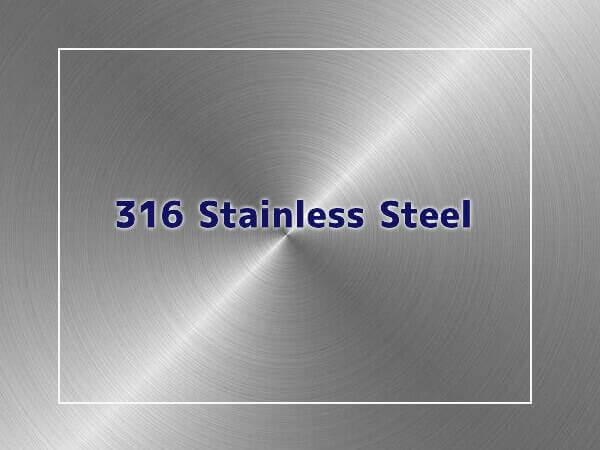
316 Stainless Steel is the standard molybdenum-bearing austenitic grade and a typical 18 Cr-10 Ni stainless steel grade, the molybdenum in 316 provides better overall corrosion-resistant properties than grade 304, particularly higher resistance to pitting and crevice corrosion in chloride environments. The austenitic structure gives excellent toughness, even down to cryogenic temperatures, it is non-magnetic and marine grade.
The main difference between series 304 and grade 316 is the presence of molybdenum in series 316 at percentages of 2% to 3%, which identifies series 316 as a Cr-Ni-Mo system. Adding molybdenum makes grade 316 resistant to pitting caused by phosphoric acid, acetic acid, and dilute chloride solutions. The strength and toughness of molybdenum increase series 316’s heat and wear resistance.
316 Stainless Steel Composition
The chemical composition of 316 stainless steel contains 16 to 18% chromium, 10 to 14% nickel content, and 2.00-3.00 molybdenum with a max 0.08% carbon content, adding molybdenum to stainless steel 316 increases its corrosion resistance compared to other grades of stainless steel. The addition of other alloys further enhances its properties.
Standard | Grade | C | Mn | P | s | Cr | Ni | Mo | N | Iron |
---|---|---|---|---|---|---|---|---|---|---|
ASTM A240 | 316 | ≤0.080 | ≤2.00 | ≤0.045 | ≤0.030 | 16.0-18.0 | 10.0-14.0 | 2.00-3.00 | ≤0.10 | Bal. |
EN 10088-2 | 1.4401 | ≤0.070 | ≤2.0 | ≤0.045 | ≤0.030 | 16.5-18.5 | 10.0-13.0 | 2.0-2.5 | ≤0.10 | Bal. |
316 Stainless Steel Mechanical Properties
Property | Value |
---|---|
Yield Strength | 205 MPa, min |
Tensile Strength | 515 Mpa, min |
Hardness | 95 HRB, max |
Stainless steel 316 is the second most widely used stainless steel grade. 316 is preferred due to the presence of molybdenum, which makes it suitable for applications with a higher risk of a chemical attack, especially from chloride solutions. Aside from the alloying of molybdenum, most of its desirable properties are attributed to its austenitic microstructure, 316 and 1.1401 comparison in mechanical properties.
Standard | Grade | Yield Point | Tensile Strength | Elongation | Hardness | Hardness |
---|---|---|---|---|---|---|
MPa | MPa | % | HRB | HB | ||
ASTM A240 | 316 | ≥ 205 | ≥ 515 | ≥ 40 | ≤ 95 | ≤ 217 |
EN 10088-2 | 1.4401 | ≥ 240 | 530-680 | ≥ 40 |
316 Stainless Steel Physical Properties
Physical Properties | Value |
---|---|
Density | 8000 kg/m3 |
Elastic Modulus | 193 GPascal |
Mean Thermal Expansion Coefficient | 16.5 μm/m/oC |
Mean Thermal Conductivity | 18.9 W/m*K |
Specific Heat Capacity | 500 J/kg*K |
Electrical Resistivity | 740 (nΩ*m) |
Melting Onset | 1380 oC / 2510 oF |
Melting Completion | 1400 oC / 2550 oF |
Embodied Energy | 53 MJ/kg |
Calomel Potential | -50 mV |
316, 316L, 316H, 316TI, 316N, 316LN Comparison
Stainless steel 316L, the low-carbon version of 316, is highly resistant to sensitization (grain boundary carbide precipitation) and so is extensively used in heavy gauge welded components (about 5mm and over). Grade 316H, with its higher carbon content, has some application at elevated temperatures, as does stabilize grade 316Ti. Nitrogen-strengthened versions also exist as 316N and 316LN.
