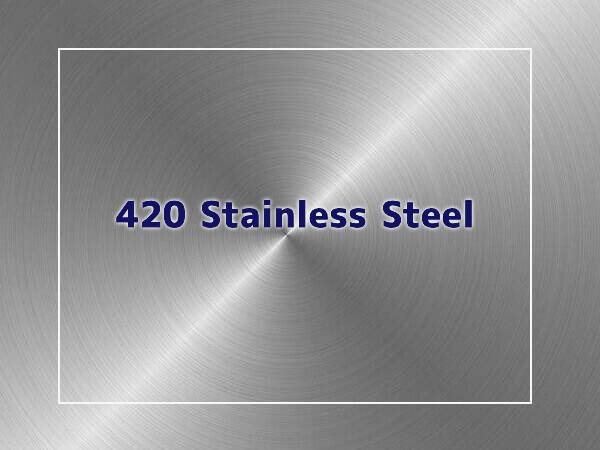
420 stainless steel is a hardenable martensitic stainless steel that contains a minimum of 12% chromium, which provides good corrosion resistance properties, Its best corrosion resistance is achieved when the metal is hardened and surface ground or polished. 420 grade has a higher carbon content than is designed to enhance strength and hardness characteristics, however, the corrosion resistance of 420 stainless steel is not as good as the common austenitic grades.
420 stainless steel has good ductility in the annealed condition but can be hardened to a minimum Rockwell hardness of 50 HRC, which is the highest hardness of the 12% chromium grades, the typical application is for knives. 420 stainless steel is magnetic due to its microstructure of martensitic.
The hardness of 420 stainless steel: Rockwell HRB 96 max.
420 stainless steel heat treatment: Heat to 1500-1650°F (816-899°C), cool slowly
420 stainless steel melting point: 2649 – 2750°F (1454 – 1510°C)
420 Stainless Steel Chemical Composition
The chemical composition of 420 stainless steel contains 12–14% chromium (Cr) and iron, high carbon content (min 0.15%), and less nickel content (0.75% Max).
ASTM | AISI (UNS) | C, | Si, Max | Mn, Max | P, Max | S, Max | Cr | Ni, Max | Mo, Max | Iron |
---|---|---|---|---|---|---|---|---|---|---|
ASTM A240 420 | SS 420 (UNS S42000) | 0.15, min | 1.00 | 1.00 | 0.040 | 0.030 | 12.0-14.0 | 0.75 | 0.50 | Bal. |
ASTM A276 420 | SS 420 (UNS S42000) | 0.15, min | 1.00 | 1.00 | 0.040 | 0.030 | 12.0-14.0 | – | – | Bal. |
EN10088-2 1.4028 | 0.26-0.35 | 1.00 | 1.50 | 0.040 | 0.015 | 12.0-14.0 | – | – | Bal. | |
EN10088-2 1.4021 | 0.16-0.25 | 1.00 | 1.50 | 0.040 | 0.015 | 12.0-14.0 | – | Bal |
420 Stainless Steel Mechanical Properties
Tensile Strength, min (MPa) | Yield Strength 0.2% Proof (MPa) | Elongation (% in 50mm) | Hardness Brinell (HRB), max |
---|---|---|---|
690 | 345 | 15 | 96 |
420 Stainless Steel Physical Properties
Physical Properties | Value |
---|---|
Density, g/cm3 (lb/in.3) | 7.8 (0.28) |
Melting point, °C (°F) | 1450-1510 (2650-2750) |
Specific heat capacity, J/kg·K (Btu/lb·°F) | 460 (0.11) at 0-100 °C (32 to 212 °F) |
Electrical resistivity, μΩ·m | 0.55 at 20 °C |
Elastic modulus (Modulus of elasticity), GPa (106 psi) | 200 (29) |
Thermal conductivity, W/m·K (Btu/ft·h·°F) | 24.9 (14.4), at 100 °C (212 °F) |
Coefficient of thermal expansion, μm/m·°C (μin./in. ·°F) | 10.3 (5.7), at 0-100 °C (32-212 °F) |
10.8 (6.0), at 0-315 °C (32-600 °F) | |
11.7 (6.5), at 0-538 °C (32-1000 °F) |
420 Stainless Steel Equivalent
EU EN | USA – | Germany DIN,WNr | Japan JIS | France AFNOR | England BS | China GB | Sweden SS | Poland PN | Czechia CSN | Russia GOST |
---|---|---|---|---|---|---|---|---|---|---|
EU EN | USA – | Germany DIN,WNr | Japan JIS | France AFNOR | England BS | China GB | Sweden SS | Poland PN | Czechia CSN | Russia GOST |
X20Cr13 (1.4021) | 420/S42010 | X20Cr13 | SUS420J1 | X20Cr13Z20C13 | 420S29420S37 | 2Cr13X20Cr13 | 2303 | 2H13 | 17022 | 20KH13 |
Features
Grade 420 stainless steel is a high-carbon steel with a minimum chromium content of 12%. Like other martensitic stainless steels, grade 420 can also be hardened through heat treatment. Martensitic stainless steels are ones with high hardness and high carbon content. These steels are generally fabricated using methods that require hardening and tempering treatments. The operating conditions of martensitic steels are affected by loss of material strength at high temperatures and a decrease in ductility at negative temperatures. AISI 420 steel provides both outstanding corrosion resistance and exceptional wear resistance.
