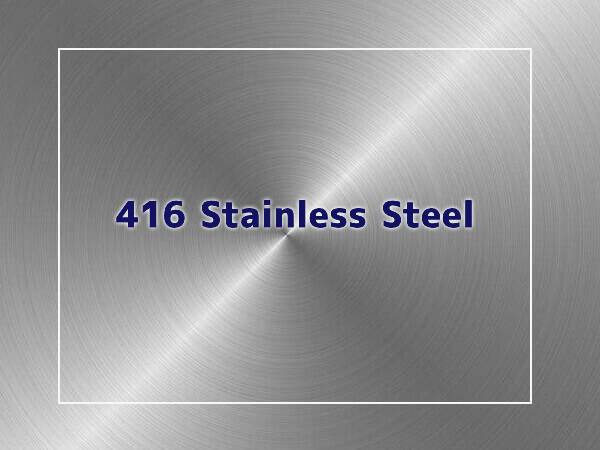
416 stainless steel is a martensitic stainless steel grade with most of the free-machining properties, It has the highest machinability of any stainless steel at about 85% of that of free-machining carbon steel. Martensitic stainless steels were designed to be hardenable by heat treatment and also corrosion resistant. Although stainless steel 416 and other martensitic stainless steels are not as resistant as austenitic or ferritic stainless, they still demonstrate good corrosion and oxidation resistance and high strength in hardened and tempered conditions.
Stainless Steel 416 is magnetic, highly machinable and is known for being wear-resistant. Other characteristics include non-seizing and non-galling properties, resistance to mildly corrosive environments, and reasonable strength in the tempered and hardened state. Stainless Steel 416 is not approved for use in high-sulfur environments. To be the first “free machining” stainless, Stainless Steel 416 can be easily turned, tapped, broached, drilled, reamed, threaded and milled per various machine manufacturer’s recommendations for various suitable tool speeds, feeds and types.
The machinability can be improved by adding sulphur, which leads to the formation of manganese sulphide inclusions. The addition of sulphur also reduces the formability, weldability and corrosion resistance of 416 steels to below that of grade 410. Because of their high machinability and low cost, grade 416 steels are available in highly tempered, hardened or unhardened forms.
416 Stainless Steel Composition
Grade | C, max | Mn, max | Si, max | P, max | S, min | Cr | Mo, max |
---|---|---|---|---|---|---|---|
416 | 0.15 | 1.25 | 1.00 | 0.06 | 0.15 | 12-14 | 0.6 |
416 Stainless Steel Mechanical Properties
Tempering Temperature (°C) | Tensile Strength (MPa) | Yield Strength 0.2% Proof (MPa) | Elongation (% in 50mm) | Hardness Brinell (HB) |
---|---|---|---|---|
Annealed * | 517 | 275 | 30 | 262 |
Condition T ** | 758 | 586 | 18 | 248-302 |
204 | 1340 | 1050 | 11 | 388 |
316 | 1350 | 1060 | 12 | 388 |
427 | 1405 | 1110 | 11 | 401 |
538 | 1000 | 795 | 13 | 321 |
593 | 840 | 705 | 19 | 248 |
650 | 796 | 670 | 17.5 | 253 |
* Annealed properties are typical for Condition A of ASTM A582.
** Hardened and tempered Condition T of ASTM A582 – Brinell hardness is specified range, other properties are typical only.
# Tempering of this steel at temperatures of 400 to 580°C should be avoided due to low impact resistance.
416 Stainless Steel Physical Properties
Grade | Density (kg/m3) | Elastic Modulus (GPa) | Mean Coefficient of Thermal Expansion (μm/m/°C) | Thermal Conductivity (W/m.K) | Specific Heat 0-100°C (J/kg.K) | Electrical Resistivity (nΩ.m) | |||
---|---|---|---|---|---|---|---|---|---|
0-100°C | 0-315°C | 0-538°C | at 100°C | at 500°C | |||||
416 | 7800 | 200 | 9.9 | 11 | 11.5 | 24.9 | 28.7 | 460 | 570 |
Equivalent Grades
- UNS S41600
- DIN 1.4005
- EN X12CrS13
- JIS SUS 416
- SS 2380
Corrosion Resistance
Grade 416 steels are highly resistant to acids, alkalis, fresh water and dry air. However, they are less corrosion resistant than non-free-machining steels, austenitic grades and grade 430 Ferritic alloys with 17% chromium. These steels are hardened to obtain maximum corrosion resistance and smooth surface. 416 free-machining grades with high sulphur content are inappropriate for chloride and marine environments.
