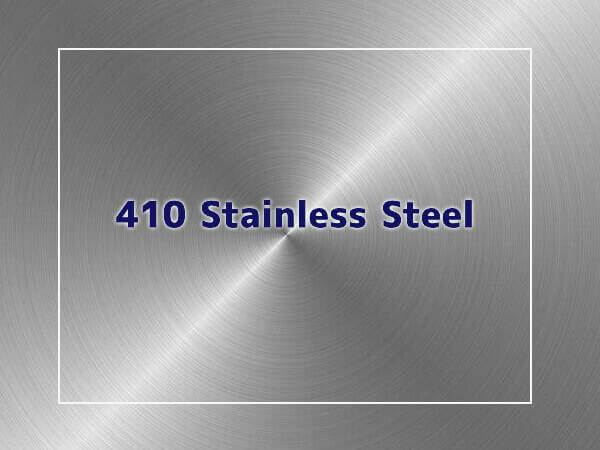
410 stainless steel is hardenable martensitic stainless steel containing at least 11.5% chromium, which provides good corrosion resistance properties. 410 grade offers high strength and hardness with a moderate level of corrosion resistance, however, the corrosion resistance can be further enhanced by a series of processes such as hardening, tempering and polishing. Quenching and tempering can harden grade 410 steel.
410 stainless steel is the basic martensitic stainless steel suitable for highly stressed parts where corrosion resistance, good strength, and ductility are needed. 410 alloy can be used up to 1200ºF (649ºC) where resistance to scaling and oxidation is required. It is used for cutlery applications, kitchen utensils and hand tools and is magnetic in both the annealed and hardened conditions.
410 stainless steel Composition
The chemical composition of 410 stainless steel contains 11.5–13.5% chromium (Cr) and iron, high carbon content (max 0.15%), and less nickel content (0.50% Max).
C | Mn | Si | P | S | Cr | Ni | Iron | |
---|---|---|---|---|---|---|---|---|
410 | 0.08-0.15 | 1.00 max | 1.00 max | 0.04 max | 0.03 max | 11.5 – 13.5 | 0.50 max | Bal. |
410 stainless steel Mechanical Properties
Grade | Tensile Strength, ksi (MPa) min | Yield Strength 0.2% offset ksi (MPa) min | Elongation (% in 50mm) min | Hardness (Brinell) MAX | Hardness (Rockwell B) MAX |
---|---|---|---|---|---|
410 | 65 (450) | 30 (205) | 20 | 217 | 96 |
410 Stainless Steel Physical Properties
Physical Properties | Value |
---|---|
Density, g/cm3 (lb/in3) | 7.9 (0.29) |
Melting point, °C (°F) | 1480-1530 (2700-2790) |
Magnetic permeability | 700-1000 |
Specific heat capacity, J/kg·K (Btu/lb ·°F) | 460 (0.11) at 20 °C (68°F) |
Electrical resistivity, μΩ·m | 0.57 at 20 °C (68°F) |
Elastic modulus (Modulus of elasticity), Gpa (106 psi) | 200 (29.0) |
Young’s modulus, Gpa (106 psi) | 190-210 (27.6-30.4) |
Thermal diffusivity, mm2/s (in2/s) | 6.7 (0.01) at 20 – 100 °C (68 – 212 °F) |
Thermal conductivity, W/m·K (Btu/ft · h ·°F) | 24.9 (14.4) at 100 °C (212 °F) |
28.7 (16.6) at 500 °C (932 °F) | |
Coefficient of thermal expansion, 10-6/K (μin./in. ·°F) | 9.9 (5.5) at 0-100 °C (32-212 °F) |
11.4 (6.3) at 0-315 °C (32-600 °F) | |
11.6 (6.4) at 0-538 ℃ (32-1000 °F) |
410 Stainless Steel Equivalent
- EN X12Cr13
- DIN 1.4006
- GOST 12KH1315KH13L
- BS 410S21
- AFNOR Z10C13
410 Stainless Steel Features
- Martensitic stainless steel grade with high strength and hardness
- Moderate corrosion resistance
- It is magnetic in both the annealed and hardened conditions
- High carbon content excellent wear resistance
- Thermal conductivity is improved and thermal expansion is reduced relative to austenitic stainless grades.
- Low nickel content (0.50 Max).
- Melting Point: 2729°F / 1495°C
- The equivalent grades are UNS S41000 and EN 1.4006.
- Limited formability and weldability, compared to the austenitic stainless steel.
