | ±0.011 [0.28] | |||
80 | 0.218 [5.54] | ±0.015 [0.38] | |||
21⁄2 | 2.875 [73.03] | +0.020 [0.51] | 5 | 0.065 [1.65] | ±0.005 [0.12] |
−0.009 [0.23] | 10 | 0.120 [3.05] | ±0.010 [0.25] | ||
40 | 0.203 [5.16] | ±0.015 [0.38] | |||
80 | 0.276 [7.01] | ±0.020 [0.51] | |||
3 | 3.500 [88.90] | +0.025 [0.63] | 5 | 0.083 [2.11] | ±0.006 [0.15] |
−0.010 [0.25] | 10 | 0.120 [3.05] | ±0.010 [0.25] | ||
40 | 0.216 [5.49] | ±0.015 [0.38] | |||
80 | 0.300 [7.62] | ±0.020 [0.51] | |||
31⁄2 | 4.000 [101.6] | +0.025 [0.63] | 5 | 0.083 [2.11] | ±0.006 [0.15] |
−0.010 [0.25] | 10 | 0.120 [3.05] | ±0.010 [0.25] | ||
40 | 0.226 [5.74] | ±0.018 [0.46] | |||
80 | 0.318 [8.08] | ±0.020 [0.51] | |||
4 | 4.500 [114.3] | +0.025 [0.63] | 5 | 0.083 [2.11] | ±0.006 [0.15] |
−0.010 [0.25] | 10 | 0.120 [3.05] | ±0.010 [0.25] | ||
40 | 0.237 [6.02] | ±0.019 [0.48] | |||
80 | 0.337 [8.56] | ±0.020 [0.51] |
Permissible Variations in Dimensions
- Specified Diameter—The diameter at any point in each length of pipe shall be within the tolerance specified in Table 1.
- Alignment (Camber)—Using a 3-ft [1.0-m] straightedge placed so that both ends are in contact with the pipe, the camber shall not be more than 0.030-in. [0.8-mm].
- Thickness—The wall thickness at any point in the pipe shall be within the thickness tolerance specified in Table 3, except that for pipe in which the wall thickness exceeds 0.188-in. [4.8-mm] a weld reinforcement of up to 0.015-in. [0.38-mm] is permitted on the inside of the pipe.
ASTM A814/A814M
Standard Specification for Cold-Worked Welded Austenitic Stainless Steel Pipe
ASTM A814 Pipe Materials and Manufacture
The pipe shall be made by a machine welding or an automatic welding process, welding from one or both sides and producing full penetration welds with no addition of filler metal in the welding operation.
Weld repairs, with the addition of compatible filler metal, may be made to the weld joint in accordance with the requirements of the section on Repair by Welding of Specification A 999/A 999M.
Prior to final heat treatment of the pipe, the weld bead must be cold-worked by methods such as forging, planishing, drawing, swaging or bead rolling so as to obtain a flush condition on the inside and outside of the pipe. Undercuts shall be limited to shallow rounded depressions of less than 0.005 in. [0.127 mm] deep on either the inside or outside surface of the pipe with no encroachment of the minimum permitted wall thickness.
The pipe shall be pickled free of scale. When bright annealing is used, pickling is not necessary.
All pipes shall be furnished in the heat-treated condition. The heat-treatment procedure, except for H grades, S30815, N08367 and S 31254, shall consist of heating the pipe to a minimum temperature of 1900 °F [1040 °C] and quenching in water or rapidly cooling by other means.
All H grades and S30815 shall be furnished in the solution-treated condition. The minimum solution treating temperature for Grades TP321H, TP347H, and TP348H shall be 2000 °F [1100 °C] and for Grades TP304H and TP316H, 1900 °F [1040 °C]. The minimum temperature for S30815 shall be 1920 °F [1050 °C].
The heat-treatment procedure for S 31254 shall consist of heating the pipe to a minimum temperature of 2100 °F [1150°C] and quenching in water or rapidly cooling by other means.
