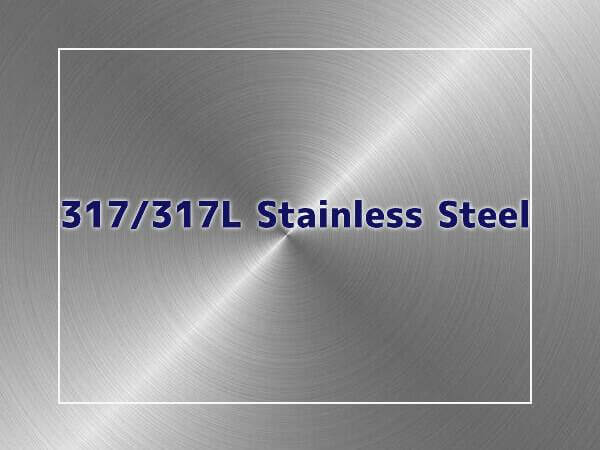
317L stainless steel is a molybdenum-bearing Austenitic chromium-nickel steel, compared to 304L and 316L, low carbon 317L possesses more molybdenum, chromium, and nickel element, which helps 317L provide better corrosion resistance characteristics, The low carbon content makes it suitable for welding without sensitization to intergranular corrosion caused by chromium carbide precipitation in the grain boundaries.
Stainless Steel 317L offers higher creep, stress-to-rupture, and tensile strength at elevated temperatures than conventional stainless steels. It is a low carbon or “L” grade which provides resistance to sensitization during welding and other thermal processes.
317L can be used for many applications, especially in sulfurous acid compounds environment, alloy 317L is non-magnetic in the annealed condition, but it may exhibit a little magnetism during welding or after welding.
317, 317L Stainless Steel Composition
C | Mn | P | S | Si | Ni | Cr | Mo | Fe | |
---|---|---|---|---|---|---|---|---|---|
317 | 0.08 | 2.00 | 0.040 | 0.030 | 1.0 | 11-14 | 18-20 | 3.0-4.0 | Balance |
317L | 0.03 | 2.00 | 0.040 | 0.030 | 1.0 | 11-15 | 18-20 | 3.0-4.0 | Balance |
317, 317L Stainless Steel Mechanical Properties
Tensile Strength(Mpa) | Yield Point(Mpa) | Elongation(%) | HARDNESS | |
---|---|---|---|---|
317 | 515 | 205 | 35 | 95 |
317L | 515 | 205 | 35 | 95 |
317, 317L Stainless Steel Equivalent
AISI | UNS | DIN | EN | JIS | GB |
---|---|---|---|---|---|
317 | S31700 | SUS317 | 06Cr19Ni13Mo3 | ||
317L | S31703 | 1.4438 | X2CrNiMo18-15-4 | SUS317L | 022Cr19Ni13Mo3 |
317L And 1.4438 Comparison
Standard | Grade | C | Mn | Cr | Ni | Mo | N |
---|---|---|---|---|---|---|---|
ASTM A240 | 317L | ≤0.030 | ≤2.00 | 18.0-20.0 | 11.0-15.0 | 3.0-4.0 | ≤0.10 |
EN 10088-2 | 1.4438 | ≤0.030 | ≤2.0 | 17.5-19.5 | 13.0-16.0 | 3.0-4.0 | ≤0.10 |
317L Stainless Steel Physical Properties
Density | Melting Point | Specific Heat | Thermal Conductivity | Coefficient Of Expansion | Electrical Resistivity | Elastic Modulus |
---|---|---|---|---|---|---|
G/Cm3 | (℃) | [J/(Kg·K)] 0~100 ℃ | [W/(M·K)] 100 ℃ | ( 10-6/K )0~100 ℃ | ( NΩ.M | KN/Mm2 |
7.99 | 1371 – 1421 | 500 | 16.3 | 16.6 | 790 | 193 |
Corrosion Resistance
Alloy 317L has excellent corrosion resistance in a wide range of chemicals. It resists attacks in sulfuric acid, acidic chlorine and phosphoric acid. The corrosion resistance of 317 and 317L should be the same in any given environment. The one exception is where the alloy will be exposed to temperatures in the chromium carbide precipitation range of 800 – 1500°F (427 – 816°C). Because of its low carbon content, 317L is the preferred material in this service to guard against intergranular corrosion. In general, austenitic stainless steels are subject to chloride stress corrosion cracking in halide service. Although 317L is somewhat more resistant to stress corrosion cracking than 304/304L stainless steels, because of its higher molybdenum content, it is still susceptible. The higher chromium, molybdenum and nitrogen content of 317L enhance its ability to resist pitting and crevice corrosion in the presence of chlorides and other halides. The Pitting Resistance Equivalent including Nitrogen number (PREN) is a relative measure of pitting resistance. The following chart offers a comparison of Alloy 317L and other austenitic stain
Heat Treatment
Working temperatures of 1652 – 2102°F (900 – 1150°C) are recommended for hot working processes. Do not work this alloy below 1742°F (950°C). If the final forming temperature falls below this threshold, a solution anneal of 1976 – 2156°F (1080 – 1180°C) is necessary. Rapid quenching is required
Welding
317L stainless steel is suitable for all common fusion and resistance methods, with the exception of oxyacetylene welding, low carbon filler metals with molybdenum content higher than that of 317L, or a nickel-base filler metal with sufficient chromium and molybdenum content to exceed the corrosion resistance of 317L should be used to weld 317L steel, post weld heat treatment is not necessary.
