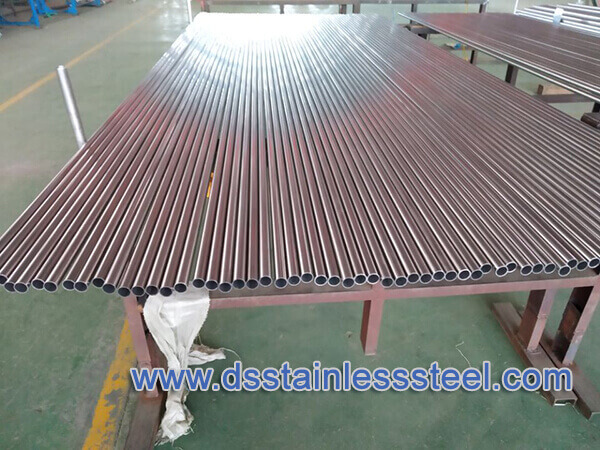
ASTM A249 TP304 stainless steel tubes are designed for pressure vessel systems including boiler, super-heater, heat exchanger and condenser, ASTM A249 standard specifies the manufacturing, grades, tolerance, tests, and other conditions for welded tubes, we produce ASTM A249 tubes using the TIG welding and plasma welding processes from flat-rolled strips, ASTM A249 304 is the most used stainless steel grade with excellent corrosion resistance and properties.
The A249 stainless steel tubing sizes and thicknesses usually furnished are 1/8 in. [3.2 mm] in inside diameter to 12 in. [304.8 mm] in outside diameter and 0.015 to 0.320 in. [0.4 to 8.1 mm], inclusive, in wall thickness. Tubing having other dimensions may be furnished. The wall thickness of the tube can be Average Wall (A.W) and Minimum Wall (M.W.), heavy wall tubes are available.
ASTM A249 TP304 Stainless Steel Tube Specifications
Standard | ASTM A249 |
---|---|
Material | TP304 |
Tube Type | Welded Tube |
Finishes | Annealing Pickling, Bright Annealing |
Outside Diameter | 6 Up To 304.8 Mm |
Thickness | 0.5 Up To 6 Mm |
Application | Heat Exchanger System |
ASTM A249 TP304 Chemical Composition
Grade | C | Si | Mn | Cr | Ni | S | P | Fe |
---|---|---|---|---|---|---|---|---|
TP304 | 0,08 | 1,0 | 2 | 18 – 20 | 8 – 11 | 0,03 | 0,045 | Bal. |
ASTM A249 TP304 Mechanical Properties
Grade | Tensile Strength (Mpa) | Yield Point (Mpa) | Elongation (%) |
---|---|---|---|
TP304 | 515 | 205 | 35 |
ASTM A249 Tubing Manufacturing
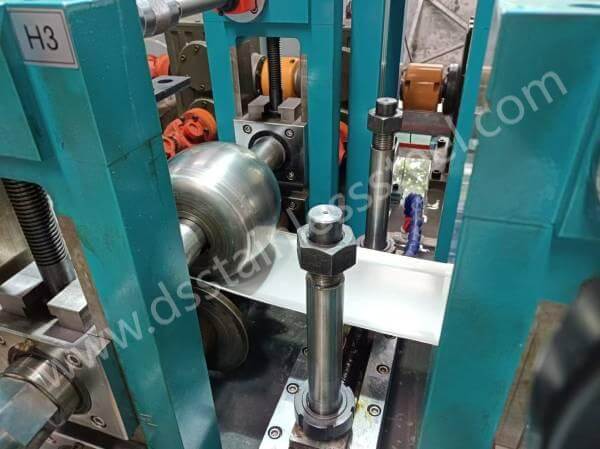
ASTM A249 specification nominal-wall-thickness welded tubes and heavily cold-worked welded tubes made from austenitic steels, with various grades intended for such use as boiler, superheater, heat exchanger, or condenser tubes, for welded tubes, dual standard ASTM A249/A269 is used for heat exchanger tubes.
Strip
Quality welded tube is made from the quality strip, quality requires fine edge conditions and uniform wall.
TIG Welding
We use the tungsten inert gas (TIG) welding method, TIG is an automatic process of welding two edges of a strip and forming a tubular shape, this process achieves a precise joint between the bead and base metal.
Related: TIG Welding Stainless Steel Tube
Cold Working
After welding, the inside and outside of the tube must be forged to achieve high integrity, then have correct properties, and also possess precise dimensions.
