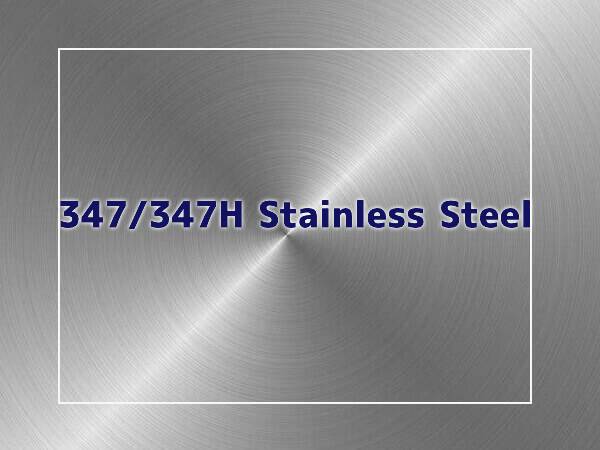
347 stainless steel is a columbium-stabilized austenitic stainless steel grade with good general corrosion resistance and somewhat better resistance in strong oxidizing conditions than 321 (UNS S32100). It has excellent resistance to intergranular corrosion after exposure to temperatures in the chromium carbide precipitation range of 800 – 1500°F (427 – 816°C). The alloy has excellent oxidation resistance and creep strength to 1500°F (816°C). It also possesses good low-temperature toughness.
347H stainless steel is the higher carbon (0.04 – 0.10) version of the alloy. It was developed for enhanced creep resistance and higher strength at temperatures above 1000°F (537°C). At high temperatures, 347H stainless steel is more durable than other stainless steel materials, this makes it very popular for working in high-temperature environments. In high-temperature corrosive environments, 347H stainless steel can maintain its strength and durability without embrittlement or fatigue.
347/347H Stainless Steel Composition
The chemical composition of 347 stainless steel contains 17-19 percent chromium, 9-13 percent nickel and 0.08 percent carbon. There are also small amounts of titanium, niobium and molybdenum. The addition of these elements gives 347 stainless steel its excellent high-temperature resistance while maintaining its corrosion resistance and mechanical strength.
C | Cr | Mn | Ni | P | S | Si | Cb/Ta | |
---|---|---|---|---|---|---|---|---|
347 | 0.08 Max | Min: 17.0 Max: 20.0 | 2.0 Max | Min: 9.0 Max: 13.0 | 0.04 Max | 0.30 Max | 0.75 Max | Min:10x C Max: 1.0 |
347H | Min: 0.04 Max: 0.10 | Min: 17.0 Max: 20.0 | 2.0 Max | Min: 9.0 Max: 13.0 | 0.03 Max | 0.30 Max | 0.75 Max | Min:10x C Max: 1.0 |
347/347H Stainless Steel Mechanical Properties
Grade | Tensile Strength Ksi (MPa) Min | Yield Strength 0.2% Ksi Offset Ksi (MPa) Min | Elongation (% In 50mm) Min | Hardness (Brinell) MAX | Hardness (Rockwell B) MAX |
---|---|---|---|---|---|
347/347H | 75 (515) | 30 (205) | 40 | 201 | 95 |
347 Stainless Steel Physical Properties
- Density: 0.288 lbs/in3, 7.96 g/cm3
- Specific Heat: 0.12 BTU/lb-°F (32 – 212°F), 500 J/kg-°K (0 – 100°C)
- Modulus of Elasticity: 28.0 x 106 psi, 193 GPa
- Thermal Conductivity 200°F (100°C): 133 BTU/hr/ft2/ft/°F, 16.3 W/m-°K
- Melting Point: 2550 – 2635°F, 1398 – 1446°C
- Electrical Resistivity: 72 Microhm-cm at 20°F
347 Stainless Steel Equivalent
- UNS S34700
- DIN 1.4450
- JIS SUS347
- GOST 08KH18N12B
- EN X6CrNiNb18-10
- GB/T S34778
Corrosion Resistance
Alloy 347 stainless steel exhibits good general corrosion resistance that is comparable to 304. It was developed for use in the chromium carbide precipitation range of 800 – 1500°F (427 – 816°C) where un-stabilized alloys such as 304 are subject to intergranular attack.
The alloy can be used in nitric solutions, most diluted organic acids at moderate temperatures and pure phosphoric acid at lower temperatures and up to 10% diluted solutions at elevated temperatures. Alloy 347 stainless steel plate resists polythionic acid stress corrosion cracking in hydrocarbon service. It can also be utilized in chloride or fluoride-free caustic solutions at moderate temperatures.
Alloy 347/347H stainless steel does not perform well in chloride solutions, even in small concentrations, or in sulfuric acid.
Machinability
Machining grade 347H stainless steel is slightly tougher than that of grade 304 steel. However, the hardenability of this steel can be minimized by the use of constant positive feeds and slow speeds.
Welding
347/347H has excellent weldability and is suitable for the full range of conventional welding methods (like MMA, MIG, MAG, TIG, SAW, LBW, or RSW), except gas welding.
Grade 347H stainless steel can be welded using most of the resistance and fusion methods. Oxyacetylene welding is not preferred for this steel.