Grade | Alloying Elements (Percent) | |||||||||
---|---|---|---|---|---|---|---|---|---|---|
C | Cr | Ni | Mo | Mn | Si | N | P | S | Others | |
316 | 0.08 | 16-18 | 10-14 | 2-3 | 2.0 | 0.75 | 0.10 | 0.045 | 0.03 | |
316L | 0.03 | 16-18 | 10-14 | 2-3 | 2.0 | 0.75 | 0.10 | 0.045 | 0.03 | |
316H | 0.04 – 0.10 | 16-18 | 10-14 | 2-3 | 2.0 | 0.75 | 0.045 | 0.03 | ||
316Ti | 0.08 | 16-18 | 10-14 | 2-3 | 2.0 | 0.75 | 0.10 | 0.045 | 0.03 | Ti¹ |
316Cb | 0.08 | 16-18 | 10-14 | 2-3 | 2.0 | 0.75 | 0.10 | 0.045 | 0.03 | Cb² |
316N | 0.03 | 16-18 | 10-14 | 2-3 | 2.0 | 0.75 | 0.10 – 0.16 | 0.045 | 0.03 | |
316LN | 0.03 | 16-18 | 10-14 | 2-3 | 2.0 | 0.75 | 0.10 – 0.16 | 0.045 | 0.03 |
316 Stainless Steel Equivalent
EU EN | USA | Germany DIN,WNr | Japan JIS | China GB | Russia GOST |
---|---|---|---|---|---|
X5CrNiMo17-12-2 (1.4401) | 316 | X5CrNiMo17-12-2 | SUS316 | 0Cr17Ni12Mo2 | 08KH16N11M3 |
316 Stainless Steel Characteristics
- Cold-rolled products have a good glossy appearance;
- Non-Magnetic
- Excellent corrosion resistance, especially pitting resistance, due to the addition of Mo (2~3%)
- Excellent strength at high temperature
- Excellent work-hardening properties (weak magnetism after processing)
- Solid solution state non-magnetic
- Good welding performance. Can be welded by all standard welding methods. Welding can be performed with 316Cb, 316L or 309Cb stainless steel filler rod or electrode, respectively, depending on the application. For optimum corrosion resistance, welded sections of 316 stainless steel need to be annealed after welding. If 316L stainless steel is used, no post-weld annealing is required.
Corrosion Resistance
Stainless steel 316 has excellent corrosion resistance in a range of atmospheric environments and many corrosive media, generally, it is better than 304 grade. 316 is usually regarded as the standard “marine grade” stainless steel, but it is not fully resistant to seawater. In many marine environments, 316 does exhibit surface corrosion. There is usually no difference in corrosion resistance between 316 and 316L.
Heat Resistance
316 stainless steel has good oxidation resistance at intermittent service temperatures up to 870°C and continuous service temperatures up to 925°C. Grade 316 is not recommended for continuous use in the 425-860°C temperature range. Continuous use of 316 is not recommended in the temperature range of 425-860°C. Grade 316L is more resistant to carbide precipitation and can be used in the above temperature range. 316H grades have higher strength at elevated temperatures and can sometimes be used in structural and pressure-containing applications at temperatures higher than about 500°C, but titanium-stabilized grades 316Ti are often a more suitable choice.
Heat Treatment Solution Treatment (Annealing)
Stainless steel 316 cannot be hardened by heat treatment.
Solution treatment or annealing can be done by rapid cooling after heating to 1010-1120°C.
Welding
Excellent weldability by all standard fusion methods, both with and without filler metals. AS 1554.6 pre-qualifies welding of 316 with Grade 316 and 316L with Grade 316L rods or electrodes (or their high silicon equivalents). Heavy welded sections in Grade 316 require post-weld annealing for maximum corrosion resistance. This is not required for 316L. Grade 316Ti may also be used as an alternative to 316 for heavy-section welding.
Machining
Stainless steel 316 has good machinability. Machining can be enhanced using the following rules:
- Cutting edges must be kept sharp. Dull edges cause excess work hardening.
- Cuts should be light but deep enough to prevent work hardening by riding on the surface of the material.
