We offer ASTM A376 TP 347/347H 304 321 Seamless Stainless Steel Pipe in a wide range of sizes, outside diameter from 1/2 inch to 30 inch, wall thickness have SCH5S, 10S, 40S, 80S, the average wall thickness can be offered upon requirement, we offer ASTM A376 347/347H stainless steel seamless pipe in the cold finishing manufacturing process, then heat treatment, pickling and passivation process, pipe end can be beveled end and plain end. ASTM A376 TP 347/347H Seamless Stainless Steel Pipes have excellent corrosion resistance.
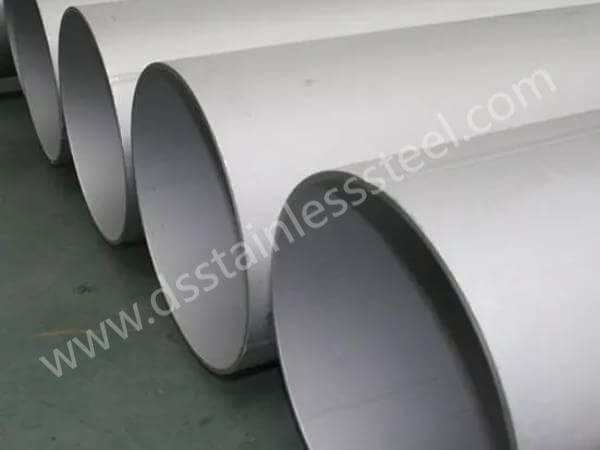
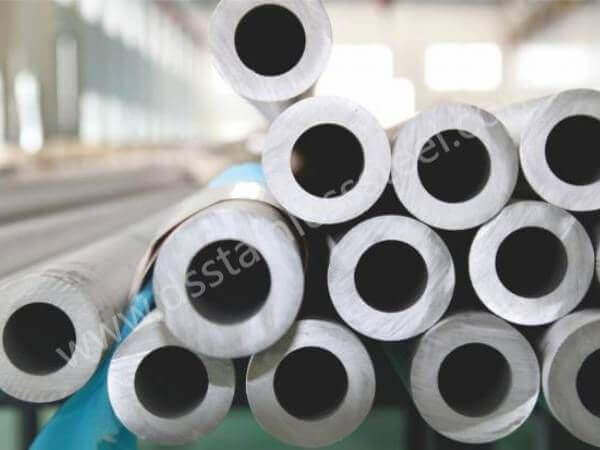
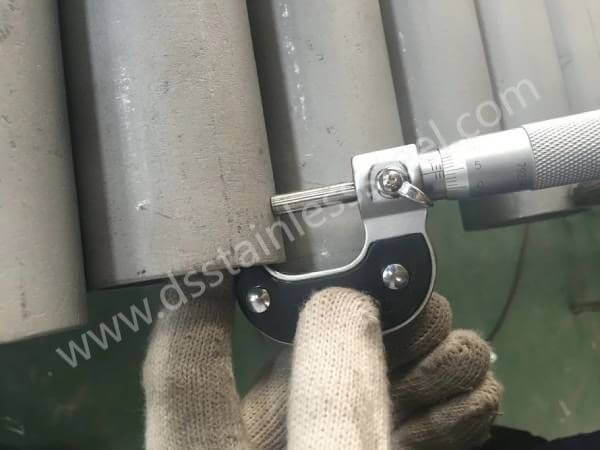
ASTM A376 TP347 Seamless Stainless Steel Pipe, ASTM A376 TP304 Seamless Pipe, ASTM A376/A312 Stainless Stel Pipe, ASTM A376 TP347H Seamless Stainless Steel Pipe, ASTM A376 High Temperature Steel Pipe, ASTM A376 TP321 Seamless Pipe, ASME SA376 347/347H 304 321 Seamless Stainless Steel Pipe
ASTM A376 TP 347/347H 304 321 Seamless Stainless Steel Pipe
Standard | ASTM A376 |
---|---|
Stainless Steel | 304, 316, 321, 347, 347H |
Pipe Type | Seamless Pipe |
Finishes | Annealed pickling, bright annealing |
Outside Diameter | 1/8 Inch To 30 Inch, NPS |
Thickness | Sch 5, Sch 5S, Sch 10S, Sch 40S, Sch 80S, Sch 160 |
Application | high-temperature central-station service |
ASTM A376/A376M
Standard Specification for Seamless Austenitic Steel Pipe for High-Temperature Service
ASTM A376/A376M covers seamless austenitic steel pipe intended for high-temperature central station service. The grades covered are five H grades and two nitrogen grades. The pipe may be either hot-finished or cold-finished, with a suitable finishing treatment.