The heat-treatment procedure for S31727 and S32053 shall consist of heating the pipe to a minimum temperature of 1975 to 2155 °F [1080 to 1180 °C] and quenching in water or rapidly cooling by other means.
UNS N 08367 shall be solution annealed from 2025 °F minimum followed by rapid quenching. H grades and S30815 shall have a minimum grain size of 7 or coarser when measured in accordance with Test Methods E112E112.
Chemical Composition
The steel shall conform to the chemical composition prescribed in Table 2.
When specified on the purchase order, a product analysis shall be supplied from one tube or coil of steel per heat. The product analysis tolerance of Specification A 480/A 480MA480/A480M shall apply.
Grade | Chemical composition(%) | ||||||||
---|---|---|---|---|---|---|---|---|---|
C | Si | Mn | P | S | Ni | Cr | Mo | Others | |
TP304 | 0.08Max | 0.75Max | 2.00Max | 0.045Max | 0.030Max | 8.00~16.0 | 18.0~20.0 | – | – |
TP304H | 0.04~0.10 | 0.75Max | 2.00Max | 0.045Max | 0.030Max | 8.00~16.0 | 18.0~20.0 | – | – |
TP304L | 0.035Max | 0.75Max | 2.00Max | 0.045Max | 0.030Max | 8.00~13.0 | 18.0~20.0 | – | – |
TP304N | 0.08Max | 0.75Max | 2.00Max | 0.045Max | 0.030Max | 8.00~11.0 | 18.0~20.0 | – | – |
TP304LN | 0.035Max | 0.75Max | 2.00Max | 0.045Max | 0.030Max | 8.00~11.0 | 18.0~20.0 | – | Cb+Ta 10C~1.10 |
TP304Cb | 0.08Max | 0.75Max | 2.00Max | 0.045Max | 0.030Max | 12.00~16.00 | 22.00~24.00 | 0.75Max | Cb+Ta 10C~1.10 Cu 0.75Max |
TP309S | 0.08Max | 0.75Max | 2.00Max | 0.045Max | 0.030Max | 12.00~15.00 | 22.00~24.00 | 0.75Max | – |
TP310Cb | 0.08Max | 0.75Max | 2.00Max | 0.045Max | 0.030Max | 19.00~22.00 | 24.00~26.00 | 0.75Max | Cb+Ta 10C~1.10 Cu 0.75Max |
TP310S | 0.08Max | 0.75Max | 2.00Max | 0.045Max | 0.030Max | 19.00~22.00 | 24.00~26.00 | 0.75Max | – |
TP316 | 0.08Max | 0.75Max | 2.00Max | 0.045Max | 0.030Max | 10.00~14.0 | 16.0~18.0 | 2.00~3.00 | – |
TP316H | 0.04~0.10 | 0.75Max | 2.00Max | 0.045Max | 0.030Max | 10.00~14.0 | 16.0~18.0 | 2.00~3.00 | – |
TP316L | 0.035Max | 0.75Max | 2.00Max | 0.045Max | 0.030Max | 10.00~14.0 | 16.0~18.0 | 2.00~3.00 | – |
TP316N | 0.035Max | 0.75Max | 2.00Max | 0.045Max | 0.030Max | 10.00~14.0 | 16.0~18.0 | 2.00~3.00 | N 0.10~0.16 |
TP316LN | 0.035Max | 0.75Max | 2.00Max | 0.045Max | 0.030Max | 10.00~14.0 | 16.0~18.0 | 2.00~3.00 | N 0.10~0.16 |
TP317 | 0.08Max | 0.75Max | 2.00Max | 0.045Max | 0.030Max | 11.00~14.00 | 18.0~20.0 | 3.00~4.00 | – |