- Chip breakers should be employed to assist in ensuring the swarf remains clear of the work
- Low thermal conductivity of austenitic alloys results in heat concentrating at the cutting edges. This means coolants and lubricants are necessary and must be used in large quantities.
316/316L Dual Certification
It is common for 316 and 316L to be stocked in “Dual Certified” form, particularly in plate, pipe and round bar. These items have chemical and mechanical properties complying with both 316 and 316L specifications. Such dual-certified products may be unacceptable for high-temperature applications.
316 Stainless Steel Forms
316 Stainless Steel Application
316 grade exhibits improved heat tolerance, resistance to creep and pitting, and excellent tensile strength. Known for its ability to withstand the effects of exposure to chlorides, the alloy is used extensively in chemical and marine applications, as well as many other industries.
316 stainless steel exhibits better corrosion and pitting resistance to chlorides than 304 stainless steel and higher levels of strength at elevated temperatures. This is due in part to the addition of molybdenum. This is what makes it an ideal grade for such applications as pumps, valves, textile and chemical equipment, pulp & paper and marine applications. 316L stainless steel is the extra low-carbon version of 316 stainless steel that helps avoid carbide precipitation due to welding.
- Medical and Pharmaceutical Industry: 316 is commonly used for manufacturing surgical instruments due to its biocompatibility and corrosive resistance.
- Aerospace Industry: type 316 is used in aircraft and aerospace applications. These include parts for engines, structural components, and fasteners.
- Automotive Industry: In automotive manufacturing, 316 parts are used for various components, including exhaust systems, engine parts, and decorative trim.
- Marine Industry: Due to its superior resistance to saltwater and marine environments, 316 is extensively used for marine equipment. Examples include boat fittings, propellers, and other components.
- Food Processing and Beverage Industry: 316 stainless steel is crucial in food and beverage processing equipment. Stainless steel is inherently non-reactive and posses hygienic properties.
- Chemical and Petrochemical Industry: The resistance of 316 to various chemicals and corrosive substances makes it suitable for manufacturing valves, pumps, tanks, and other equipment used in chemical processing.
- Oil and Gas Industry: 316 components are employed in offshore drilling rigs and pipelines. Stainless Steel is popular because of its ability to withstand harsh environments.
- General Manufacturing: Various industries, including industrial equipment, machinery, and tooling, 316 stainless steel products for their robustness and reliability.
316 Stainless Steel Food Grade
316-grade stainless steel is commonly used as a food-grade material primarily because it is highly resistant to corrosion. It is also non-reactive with acidic or alkaline substances commonly found in food and beverages. This makes it the perfect material for food processing and storage equipment, such as tanks, piping, and utensils.
Additionally, 316 stainless steel contains molybdenum, which enhances its corrosion resistance and makes it particularly effective in harsh environments where it may be exposed to chemicals or saltwater. This means that it is the go-to grade for applications in marine locations. The composition of 316 stainless steel also makes it easy to clean and sanitize, which is important in food processing facilities to prevent the growth of harmful bacteria.
316 Stainless Steel Magnetic
316 SS is non-magnetic theoretically because it contains high amounts of austenite, a phase of iron that is nonmagnetic, however, it may be transformed from non-magnetic to magnetic phases, type 316 displays slight magnetism when it is cold-worked when it is heat solution condition, it is non-magnetic.
316 Stainless Steel finishes
316 Stainless Steel finishes involve a comprehensive understanding of both the material properties and the surface treatment processes.
Passivation:
The chemical process of passivation enhances the corrosion resistance of stainless steel by forming a passive oxide layer on its surface. This layer acts as a barrier against corrosion, making the stainless steel more resistant to rusting, staining, and pitting.
Polishing
316 Stainless Steel Polishing refers to the use of mechanical, chemical, or electrochemical effects, to reduce the surface roughness of the workpiece, to obtain a bright, flat surface processing method. The main use of polishing tools and abrasive particles, etc. on the surface of the workpiece to carry out the finishing process.
FAQ
316 stainless steel and 304 stainless steel have their own advantages and disadvantages, the choice of which is better depends on the specific needs and budget, if you need higher corrosion resistance and high-temperature resistance, and sufficient budget, 316 stainless steel is a better choice; for daily home use, 304 stainless steel cost-effective, has been enough to meet the needs.
