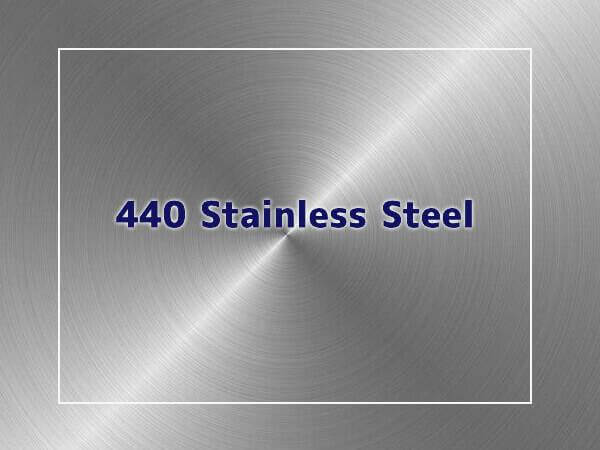
440 steel is a series of high-carbon martensitic stainless steels, including grades 440A, 440B, and 440C type, these grades have excellent hardness and wear resistance and are commonly used in the production of high-performance knives and cutting tools.
440C stainless steel is a high-carbon martensitic stainless steel, high carbon content in 440C provides high strength, moderate corrosion resistance, good hardness, and wear resistance. these characteristics make 440C particularly suited to such applications as ball bearings and valve parts, it has the highest hardness among stainless steel.
440A and 440B are the same composition as 440C except for slightly lower carbon contents (0.60 – 0.75% and 0.75 – 0.95% respectively); these have lower attainable hardnesses but slightly higher corrosion resistances. Although all three versions of this grade are standard, in practice 440C is more available than the A or B variants.
440 Stainless Steel Chemical Composition
Grade | C | Mn | Si | P | S | Cr | Mo |
---|---|---|---|---|---|---|---|
440A | 0.65- 0.75 | 1.00 | 1.00 | 0.040 | 0.030 | 16.00- 18.00 | 0.75 |
440B | 0.75- 0.95 | 1.00 | 1.00 | 0.040 | 0.030 | 16.00- 18.00 | 0.75 |
440C | 0.95- 1.20 | 1.00 | 1.00 | 0.040 | 0.030 | 16.00- 18.00 | 0.75 |
* Maximum, unless range is indicated
These properties are specified for bar products in ASTM A276. Similar but not necessarily identical properties are specified for other products such as wire and forgings in their respective specifications. These grades are not normally available in flat rolled or fluid products.
440 Stainless Steel Mechanical Properties
Grade (UNS) | Tensile Strength (MPa) ≥ | Yield Strength, 0.2%, ≥ (MPa) | Elongation in 50 mm (%) ≥ | Hardness | Product & Condition |
---|---|---|---|---|---|
440A (S44002) | 725 | 415 | 20 | 95 HRB | Annealed bar |
1790 | 1650 | 5 | 20 | Bars tempered at 315 °C | |
≤ 965 | Annealed wire, cold finished | ||||
440B (S44003) | 740 | 425 | 18 | 96 HRB | Annealed bar |
1930 | 1860 | 3 | 15 | Bars tempered at 315 °C | |
≤ 965 | Annealed wire, cold finished | ||||
440C (S44004) | 760 | 450 | 14 | 97 HRB | Annealed bar |
1970 | 1900 | 2 | 10 | Bars tempered at 315 °C | |
≤ 965 | Annealed wire, cold finished |
440C Stainless Steel Physical Properties
Grade | Density (kg/m3) | Elastic Modulus (GPa) | Mean Coefficient of Thermal Expansion (mm/m/°C) | Thermal Conductivity(W/m.K) | Specific Heat 0-100°C (J/kg.K) | Electrical Resistivity (nW.m) | |||
---|---|---|---|---|---|---|---|---|---|
0-100°C | 0-200°C | 0-600°C | at 100°C | at 500°C | |||||
440 C | 7650 | 200 | 10.1 | 10.3 | 11.7 | 24.2 | – | 460 | 600 |
Grade Specification Comparison
Grade | UNS No | Euronorm | Swedish SS | Japanese JIS | |
---|---|---|---|---|---|
Steel No. | Name | ||||
440A | S44002 | – | – | SUS 440A | |
440B | S44003 | 1.4112 | X90CrMoV18 | SUS 440B | |
440C | S44004 | 1.4125 | X105CrMo17 | – | SUS 440C |
These comparisons are approximate only. The list is intended as a comparison of functionally similar materials not as a schedule of contractual equivalents. If exact equivalents are needed original specifications must be consulted. |
440 Stainless Steel Properties and Types
The 440 family of stainless steels is most typically offered in long forms—bars, wires, billets, coils, and tubes are the most common, but there may be others. These raw forms are the most conducive to metalworking with 440 steel.