TP317L | 0.035Max | 0.75Max | 2.00Max | 0.045Max | 0.030Max | 11.00~15.0 | 18.0~20.0 | 3.00~4.00 | – |
TP321 | 0.08Max | 0.75Max | 2.00Max | 0.045Max | 0.030Max | 9.00~13.0 | 17.0~20.0 | – | Ti 5C~0.70 |
TP321H | 0.04~0.10 | 0.75Max | 2.00Max | 0.045Max | 0.030Max | 9.00~13.0 | 17.0~20.0 | – | Ti 5C~0.70 |
TP347 | 0.08Max | 0.75Max | 2.00Max | 0.045Max | 0.035Max | 9.00~13.0 | 17.0~20.0 | – | Cb+Ta 10C~1.00 |
TP347H | 0.04~0.10 | 0.75Max | 2.00Max | 0.045Max | 0.035Max | 9.00~13.0 | 17.0~20.0 | – | Cb+Ta 8C~1.0 |
TP348 | 0.08Max | 0.75Max | 2.00Max | 0.045Max | 0.035Max | 9.00~13.0 | 17.0~20.0 | – | Cb+Ta 10C~1.00 |
TP348H | 0.04~0.10 | 0.75Max | 2.00Max | 0.045Max | 0.035Max | 9.00~13.0 | 17.0~20.0 | – | Ta 0.10Max Cb+Ta 8C~1.00 |
TPXM10 | 0.08Max | 1.00Max | 8.00~10.00 | 0.040Max | 0.030Max | 5.50~7.50 | 19.00~21.50 | – | N 0.15~0.40 |
TPXM11 | 0.04Max | 1.00Max | 8.00~10.00 | 0.040Max | 0.030Max | 5.50~7.50 | 19.00~21.50 | – | N 0.15~0.40 |
TPXM15 | 0.08Max | 1.50~2.00 | 2.00Max | 0.040Max | 0.030Max | 17.50~18.50 | 17.0~19.0 | – | – |
TPXM19 | 0.060Max | 1.00Max | 11.50~14.50 | 0.040Max | 0.030Max | 11.50~13.50 | 20.50~23.50 | 1.50~3.00 | N 0.20~0.40 V 0.10~0.30 Cb+Ta 0.10~0.30 |
TPXM29 | 0.080Max | 1.00Max | 11.50~14.50 | 0.060Max | 0.030Max | 2.25~3.75 | 17.0~19.0 | – | N 0.20~0.40 V 0.10~0.30 Cb+Ta 0.10~0.30 |
S31254 | 0.020Max | 0.80Max | 1.00Max | 0.030Max | 0.010Max | 17.50~18.50 | 19.50~20.50 | 6.00~6.50 | N 0.180~0.220 Cu 0.50~1.00 |
S30815 | 0.10Max | 0.80Max | 1.40~2.00 | 0.040Max | 0.030Max | 10.0~12.0 | 20.0~22.0 | – | N 0.14Max~0.20 Cu 0.03~0.08 |
Tensile Requirements
The tensile properties of the material shall conform to the requirements prescribed in Table 3.
Grade | Tensile Test MPa or N/mm2 | |
---|---|---|
Min Yield point | Tensile Strength | |
TP304 | 205 | 485Min |
TP304H | 205 | 485Min |
TP304L | 205 | 515Min |
TP304N | 205 | 515Min |
TP304LN | 205 | 515Min |
TP304Cb | 205 | 515Min |
TP309S | 205 | 515Min |
TP310Cb | 205 | 515Min |
TP310S | 205 | 515Min |
TP316 | 205 | 515Min |
TP316H | 205 | 515Min |
TP316L | 205 | 515Min |
TP316N | 205 | 515Min |
TP316LN | 205 | 515Min |
TP317 | 205 | 515Min |
TP317L | 205 | 515Min |
TP321 | 205 | 515Min |
TP321H | 205 | 515Min |
TP347 | 205 | 515Min |
TP347H | 205 | 515Min |
TP348 | 205 | 515Min |
TP348H | 205 | 515Min |
TPXM10 | 345 | 515Min |
TPXM11 | 345 | 620Min |
TPXM15 | 205 | 515Min |
TPXM19 | 380 | 690Min |
TPXM29 | 380 | 690Min |
S31254 | 300 | 650Min |
S30815 | 310 | 600Min |