ASTM A376 Chemical Composition
Grade | UNS Designation | Carbon | Manganes, max | Phosphoru, max | Sulfur, max | Silicon, max | Nickel | Chromium | Molybdenum | Nitrogen (A) | Others |
---|---|---|---|---|---|---|---|---|---|---|---|
TP304 | S30400 | 0.08 max | 2 | 0.045 | 0.03 | 0.75 | 8.0–11.0 | 18.0–20.0 | … | … | … |
TP304H | S30409 | 0.04–0.10 | 2 | 0.045 | 0.03 | 0.75 | 8.0–11.0 | 18.0–20.0 | … | … | … |
TP304N | S30451 | 0.08 max | 2 | 0.045 | 0.03 | 0.75 | 8.0–11.0 | 18.0–20.0 | … | 0.10–0.16 | … |
TP304LN | S30453 | 0.035 max | 2 | 0.045 | 0.03 | 0.75 | 8.0–11.0 | 18.0–20.0 | … | 0.10–0.16 | … |
TP316 | S31600 | 0.08 max | 2 | 0.045 | 0.03 | 0.75 | 11.0–14.0 | 16.0–18.0 | 2.00–3.00 | … | … |
TP316H | S31609 | 0.04–0.10 | 2 | 0.045 | 0.03 | 0.75 | 11.0–14.0 | 16.0–18.0 | 2.00–3.00 | … | … |
TP316N | S31651 | 0.08 max | 2 | 0.045 | 0.03 | 0.75 | 11.0–14.0 | 16.0–18.0 | 2.00–3.00 | 0.10–0.16 | … |
TP316LN | S31653 | 0.035 max | 2 | 0.045 | 0.03 | 0.75 | 11.0–14.0 | 16.0–18.0 | 2.00–3.00 | 0.10–0.16 | … |
TP321 | S32100 | 0.08 max | 2 | 0.045 | 0.03 | 0.75 | 9.0–13.0 | 17.0–19.0 | … | … | (B) |
TP321H | S32109 | 0.04–0.10 | 2 | 0.045 | 0.03 | 0.75 | 9.0–13.0 | 17.0–19.0 | … | … | (C) |
TP347 | S34700 | 0.08 max | 2 | 0.045 | 0.03 | 0.75 | 9.0–13.0 | 17.0–19.0 | … | … | (D) |
TP347H | S34709 | 0.04–0.10 | 2 | 0.045 | 0.03 | 0.75 | 9.0–13.0 | 17.0–19.0 | … | … | (E) |
TP348 (F) | S34800 | 0.08 max | 2 | 0.045 | 0.03 | 0.75 | 9.0–13.0 | 17.0–19.0 | … | … | Ta 0.1, Co 0.20 max, (D) |
TP348H | S34809 | 0.04–0.10 | 2 | 0.045 | 0.03 | 1 | 9.0–13.0 | 17.0–19.0 | … | … | (E) |
16-8-2H | S16800 | 0.05–0.10 | 2 | 0.045 | 0.03 | 0.75 | 7.5–9.5 | 14.5–16.5 | 1.50–2.00 | … | … |
… | S31725 | 0.030 max | 2 | 0.045 | 0.03 | 0.75 | 13.5–17.5 | 18.0–20.0 | 4.0–5.0 | 0.20 max | Cu 0.75 max |
… | S31726 | 0.030 max | 2 | 0.045 | 0.03 | 0.75 | 14.5–17.5 | 17.0–20.0 | 4.0–5.0 | 0.10–0.20 | Cu 0.75 max |
… | S34565 | 0.030 max | 5.0–7.0 | 0.03 | 0.01 | 1 | 16.0–18.0 | 23.0–25.0 | 4.0–5.0 | 0.040–0.060 | Cu 0.75 max |
(A) The method of analysis for nitrogen shall be a matter of agreement between the purchaser and manufacturer.
(B) The titanium content shall be not less than five times the carbon content and not more than 0.70%.
(C) The titanium content shall be not less than four times the carbon content and not more than 0.70%.
(D) The columbium content shall be not less than ten times the carbon content and not more than 1.10%.
(E) The columbium content shall be not less than eight times the carbon content and not more than 1.10%. (F) This grade is intended for special purpose applications.