440 steel refers to four types of steel: 440A, 440B, 440C and 440F steel, which only differ based on the level of carbon in their composition. All types of 440 steel are popular choices, but 440C steel is the most popular of the four, as it has the highest hardness.
- 440A – With the least amount of carbon among the four types, this makes 440A stainless the most stain-resistant. It is the most ideal for diving and saltwater applications that require superior corrosion resistance.
- 440B. The 440B grade of stainless steel is ideal for crafting blades in areas when they need higher toughness than 440A and higher stain resistance than 440C, such as wet knives for cooking.
- 440C. With the greatest amount of carbon out of the 440 variants, this is considered to be the strongest and most desirable steel for knife making—especially over type 440A (except in aquatic conditions).
- 440F. When talking about the 440 stainless grades, 440F often remains unmentioned. 440F is a free-machining variant of 440C. The popularity of 440c led to the development of this variant that works better for machining but is nearly the same composition.
All 440 steels are hardenable, meaning they gain additional strength via heat treatment, and they are considered high-carbon alloy steel. When strengthened using this process, 440 steels are the hardest of all the stainless steels, making them both abrasion-resistant as well as corrosion-resistant. When in its soft “annealed” state, 440 steel is easily worked, machined, and manipulated into shape,
Corrosion Resistance
Good resistance to the atmosphere, freshwater, foods, alkalies and mild acids. Best resistance in the hardened and tempered and passivated condition. A smooth polished surface also assists. The corrosion resistance of Grade 440C is close to that of grade 304 in many environments. Consult Atlas Technical Assistance for specific environmental recommendations.
Heat Resistance
Not recommended for use in temperatures above the relevant tempering temperature, because of reduction in mechanical properties by over-tempering.
Heat Treatment
Annealing Full anneal – 840-870°C, slow furnace cool to about 600°C and then air cool. Sub-critical Annealing – 735-760°C and slow furnace cool.
Hardening
Heat to 1010-1065°C, followed by quenching in warm oil or air. Oil quenching is necessary for heavy sections. Immediately temper at 150- 370°C to obtain the hardness values and mechanical properties as indicated in the accompanying table. Best corrosion resistance is when tempered below 425°C. Tempering in the range 425- 565°C is to be avoided because of reduced impact resistance and corrosion resistance.
Tempering in the range 600-675°C results in lower hardness – the product becomes machinable.
Maximum achievable hardnesses are approximately HRC56 for Grade 440A, HRC58 for 440B and HRC60 for 440C.
Welding
Welding is seldom carried out because of the grades’ high hardenability. If welding is necessary pre-heat at 250°C and follow welding with a full anneal. Grade 420 filler will give a high hardness weld (although not as high as the 440C), but 309 or 310 will produce soft welds with higher ductility.
Machining
In the annealed condition this grade is relatively easily machined; approximately the same as for high-speed steel. Chips are tough and stringy so chip breakers are important. If these grades are hardened machining becomes more difficult and probably impossible.
Applications
AISI 440 steel is used for the manufacture of bearing parts that operate in corrosive environments, as well as for the manufacture of high-quality tools (medical scalpels, scissors and blades, surgical and dental instruments), molds, springs, cutlery, valves and valve components, cams, gears, shafts, ball bearings, nozzles, and measuring tools.
440 Stainless Steel Forms
Is 440 Stainless Steel Magnetic?
440 stainless steel is magnetic, it belongs to the martensitic stainless steel family, and this type of stainless steel is usually magnetic. Specifically, 440 stainless steel is magnetic when it is not specially treated, which means that it can be attracted to iron absorption stones. The magnetic properties of this stainless steel make it unique in a number of applications, such as in the manufacture of products that require magnetic retention. In addition, 440 stainless steel is also known for its high hardness, good corrosion and wear resistance, which makes it widely used in applications such as knives and bearings that require high strength and durability.