Heat Resistance
Scaling resistance of grade 416 steels under intermittent conditions can be extended up to 760°C, and up to 675°C under continuous operations. Considering the sustainability of mechanical properties, 416 steels should not be employed at temperatures greater than the standard tempering temperatures.
Heat Treatment
Full Annealing – Grade 416 steel can be annealed at temperatures of 815 to 900°C for ½ h. This process is followed by cooling at 30°C for an hour and air-cooling.
Sub-Critical Annealing – Grade 416 steel is heated to 650 to 760°C and air-cooled.
Hardening – The process involves heating grade 416 steels to 925 to 1010°C, oil quenching and tempering to improve mechanical properties. Tempering should not be carried out at temperatures ranging from 400 to 580°C, owing to poor ductility of grade 416.
Welding
Grade 416 steel exhibits poor weldability. Welding can be carried out by pre-heating 416 steels to 200 to 300°C, followed by re-hardening, annealing or stress relieving at 650 to 675°C.
Grade 410 low hydrogen electrodes can be used for welding purposes. Grade 309 filler rods can also be used for materials that require moderate hardening.
Machining
Grade 416 steels offer the highest machinability of any stainless steel in their sub-critical annealed condition.
Applications
- Medical instruments: AISI416 stainless steel is a medical-grade stainless steel material, due to its good corrosion resistance and high strength, it is often used in the manufacture of medical equipment, such as scalpels, surgical scissors and so on.
- Chemical equipment: AISI416 stainless steel is also widely used in the chemical industry. Due to its corrosion and heat resistance, it is used in the manufacture of chemical equipment such as reactors and storage tanks.
- Food processing equipment: AISI416 stainless steel meets the food safety standards, so it is often used in the manufacture of food processing equipment, such as knives, cutlery and so on.
- Building structure: AISI416 stainless steel has high strength and good corrosion resistance, so it is also used in building structures, such as bridges, building support structures and so on.
Disadvantages of 416 Stainless Steel
- Lower corrosion resistance: 416 stainless steel has lower corrosion resistance than austenitic stainless steels such as 304 or 316. It is not suitable for use in high sulphur or acidic environments because high phosphorus and sulphur content will reduce its corrosion resistance.
- Unsuitable for high sulphur environments: Because of the potential risk of corrosion in high sulphur environments, 416 stainless steel does not meet NACE MR0175 and MR0103 standards for use in high sulphur environments such as sulphurous gases.
- Poor weldability: Although 416 stainless steel can be welded, it must be annealed at approximately 1450°F (~788°C) after welding to improve its ductility and corrosion resistance. Relatively poor weldability requires special attention.
- Low impact resistance: 416 stainless steel is unsuitable for use when tempered in the 400-580°C range due to its low impact resistance. This limits its use in certain applications.
316 vs 416 stainless steel
- Chemical composition:
- 416 stainless steel: low carbon content, contains about 12% chromium, no nickel and molybdenum, high sulphur content (not less than 0.15%), which makes its cutting performance good.
- 316 stainless steel: contains 10% nickel, 16% chromium and 2% molybdenum, which gives it strong corrosion and rust resistance.
- Corrosion resistance:
- 416 stainless steel: corrosion resistance is not as good as 316 stainless steel, mainly used in automatic lathe, CNC lathe mass production.
- 316 stainless steel: has better corrosion resistance, especially the resistance to chloride ion corrosion is better than 304 stainless steel, commonly used in the food industry and surgical equipment.
- Cutting performance:
- 416 stainless steel: due to its high sulphur content (>0.15%), cutting performance is good, especially for automatic lathes and CNC lathes mass production.
- Stainless steel 316: relatively poor cutting properties, unsuitable for applications requiring high volumes of cutting.
- Application areas:
- 416 stainless steel: mainly used in the production of solenoid valves, microtome motors and electrical components, especially suitable for automatic lathes and CNC lathes mass production.
- 316 stainless steel: commonly used in the food industry, medical equipment and chemical industry, especially for applications requiring high corrosion resistance.