Typical Applications
- Chemical and marine engineering: 317 stainless steel is widely used in chemical and marine engineering, because of its good corrosion resistance and resistance to chloride erosion, suitable for building exterior materials and petrochemical equipment in coastal areas.
- Architectural decoration: In the field of architectural decoration, 317 stainless steel is used for curtain walls, railings, doors and windows, etc., because it is easy to clean, low maintenance cost and is beautiful.
- Environmental protection: 317 stainless steel corrosion resistance can help reduce the waste pollution of the environment, so there is an important role in the field of environmental protection.
- Paper and printing and dyeing: 317 stainless steel is used in paper making, printing and dyeing equipment, etc. It has good corrosion resistance and resistance to chloride erosion.
317 Stainless Steel vs 316
The main difference between 316 and 317 stainless steel is in chemical composition and properties. 317 stainless steel contains higher molybdenum content, so its corrosion resistance is better than 316 stainless steel, especially in environments containing chloride’s better performance.
Chemical composition, 316 stainless steel has a lower molybdenum content, while 317 stainless steel has a higher molybdenum content. In addition, the chromium content of 317 stainless steel is also higher than 316 stainless steel, which further enhances its corrosion resistance.
Performance, 316 stainless steel has good corrosion resistance and oxidation resistance, which is suitable for many industrial fields, such as food processing, pharmaceuticals and chemicals. 317 stainless steel has better corrosion resistance and high-temperature strength due to the higher content of molybdenum and chromium, which is especially suitable for harsh environments, such as marine engineering and chemical processing.
Applications, 316 stainless steel is widely used in marine environments, the food industry and general chemical equipment. 317 stainless steel, on the other hand, is more suitable for use in high-temperature, highly corrosive environments, such as chemical processing facilities and marine engineering projects.
317L Stainless Steel vs 316L
317L stainless steel has better corrosion and heat resistance due to its higher molybdenum content and performs especially well in high temperatures and acidic environments. While 316L stainless steel is still widely used in many applications due to its lower cost and good corrosion resistance.
Firstly, 317L stainless steel contains higher levels of molybdenum (3%-4%), while 316L has a molybdenum content of 2%-3%. This difference allows 317L to perform better in corrosion resistance, especially in acidic environments containing chlorides. Additionally, 317L has a higher chromium content, typically between 18%-20%, compared to 316L’s chromium of 18%-20%.
In terms of corrosion resistance, 317L, due to its higher molybdenum content, offers better resistance to pitting and crevice corrosion, especially at high temperatures and in acidic environments. In contrast, 316L, while also having good corrosion resistance, is not as good as 317L under extreme conditions. For example, 317L performs better in acidic environments containing chlorides, while 316L is suitable for general corrosive environments.
I317L exhibits higher creep strength and better overall performance at elevated temperatures and can withstand higher temperatures. In contrast, 316L does not perform as well as 317L, although it can also be used at high temperatures.
Finally, 317L has better ductility and stress corrosion resistance due to its higher nickel and molybdenum content. 316L, on the other hand, is still widely used in many applications due to its lower cost and good mechanical properties3.
In conclusion, choosing 316L or 317L stainless steel depends on the specific application environment and requirements. If it is required to be used in high temperature and acidic environments, 317L is recommended; while in general corrosive environments, 316L is an economical and reliable choice.
Related References
- ASTM A240/ASME SB240, Standard Specification for Chromium and Chromium-Nickel Stainless Steel Plate, Sheet, and Strip for Pressure Vessels and for General Applications
- ASTM A480, Standard Specification for General Requirements for Flat-Rolled Stainless and Heat-Resisting Steel Plate, Sheet, and Strip
- EN 10088-2, Stainless steels. Technical delivery conditions for sheet/plate and strip of corrosion-resisting steels for general purposes
- EN 10088-3, Stainless steels. Technical delivery conditions for semi-finished products, bars, rods, wire, sections and bright products of corrosion-resisting steels for general purposes
- EN 10088-4, Stainless steels. Technical delivery conditions for sheet/plate and strip of corrosion-resisting steels for construction purposes
- EN 10088-5, Stainless steels. Technical delivery conditions for bars, rods, wire, sections and bright products of corrosion-resisting steels for construction purposes
- ASTM A249, Standard Specification for Welded Austenitic Steel Boiler, Superheater, Heat-Exchanger, and Condenser Tubes
- ASTM A213, Standard Specification for Seamless Ferritic and Austenitic Alloy-Steel Boiler, Superheater, and Heat-Exchanger Tubes
- ASTM A312, Standard Specification for Seamless, Welded, and Heavily Cold Worked Austenitic Stainless Steel Pipes
- ASTM A276, Standard Specification for Stainless Steel Bars and Shape