Is 440 Stainless Steel Good for Knives?
440 Stainless Steel is a high-quality stainless steel material that is widely used in the manufacture of knives. 440 stainless steel has high hardness and good wear resistance, which makes it an ideal material for making knives.
- High hardness and wear resistance: 440 stainless steel can reach a hardness of 58-62HRC after appropriate heat treatment, which allows knives to have excellent cutting performance and wear resistance, and can cope with the cutting needs of various hard materials.
- Good corrosion resistance: 440 stainless steel contains a high proportion of chromium and molybdenum elements, which allows 440 good corrosion resistance and oxidation resistance. Even in wet or corrosive environments, it maintains the sharpness and longevity of the cutter.
- Excellent Toughness: 440 stainless steel is tough while maintaining high hardness. This means that when subjected to impact or pressure, the tool is less likely to break or deform, improving the safety of use.
- Easy to Machine: 440 stainless steel has good machinability and can be shaped by forging, turning and milling. At the same time, its surface is easy to polish and grind, making the appearance of the tool more beautiful.
- Wide applicability: 440 stainless steel knives are suitable for many occasions, such as kitchen cooking, outdoor adventure, industrial production and so on. Its excellent hardness and wear resistance make the knives able to cope with various challenges.
- Long service life: Thanks to its excellent corrosion and oxidation resistance, 440 stainless steel knives have a long service life under normal conditions of use. This not only reduces the frequency of replacement but also saves costs.
- Easy maintenance: 440 stainless steel knives are easy to clean and maintain, simply rinse with water and wipe dry. In addition, regular maintenance can be carried out using specialized tool cleaners to extend the service life.
304 vs 440 stainless steel
There is a significant difference between 440 stainless steel and 304 stainless steel in chemical composition. 440 stainless steel contains a high amount of carbon and belongs to martensitic stainless steel with high hardness; while 304 stainless steel is an austenitic stainless steel containing 18% chromium and 8% nickel, which has good corrosion resistance and toughness.
In terms of corrosion resistance, 304 stainless steel shows better corrosion resistance due to its higher chromium and nickel content, able to resist the corrosion of most chemicals; while 440 stainless steel has relatively poor corrosion resistance, especially in the chloride environment prone to pitting.
Mechanical properties, 304 stainless steel has good strength and hardness, suitable for applications requiring high strength; while 440 stainless steel after appropriate heat treatment, has very high hardness, commonly used in the manufacture of high-hardness tools and knives.
In terms of magnetism, 304 stainless steel is a non-magnetic material and will not be attracted by magnets; while 440 stainless steel is magnetic and can be attracted by magnets.
Processing performance, 304 stainless steel has good plasticity and machinability, easy to form and process; while 440 stainless steel may produce work hardening in the process, requiring complex softening treatment.
In terms of applications, 304 stainless steel is widely used in food production equipment, chemical equipment, medical equipment and other fields with high hygiene requirements; while 440 stainless steel is used to manufacture high-hardness tools and knives, such as razor blades and scalpels.
316 vs 440 stainless steel
440 stainless steel is a high-carbon, high-chromium stainless steel, while 316 stainless steel contains molybdenum for better corrosion resistance.
The chemical composition of 440 stainless steel mainly includes elements carbon, chromium, and molybdenum, which provide high hardness and wear resistance. 316 stainless steel, on the other hand, containing molybdenum and nickel improves its corrosion resistance, especially to pitting and crevice corrosion in environments containing chlorides.
In terms of performance, 440 stainless steel is suitable for applications requiring high loads and high wear resistance, such as high-speed rotating equipment and high-precision machine tools, due to its high hardness and wear resistance. On the other hand, 316 stainless steel is widely used in strong corrosive environments such as marine environments and the chemical industry due to its excellent corrosion resistance, making it one of the preferred materials in these fields.
Finally, 440 stainless steel and 316 stainless steel in the field of application also have a significant difference. 440 stainless steel is suitable for the manufacture of parts that require high hardness and wear resistance, while 316 stainless steel is suitable for use in corrosive environments, such as marine engineering, and chemical equipment.