Heat Treatment
Annealing is a very important process, tubes are heated to the required solution temperature and rapidly cooled, ASTM A249 TP304 stainless steel requires a minimum solution temperature is 1040 degrees, it can restabilize microstructure to ensure premium properties.
Bright Annealing Option
Bright annealing welded tube is often required, The tube passes through in closed furnace, inserting hydrogen gas to isolate the surrounding atmosphere, finally forming a passive oxide film on the surface.
Related: Bright Annealing Tubing
ASTM A249 TP304 Stainless Steel Tubes Sizes
We offer large sizes and dimensions for heat exchanger tubes, common sizes are provided below, and others are available.
Outside Diameter: 12.7, 15.88, 19.05, 25.4, 31.8, 38.1, 45, 50.8, 60.3, 76.2 mm
Wall Thickness: 0.51, 0.71, 0.89, 1.0, 1.25, 1.65, 2.11, 2.77, 3.05 mm.
ASTM A249 Material Chemical Composition
Grade | C, %, Max | Mn, %, Max | P, %, Max | S, %, Max | Si, %, Max | Cr | Ni | Mo | Ti | Nb, %, | N B |
---|---|---|---|---|---|---|---|---|---|---|---|
TP304 | 0.08 | 2.00 | 0.045 | 0.030 | 1.00 | 18.0-20.0 | 8.0-11.0 | … | … | … . | … |
TP304H | 0.04-0.10 | 2.00 | 0.045 | 0.030 | 1.00 | 18.0-20.0 | 8.0-11.0 | … | … | … | … |
TP304L | 0.035 | 2.00 | 0.045 | 0.030 | 1.00 | 18.0-20.0 | 8.0-13.0 | … | … | … | … |
TP310S | 0.08 | 2.00 | 0.045 | 0.030 | 1.00 | 24.0-26.0 | 19.0-22.0 | 0.75 | |||
TP316 | 0.08 | 2.00 | 0.045 | 0.030 | 1.00 | 16.0-18.0 | 11.0-14.0 | 2.00-3.00 | … | … | … |
TP316L | 0.035 | 2.00 | 0.045 | 0.030 | 1.00 | 16.0-18.0 | 10.0-14.0 | 2.00-3.00 | … | … | … |
TP316H | 0.04-0.10 | 2.00 | 0.045 | 0.030 | 1.00 | 16.0-18.0 | 11.0-14.0 | 2.00-3.00 | … | … | … |
TP316Ti | 0.08 | 2.00 | 0.045 | 0.030 | 0.75 | 16.0-18.0 | 10.0-14.0 | 2.00-3.00 | 5x(C+N)-0.70 | … | 0.10 |
TP321 | 0.08 | 2.00 | 0.045 | 0.030 | 1.00 | 17.0-19.0 | 9.0-12.0 | … | 5C-0.70 | … | 0.10 |
TP321H | 0.04-0.10 | 2.00 | 0.045 | 0.030 | 1.00 | 17.0-19.0 | 9.0-12.0 | … | 4C-0.60 | … | … |
TP347 | 0.08 | 2.00 | 0.045 | 0.030 | 1.00 | 17.0-19.0 | 9.0-13.0 | … | 10xC-1.00 | ||
TP347H | 0.04-0.10 | 2.00 | 0.045 | 0.030 | 1.00 | 17.0-19.0 | 9.0-13.0 | … | … | 8xC-1.00 | … |
ASTM A249 Material Mechanical Properties
Grade | UNS | Yield Strength | Tensile Strength | Elongation In 2 In. Or 50 Mm | Hardness, Max | Hardness, Max |
---|---|---|---|---|---|---|
Designation | Min Ksi [MPa] | Min Ksi [MPa] | Min, %A, B | Rockwell | Brinell/Vickers | |
TP304 | S30400 | 30 [205] | 75 [515] | 35 | 90HB | 192HBW/200Hv |