Corrosion Resistance
Grade 410 provides good corrosion resistance to air, gas, mild acids, water and some chemicals. It exhibits good resistance to ammonia, nitric acid, concentrated sulfuric acid, dilute acetic acid and naphtha. Resistance to food acids is good. Maximum corrosion resistance is achieved in the fully hardened condition. However, grade 410 steel is less corrosion resistant than austenitic grades and grade 430 ferritic alloys containing 17% chromium. A smooth surface finish offers improved performance of steels.
Heat Resistance
Grade 410 steels have good scaling resistance at temperatures of up to 650 °C. However, the mechanical properties of the material will tend to reduce at temperatures ranging from 400 to 580 °C.
Heat Treatment
Grade 410 can be fully annealed at 815 to 900 °C temperatures, followed by slow furnace cooling and air-cooling. Process annealing of grade 410 steels can be carried out at temperatures ranging from 650 to 760 °C and air-cooled.
Hardening of grade 410 stainless steel can be performed at 925 to 1010 °C, followed by air and oil quenching. Heavy sections of grade 410 need to be oil-quenched. Tempering, to enhance the mechanical properties and hardness of grade 410 steels, follows this process. It is not recommended to perform tempering at temperatures from 400 to 580 °C.
Welding
Grade 410 steels can be welded using all conventional welding techniques, but the materials should be pre-heated at 150 to 260 °C followed by post-weld annealing treatment, to mitigate cracking. Grade 410 welding rods are recommended for tempering and post-hardening. In the “as welded” conditions, grade 309 filler rods can be used to achieve a ductile joint.
According to AS 1554.6 standards, grade 309 electrodes or rods are preferred for welding 410 steel.
Machining
Grade 410 steels can be easily machined in highly tempered or annealed conditions. However, it is hard to machine grade 410 steels if they are hardened above 30HRC. Free machining grade 416 is the best alternative.
Applications
410 stainless steel used for applications involving mild corrosion, heat resistance and high strength.
- Cutlery
- Steam and gas turbine blades
- Kitchen utensils
- Bolts, nuts, screws
- Pump and valve parts and shafts
- Mine ladder rugs
- Dental and surgical instruments
- Nozzles
- Hardened steel balls and seats for oil well pumps
Standards
- ASTM A240 – Standard Specification for Chromium and Chromium-Nickel Stainless Steel Plate, Sheet, and Strip for Pressure Vessels and for General Applications
- ASTM A268 – Standard Specification for Seamless and Welded Ferritic and Martensitic Stainless Steel Tubing for General Service
- ASTM A276 – Standard Specification for Stainless Steel Bars and Shapes
Forms
410 vs 304 Stainless Steel
410 grade is martensitic stainless steel, containing 11.5–13.5% chromium, minimal to zero nickel (0–0.75%), and high carbon content compared to 304. 304 stainless steel is an austenitic stainless steel containing 18–20% chromium and 8–10.5% nickel. It has a lower carbon content (max 0.08%) than 410 stainless steel.
410 stainless steel provides good corrosion resistance, but only in mild or non-corrosive environments, It is very susceptible to pitting and fracture corrosion in moderate chloride environments. 304 stainless steel has excellent corrosion resistance in various environments, including corrosive chemicals, acids, and saltwater. It is highly resistant to corrosion and staining.
410 stainless steel has high strength, impact resistance, and hardness which can all be improved by traditional heat treatment methods. 304 stainless steel offers lower strength and hardness than 410 alloys but has higher ductility and toughness, better elongation at break, and less brittle behavior than 410 grade.
410 vs 316 Stainless Steel
The main differences between 410 and 316 stainless steel are their composition, corrosion resistance, and application areas.
First, 410 stainless steel belongs to martensitic stainless steel, whose main component is chromium and does not contain nickel, while 316 stainless steel is austenitic stainless steel, which contains chromium and nickel, and molybdenum is also added. This makes 316 stainless steel superior to 410 stainless steel in terms of corrosion resistance.
In terms of corrosion resistance, 410 stainless steel corrosion resistance is poor, mainly because the corrosion resistance requirements of the environment are not high. And 316 stainless steel due to the inclusion of molybdenum, has better corrosion resistance, especially in the chloride environment outstanding performance, commonly used in marine environments and other highly corrosive occasions.
Application areas, 410 stainless steel due to poor corrosion resistance, mainly for corrosion resistance requirements of the environment is not high, such as cutlery in the blade class, fork class. And 316 stainless steel due to its excellent corrosion resistance and mechanical properties, is widely used in petroleum, chemical, medical, food, light industry, machinery and instrumentation and other industrial fields, as well as construction and various applications in the marine environment.