- High hardness: stainless steel 420 has a high degree of hardness, which can be obtained through heat treatment. This makes it widely used in the manufacture of knives, surgical instruments and industrial parts.
- Good corrosion resistance: 420 SS has good corrosion resistance and can resist many chemicals, including some acids and salt solutions. However, compared with other stainless steels, the corrosion resistance of 420 stainless steel is relatively low.
- Easy machining: 420 grade has good plasticity and machinability before heat treatment, easy to forge, cold drawing, milling and cutting and other machining operations.
- Excellent grinding properties: 420 has good grinding properties, so it can be used in applications such as the manufacture of knives and blades that need to achieve a sharp cutting edge.
- Moderate strength and wear resistance: Type 420 has moderate tensile strength and wear resistance, making it widely used in the manufacture of parts that require wear resistance.
- It is important to note that due to its high carbon content and low chromium content, 420 grade may experience corrosion problems in some extreme environments such as high temperatures and highly corrosive environments. Therefore, use needs to be evaluated and selected based on the specific application.
Forms
420 Stainless Steel Specifications
- A 240/A 240M Chromium and Chromium-Nickel Stainless Steel Plate, Sheet, and Sliip for Pressure Vessels and for General Applications
- A 276 Stainless Steel Bars and Shapes
- EN 10088-2, Stainless steels. Technical delivery conditions for sheet/plate and strip of corrosion-resisting steels for general purposes
Corrosion Resistance
Under hardened conditions, grade 420 steels are resistant to fresh water, alkalis, air, foods and mild acids. The steel grades with a smooth surface finish have excellent performance. The corrosion resistance properties of grade 420 will tend to fall under annealed conditions. The corrosion resistance of grade 420 is lower than that of grade 430 Ferritic alloys with 17% chromium, grade 410 steel and other austenitic grades. Grade 420 steels have good corrosion resistance against food, but continuous exposure of metals to unwashed food substances can lead to pitting corrosion.
Heat Resistance
Its heat resistance depends on the content of its alloying elements and heat treatment process.
Typically, SS 420 has limited heat resistance and is better suited for low-temperature operating environments. Its maximum service temperature is usually 650℃. Beyond this temperature range, the stainless steel will begin to occur nitride precipitation, resulting in excessive grain growth and grain boundary corrosion, which can lead to a serious increase in the thermal embrittlement of the material.
If the heat resistance of 420 grade needs to be improved, heat treatment processes, such as solution treatment and quenching and annealing, can be performed. These treatments can improve the grain boundary structure and grain size of the material, thus improving its heat resistance.