TP304L | S30403 | 25 [170] | 70 [485] | 35 | 90HB | 192HBW/200Hv |
TP304H | S30409 | 30 [205] | 75 [515] | 35 | 90HB | 192HBW/200Hv |
TP304N | S30415 | 35 [240] | 80 [550] | 35 | 90HB | 192HBW/200Hv |
TP310S | S31008 | 30 [205] | 75 [515] | 35 | 90HB | 192HBW/200Hv |
TP310H | S31009 | 30 [205] | 75 [515] | 35 | 90HB | 192HBW/200Hv |
TP316 | S31600 | 30 [205] | 75 [515] | 35 | 90HB | 192HBW/200Hv |
TP316L | S31603 | 25 [170] | 70 [485] | 35 | 90HB | 192HBW/200Hv |
TP316H | S31609 | 30 [205] | 75 [515] | 35 | 90HB | 192HBW/200Hv |
TP316Ti | S31635 | 30 [205] | 75 [515] | 35 | 90HB | 192HBW/200Hv |
TP317 | S31700 | 30 [205] | 75 [515] | 34 | 90HB | 192HBW/200Hv |
TP317L | S31703 | 30 [205] | 75 [515] | 35 | 90HB | 192HBW/200Hv |
TP321 | S32100 | 30 [205] | 75 [515] | 35 | 90HB | 192HBW/200Hv |
TP321H | S32109 | 30 [205] | 75 [515] | 35 | 90HB | 192HBW/200Hv |
TP347 | S34700 | 30 [205] | 75 [515] | 35 | 90HB | 192HBW/200Hv |
TP347H | S34709 | 30 [205] | 75 [515] | 35 | 90HB | 192HBW/200Hv |
ASTM A249 Material Available
Grades
TP 201, TP201LN, TP202, TPXM-19, TPXM-29, TP301, TP304L, TP304H, TP304N, TP304LN, TP305, TP309S, TP309H, TP309Cb, TP309HCb, TP310S, TP310H, TP310Cb, TP316, TP316L, TP316H, TP316N, TP316LN, TP317, TP317L, TP321, TP321H, TP347, TP347H, TP348, TP348H, TPXM-15, Alloy 20, 800, 800H.
UNS
UNS S20100, S20153, S20910, S24000, S30400, S30403, S30409, S30415, S30451, S30453, S30500, S30615, S30815, S30908, S30909, S30601, S30940, S30941, S31008, S31009, S31040, S31041, S31050, S31254, S31266, S31277, S31600, S31603, S31609, S31651, S31653, S31655, S31700, S31703, S31725, S31726, S31727, S32050, S32053, S32100, S32109, S32615, S32654, S33228, S34565, S34700, S34709, S34800, S34809, S35045, S38100, S38815, N08020, N08367, N08800, N08810, N08811, N08926, N08904
Grades TP304H, TP309H, TP309HCb, TP310H, TP310HCb, TP316H, TP321H, TP347H, and TP348H are modifications of Grades TP304, TP309S, TP309Cb, TP310S, TP310Cb, TP316, TP321, TP347, and TP348, and are intended for high-temperature service such as for superheaters and reheaters.
Quality Control System
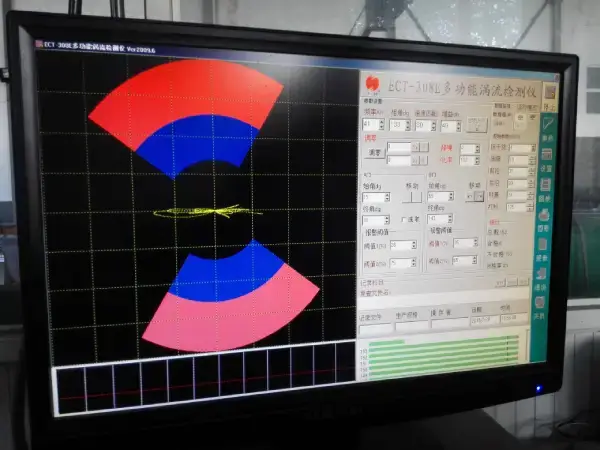
Eddy Current Test
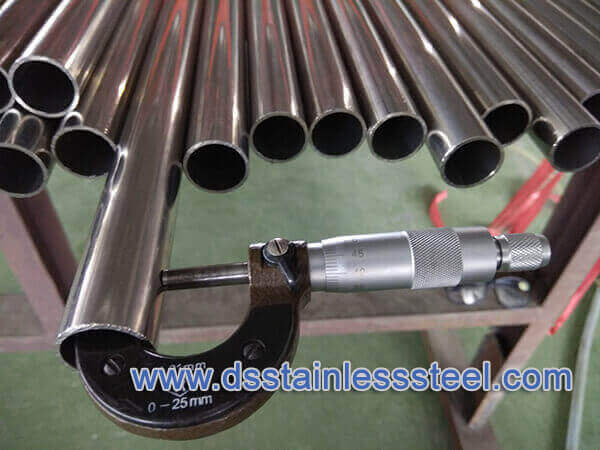
Dimensional Measurements
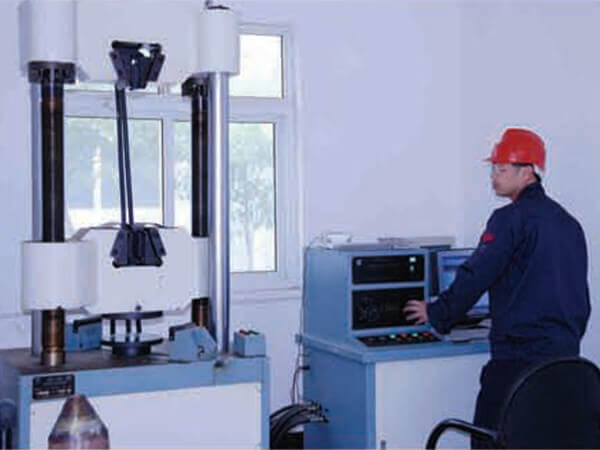
Mechanical Properties
Dimensional Inspection
All the tubes should meet to requirements of ASTM A249 specification, including tolerance of the tube outside diameter (OD), wall thickness, and length, and minimum wall thickness tube is available.