Hot Working
Forging, upsetting and other hot work processes can be performed at 1149 to 1232°C (2100 to 2250°F). The grade 347H steel has to be water-quenched and annealed to obtain maximum hardness.
Cold Working
347/347H can be readily formed and fabricated by the full range of cold-forming operations. It can be used in heading, drawing, and bending. Any cold working operations will increase the strength and hardness of the material and may leave it slightly magnetic. Work hardening is accentuated by the partial transformation of the austenite phase of the material to hard martensite.
Heat Treatment
Grade 347H stainless steel can be annealed at temperatures ranging from 1010 to 1193°C (1850 to 2000°F) and then quenched with water.
Hardening
Grade 347H stainless steel cannot be hardened by heat treatment. The hardness and strength of the steel can be increased through cold working.
Forms
Application
- Chemical industry: Used in chemical industry equipment for the manufacture of nitric acid and derivatives, salt and fertiliser and other related equipment.
- Refrigeration, pharmaceutical, food industry: there are applications in the refrigeration industry, pharmaceutical industry, food industry (such as food processing plants, dairy plants, sugar factories, breweries, etc.).
- Fuel industry: used in oil refineries and petrochemical plants, for example, it can be used in the manufacture of pipelines, autoclaves, transport tanks, heat exchangers, absorption towers, pumps, coolers and reactors and other equipment.
347, 347H, 1.4450 Stainless Steel Comparison in Composition
Standard | Grade | C | Mn | Cr | Ni |
---|---|---|---|---|---|
ASTM A240 | 347 | ≤0.08 | ≤2.00 | 17.0-19.0 | 9.0-13.0 |
ASTM A240 | 347H | 0.04-0.10 | ≤2.00 | 17.0-19.0 | 9.0-13.0 |
EN 10028-7 | 1.4550 | ≤0.08 | ≤2.00 | 17.00-19.00 | 9.00-12.00 |
EN 10088-2 | 1.4550 | ≤0.08 | ≤2.0 | 17.0-19.0 | 9.0-12.0 |
EN 10088-3 | 1.4550 | ≤0.08 | ≤2.0 | 17.0-19.0 | 9.0-12.0 |
304 vs 347 Stainless Steel
- Chemical composition, 347 stainless steel contains the element niobium, a rare metal that enhances the strength and corrosion resistance of the material. In contrast, the chemical composition of 304 stainless steel is relatively simple, mainly containing chromium, nickel and a small amount of carbon and manganese.
- Heat resistance, 347 stainless steel performs much better at high temperatures and can maintain good strength and corrosion resistance in the temperature range of 800-1600°C. The 304 stainless steel has a relatively simple chemical composition, containing mainly chromium, nickel and a small amount of carbon and manganese. While 304 stainless steel has poorer heat resistance and is prone to deformation and brittle fracture at high temperatures.
- Corrosion resistance, 347 stainless steel has better corrosion resistance than 304 stainless steel due to the niobium element, especially in the strong acid, alkali and high salinity environment. While 304 stainless steel is prone to rust and corrosion in corrosive environments.
- Welding, 347 stainless steel welding performance is better than 304 stainless steel, because of its high niobium content, which can effectively prevent intergranular corrosion in the welding process. And 304 stainless steel is prone to intergranular corrosion in the welding process.
316 vs 347 Stainless Steel
Stainless steel 347 is an austenitic stainless steel containing the elements niobium or titanium, which gives it excellent resistance to oxidation at high temperatures and prevents intergranular corrosion. In contrast, 316 stainless steel is also austenitic stainless steel, but the addition of molybdenum improves its corrosion resistance in a variety of corrosive environments, especially in environments containing chlorides to show better resistance to pitting corrosion.
In terms of applications, 347 stainless steel is commonly used in high-temperature environments, such as aero-engine components and boiler parts, as it is able to maintain stable performance at high temperatures. 316 stainless steel is widely used in applications requiring corrosion resistance, such as food processing, chemical equipment and marine engineering.
Related References
- ASTM A240, Standard Specification for Chromium and Chromium-Nickel Stainless Steel Plate, Sheet, and Strip for Pressure Vessels and for General Applications
- ASTM A480, Standard Specification for General Requirements for Flat-Rolled Stainless and Heat-Resisting Steel Plate, Sheet, and Strip
- EN 10088-2, Stainless steels. Technical delivery conditions for sheet/plate and strip of corrosion-resisting steels for general purposes
- EN 10088-3, Stainless steels. Technical delivery conditions for semi-finished products, bars, rods, wire, sections and bright products of corrosion-resisting steels for general purposes
- EN 10088-4, Stainless steels. Technical delivery conditions for sheet/plate and strip of corrosion-resisting steels for construction purposes
- EN 10088-5, Stainless steels. Technical delivery conditions for bars, rods, wire, sections and bright products of corrosion-resisting steels for construction purposes
- ASTM A249, Standard Specification for Welded Austenitic Steel Boiler, Superheater, Heat-Exchanger, and Condenser Tubes
- ASTM A213, Standard Specification for Seamless Ferritic and Austenitic Alloy-Steel Boiler, Superheater, and Heat-Exchanger Tubes
- ASTM A312, Standard Specification for Seamless, Welded, and Heavily Cold Worked Austenitic Stainless Steel Pipes
- ASTM A276, Standard Specification for Stainless Steel Bars and Shape