Overall, the heat resistance of 420 SSl is low compared to other heat-resistant stainless steel and is suitable for use in low-temperature environments. For high-temperature applications, it is recommended to choose a stainless steel material with better heat resistance.
Heat Treatment
420 stainless steel is a high carbon content stainless steel with excellent corrosion resistance and mechanical properties. It can be further improved by heat treatment. Using the annealing process, grade 420 stainless steel is heated to 840 to 900°C, then slowly furnace cooled at 600°C and finally air cooled. For process annealing, Grade 420 steel is heated to 735 to 785°C and then air-cooled. For hardening, 420 grade steel is heated to 980 to 1035°C and then air or oil quenched. Temper at 150 to 370°C to obtain high hardness and good mechanical properties, but avoid tempering treatments between 425 and 600°C.
Welding
Grade 420 stainless steels are welded using welding rods, coated with grade 420 metals, to achieve high-strength joints. During the process, steels are pre-heated at 150 to 320°C and post-heated at 610 to 760°C. In the “as welded” condition, parts are welded using grade 309 filler rods to achieve ductile joints. However, grade 309 electrodes or rods are recommended for welding grade 420 steels by AS 1554.6.
Machining
Grade 420 steels can be easily machined in their annealed state, but they are difficult to machine having a hardness greater than 30HRC. One of the most readily available machined alternatives is the free-machining grade 416 steels.
The following are common processing methods for 420 stainless steel:
- Cutting: use a shear, cutter or EDM cutter to cut 420 stainless steel. Ensure that the cutter has the proper cutting capacity and that the tool is sharp.
- Welding: Use suitable welding methods for stainless steel, such as TIG welding or MIG welding. Pay attention to temperature control during the welding process to avoid annealing or oxidizing the steel.
- Bending: Use mechanical bending machine or hand bending tools to bend 420 stainless steel plate or bar into the desired shape. Pay attention to choose the appropriate bending radius to avoid cracks caused in the bending process.
- Milling: use milling machine or gantry machining center to mill 420 stainless steel. Select appropriate tools and cutting parameters to ensure a smooth cutting process and a smooth surface.
- Grinding: Use a sander, polisher, or hand sandpaper to grind the surface of 420 stainless steel to the desired finish. Select different grain sizes of grinding wheels or sandpaper as required.
- Drilling: Drilling operations are performed using a drill press or hand-held drill. Use cobalt or titanium drill bits to ensure stable cutting and cooling lubrication.
- Turning: Use a lathe to turn 420 stainless steel. Select the proper turning tool, cutting speed and feed to obtain the desired accuracy and surface quality.
Applications
420 stainless steel has high hardness and wear resistance, as well as good corrosion resistance, and can be used to manufacture knives, blades, surgical instruments, bearing components, assembly parts, and so on. The material is also easy to process and malleable, easy to be processed into various shapes and sizes through cutting, forging, heat treatment and other processes. It is not usually used at temperatures exceeding 800oF (427oC) due to quick hardening and loss of corrosion resistance.
- Knife manufacturing: 420 stainless steel has good cutting performance and hardness, commonly used in the manufacture of blades, handles, knives scalpels and other medical devices.
- Pressure vessels: Because of its excellent corrosion resistance and high strength, 420 stainless steel is widely used in the manufacture of pressure vessels, tanks and pipelines in the fields of chemical industry, petroleum, natural gas, and so on.
- Food processing equipment: 420 stainless steel meets hygiene standards, has excellent corrosion resistance, and is easy to cut and process, often used in the manufacture of food processing equipment, knives, and cutting instruments.
- Aerospace: 420 stainless steel’s strength and corrosion resistance make it an important material in the aerospace industry, used to manufacture aircraft parts, propellers, shafts, etc.
- Chemical equipment: Because 420 stainless steel can resist the erosion of strong acids, alkalis, salts and other corrosive media, it is widely used in the chemical industry to manufacture chemical equipment, storage tanks, pipelines and so on.