ASTM A376 Tensile Requirements
Grade | Tensile (A) Strength, min, ksi [MPa] | Yield Strength, min, ksi [MPa] | Elongation in 2 in. or 50 mm (or 4D) min, % | |
---|---|---|---|---|
Longitudinal | Transverse | |||
TP304, TP304H, TP304LN, TP316, | 75 [515] | 30 [205] | 35 | 25 |
TP304N, TP316N, S31726 | 80 [550] | 35 [240] | 35 | 25 |
S34565 | 115 [790] | 60 [415] | 35 | 30 |
TP321, TP321H :- | ||||
≤3⁄8” | 75 [515] | 30 [205] | 35 | 25 |
>3⁄8” (B) | 70 [480] | 25 [170] | 35 | 25 |
(A) For grade TP304, NPS 8 or larger, and in schedules 140 and heavier, the required minimum tensile strength shall be 70 ksi [480 MPa].
(B) Prior to the issuance of A 376/A 376M — 88, the tensile and yield strength values were 75 [520] and 30 [210] respectively, for nominal wall greater than
3⁄8 in. [9.5 mm].
All pipes shall be furnished in the heat-treated condition unless the order specifically states that no final heat treatment shall be applied. Tensile tests, hydrostatic test, nondestructive electric tests, ultrasonic tests, eddy-current tests, tension tests, and flattening tests shall be made to conform to the requirements specified.
ASTM A376 Seamless Stainless Steel Pipe shall be free of scale and contaminating iron particles. Pickling, blasting, or surface finishing is not mandatory when pipe is bright annealed. The purchaser may request that a passivating treatment be applied.
Heat Treatment :
- Grades TP304, TP304N, TP304LN, TP316, TP316N, TP316LN, TP321, TP347, TP348, 16-8-2H, S31725, and S31726 :-
Unless otherwise stated in the order, heat treatment shall consist of heating to a minimum temperature of 1900°F [1040°C] and quenching in water or rapidly cooling by other means. - Grades TP304H, TP316H, TP321H, TP347H, TP348H, and 16-8-2H :-
If cold working is involved in processing, the minimum solution-treating temperature for Grades TP321H, TP347H, and TP348H shall be 2000°F [1100°C], for Grades TP304H and TP316H, 1900°F [1040°C], and for Grade 16-8-2H, 1800°F [980°C].
If the material is hot-rolled, the minimum solution-treating temperatures for Grades TP321H, TP347H, and TP348H shall be 1925°F [1050°C], for Grades TP304H and TP316H, 1900°F [1040°C], and for Grade 16-8-2H, 1800°F [980°C]. - Grade S34565 :-
Heat treatment shall consist of heating to a temperature in the range of 2050°F [1120°C] minimum and 2140°F [1170°C] maximum, and quenching in water or rapidly cooling by other means. - A solution annealing temperature above 1950°F [1065°C] may impair the resistance to intergranular corrosion after subsequent exposure to sensitizing conditions in TP321, TP321H, TP347, TP347H, TP348, and TP348H. When specified by the purchaser, a lower temperature stabilization or re-solution anneal shall be used subsequent to the initial high-temperature solution anneal.
The pipe shall be free of scale and contaminating iron particles. Pickling, blasting, or surface finishing is not mandatory when pipe is bright annealed. The purchaser may request that a passivating treatment be applied.
Hydrostatic or Non-destructive Electric Test :
Each pipe shall be subjected to the Non-destructive Electric Test or the Hydrostatic Test. Unless specified by the purchaser, either test may be used at the option of the producer.
Hydrostatic Test :
The test pressure or stress shall be determined using the following equation:
P = 2St⁄D or S= PD ⁄ 2t
Where: P = hydrostatic test pressure in psi [MPa],
S = pipe wall stress in psi or [MPa],
t = specified wall thickness, nominal wall thickness according to specified ANSI schedule number, or 1.143 times the specified minimum wall thickness, in. [mm]
D = specified outside diameter, outside diameter corresponding to specified ANSI pipe size, or outside diameter calculated by adding 2t (as defined above) to the specified inside diameter, in. [mm].
The hydrostatic test pressure determined by Eq 3 shall be rounded to the nearest 50 psi [0.5 MPa] for pressures below 1000 psi [7 MPa], and to the nearest 100 psi [1 MPa] for pressures 1000 psi [7 MPa] and above.
The test pressure shall be held for a minimum of 5 s. For welded pipe, the test pressure shall be held for a time sufficient to permit the entire length of the welded seam to be inspected.
Non-destructive Examination :
- The ultrasonic testing (UT)
- The eddy-current testing (ET)
Mechanical Tests Required :
- Transverse or Longitudinal Tension Test.
- Flattening Test.
Supplementary Tests :
- Transverse Tension Tests.
- Flattening Test.
- Etching Tests.
- Ultrasonic Test.
- Hot Ductility Test for Indicating Weldability.
- Intergranular Corrosion Test.