ASTM A249 Tolerances
Dimensional tolerances other than wall thickness tolerances shall be in accordance with Specification A1016/ A1016M. Wall thickness tolerances shall be +/-10 % of the nominal wall for all tubing sizes.
The wall thickness of the weld shall not exceed the wall thickness measured 90° from the weld by more than 6 % of the specified wall thickness or 0.004 in. [0.1 mm], whichever is greater.
Specified Outside Diameter, In. [Mm] | OD, Over, In. [Mm] | OD, Under, In. [Mm] | Wall Thickness | Length, In. [Mm] |
---|---|---|---|---|
Under 1 [25] | 0.004 [0.1] | 0.004 [0.11] | +/-10.0% | +1/8″ (3.18) – 0 |
1 To 11⁄2 [25 To 40], Incl | 0.006 [0.15] | 0.006 [0.15] | +/-10.0% | +1/8″ (3.18) – 0 |
Over 11⁄2 To 2 [40 To 50], Excl | 0.008 [0.2] | 0.008 [0.2] | +/-10.0% | +1/8″ (3.18) – 0 |
2 To 21⁄2 [50 To 65], Excl | 0.010 [0.25] | 0.010 [0.25] | +/-10.0% | +3/16″ [5] – 0 |
21⁄2 To 3 [65 To 75], Excl | 0.012 [0.3] | 0.012 [0.3] | +/-10.0% | +3/16″ [5] – 0 |
3 To 4 [75 To 100], Incl | 0.015 [0.38] | 0.015 [0.38] | +/-10.0% | +3/16″ [5] – 0 |
Over 4 To 71⁄2 [100 To 200], Incl | 0.015 [0.38] | 0.025 [0.64] | +/-10.0% | +3/16″ [5] – 0 |
Over 71⁄2 To 9 [200 To 225], Incl | 0.015 [0.38] | 0.045 [1.14] | +/-10.0% | +3/16″ [5] – 0 |
Mechanical Tests
There are destructive tests are performed on tube samples these tests have tests flattening test, flange test, and reverse bend test.
Hardness Test
ASTM A249 TP304 requires hardness in Rockwell B90 maximum.
Corrosion Tests (Optional)
ASTM A249 specification requires corrosion testing in SUPPLEMENTARY REQUIREMENTS, the purchaser should indicate the test when it is needed, intergranular corrosion and weld decay tests are considered widely to be a reliable corrosion test.
The ASTM A249-S7 weld decay test is considered widely to be a reliable corrosion test, but, in reality, the acid used in the test applies to less than 1 percent of real-life operational environments. Other tests, such as ASTM A262 practices A & E, may be far more practical for testing general corrosion.
Referenced Documents
- A262 Practices for Detecting Susceptibility to Intergranular Attack in Austenitic Stainless Steels
- A480/A480M Specification for General Requirements for Flat-Rolled Stainless and Heat-Resisting Steel Plate, Sheet, and Strip
- A1016/A1016M Specification for General Requirements for Ferritic Alloy Steel, Austenitic Alloy Steel, and Stainless Steel Tubes
- E112 Test Methods for Determining Average Grain Size
- E213 Practice for Ultrasonic Testing of Metal Pipe and Tubing
- E273 Practice for Ultrasonic Testing of the Weld Zone of Welded Pipe and Tubing
- E527 Practice for Numbering Metals and Alloys in the Unified Numbering System (UNS)
- 2.2 ASME Boiler and Pressure Vessel Code: Section VIII
- SAE J1086 Practice for Numbering Metals and Alloys (UNS)