- Medical equipment: 420 stainless steel has good corrosion resistance, high-temperature strength, and low-temperature toughness, and is widely used in the manufacture of medical equipment, surgical instruments, dental instruments and so on.
420 vs 304 Stainless Steel
420 is a martensitic stainless steel grade. As such, its major alloying elements are chromium and carbon, with small amounts of manganese, silicon, and sometimes molybdenum and nickel. 304 is an austenitic stainless steel alloy that contains a substantial amount of nickel along with more chromium than 420. but the carbon level is much lower than that of 420.
One significant difference lies in their corrosion resistance. 304 stainless steel is good resistant to corrosion, while 420 grade offers good corrosion resistance in mild environments, it is not as resistant as 304 stainless steel. In terms of strength and hardness, 420 steel excels. 304 stainless steel provides better ductility and toughness, but it is not as hard or strong as 420 alloy.
420 vs 316 Stainless Steel
420 stainless steel is martensitic stainless steel whose main components include carbon, chromium and molybdenum. It has high hardness and good wear resistance and is commonly used in applications requiring high hardness and wear resistance, such as cutting tools and bearings. However, 420 stainless steel has relatively poor corrosion resistance, especially in chloride environments where pitting corrosion is likely to occur. Therefore, 420 stainless steel is suitable for occasions where the performance requirements are not particularly high, such as general mechanical and electrical equipment.
316 stainless steel is austenitic stainless steel whose main components include chromium, nickel and molybdenum. It has excellent corrosion resistance, especially in chloride environments, and can resist pitting and crevice corrosion. 316 stainless steel is widely used in strong corrosive environments such as marine and chemical industries and is one of the preferred materials in these areas. In addition, 316 stainless steel has good mechanical properties and machinability for a variety of industrial applications.
420 vs 430 Stainless Steel
- Properties: 420 stainless steel has better wear resistance and higher hardness, but its corrosion resistance is relatively weak. In contrast, 430 stainless steel has good oxidation and corrosion resistance, although its mechanical properties and process performance are slightly inferior.
- Material: 420 stainless steel belongs to the martensitic stainless steel category, while 430 stainless steel belongs to the ferritic stainless steel type.
- Elemental composition: 420 stainless steel has high carbon content, carbon content ranges from 0.30 to 0.40%, and chromium content is 12.0 to 14.0. 430 stainless steel has relatively high chromium content, carbon content is not more than 0.12%, and chromium content is between 16.00 and 18.00%.
- Processing methods: 420 stainless steel can be treated by thermal hardening, such as quenching and tempering, to improve the hardness and surface wear resistance. 430 stainless steel is suitable for deep drawing processing, its thermal conductivity is better than austenitic stainless steel, and the coefficient of thermal expansion is smaller.
- Application: 420 stainless steel is commonly used in precision machinery, bearings, instruments, transport tools, etc. 430 stainless steel is widely used in nitric acid and food industry equipment, fuel burner parts, household appliances and home appliance parts, etc.
FAQ
420 stainless steel is a high carbon martensitic stainless steel with high hardness and wear resistance, suitable for making knives, blades, molds and other tools that require high hardness and wear resistance. This stainless steel has good resistance to atmospheric conditions under hardening conditions and has a certain degree of wear and corrosion resistance, and high hardness, which makes it very suitable for the production of cutting tools.
The hardness range of 420 stainless steel is 48-52 HRC on the Rockwell Hardness C scale. Specifically, 420 stainless steel can achieve a hardness of 52-55 HRC after quenching and tempering treatments, while the hardness in the annealed condition is lower, usually below 235 HB. In addition, 420 stainless steel can reach a hardness of over 217 HB after quenching and tempering, while the hardness in the annealed condition does not exceed 235 HB These hardness values indicate that 420 stainless steel has a high degree of hardness and wear resistance, and is suitable for use in applications where high hardness and wear resistance are required.
The strength of 420 stainless steel generally ranges from 500 to 900 MPa, depending on the heat-treated state of the material and the specific manufacturing process.