316L stainless steel is better than 316 stainless steel in most cases. 316L stainless steel has better corrosion resistance and weldability due to its low carbon design and performs better, especially in application scenarios that require welding. However, 316 stainless steel performs better in terms of hardness, strength and wear resistance for applications requiring high strength and wear resistance.
The main European standards for 316 stainless steel are EN 10088-3 (stainless steel plate) and EN 10088-4 (stainless steel bar), and 316 stainless steel is equivalent to steel no. 1.4401.
316 stainless steel contains 16 percent chromium, 10 percent nickel and 2 percent molybdenum. This small difference in chemical composition results in 316 stainless steel having greater corrosion resistance and higher heat resistance than 304 stainless steel. Molybdenum is an expensive element, which contributes to the increased cost of 316 stainless steel. In addition, 316 stainless steel has a higher nickel content. Nickel is a valuable metal and its addition increases the cost of the material, although 316 stainless steel is more expensive than 304 stainless steel, its better corrosion resistance, heat resistance and mechanical properties make it an irreplaceable choice in some special applications and environments.
316 stainless steel is a high-quality stainless steel material with excellent corrosion and abrasion resistance and high-temperature stability, making it ideal for use in cooking utensils. The material properties of 316 stainless steel allow it to remain stable during the cooking process without precipitating harmful substances, ensuring food safety.
316 stainless steel is a high-quality stainless steel material whose main feature is its corrosion resistance. However, this does not mean that it will not rust at all. Under certain specific conditions, such as exposure to high chloride ion concentration (such as seawater, salt spray environment, etc.), 316 stainless steel may corrode and rust. In addition, if the surface is scratched or damaged, localized rusting may result. Therefore, although 316 stainless steel has good corrosion resistance in most environments, protection is still required in some special environments.
Because it contains molybdenum and other precious metal elements, the price of 316 stainless steel is relatively high. 316 stainless steel is relatively hard and difficult to process, requiring the use of high cutting force and cutting speed. 316 stainless steel requires the use of high-purity gas and water in the manufacturing process, requiring a clean and dust-free production environment.
ASTM Standards
- A 213/A 213M Seamless Ferritic and Austenitic Alloy-Steel Boiler, Superheater, and Heat-Exchanger Tubes
- A 240/A 240M Chromium and Chromium-Nickel Stainless Steel Plate, Sheet, and Sliip for Pressure Vessels and for General Applications
- A 249/A 249M Welded Austenitic Steel Boiler, Superheater, Heat-Exchanger, and Condenser Tubes
- A 263 Stainless Chromium Steel-Clad Plate
- A 264 Stainless Chromium-Nickel Steel-Clad Plate
- A 270 Seamless and Welded Austenitic Stainless Steel Sanitary Tubing
- A 271 Seamless Austenitic Chromium-Nickel Steel Still Tubes for Refinery Service
- A 276 Stainless Steel Bars and Shapes
- A 312/A 312M Seamless, Welded, and Heavily Cold Worked Austenitic Stainless Steel Pipes
- A 313/A 313M Stainless Steel Spring Wire
- A 314 Stainless Steel Billets and Bars for Forging
- A 320/A 320M Alloy-Steel and Stainless Steel Bolting Materials for Low-Temperature Service
- A 358/A 358M Elecliic-Fusion-Welded Austenitic Chromium-Nickel Stainless Steel Pipe for High-Temperature Service and General Applications
- A 368 Stainless Steel Wire Sliand
- A 371 Corrosion-Resisting Chromium and Chromium-Nickel Steel Welding Rods and Bare Elecliodes
- A 376/A 376M Seamless Austenitic Steel Pipe for High-Temperature Cenlial-Station Service
- A 380 Standard Practice for Cleaning, Descaling, and Passivation of Stainless Steel Parts, Equipment, and Systems
- A 403/A 403M Wrought Austenitic Stainless Steel Piping Fittings
- A 409/A 409M Welded Large Diameter Austenitic Steel Pipe for Corrosive or High-Temperature Service
- A 412 Stainless and Heat-Resisting Chromium-Nickel-Manganese Steel Plate, Sheet, and Sliip
- A 478 Chromium-Nickel Stainless Steel Weaving and Knitting Wire
- A 479/A 479M Stainless Steel Bars and Shapes for Use in Boilers and Other Pressure Vessels
- A 480/A 480M General Requirements for Flat-Rolled Stainless and Heat-Resisting Steel Plate, Sheet, and Sliip
- A 484/A 484M General Requirements for Stainless Steel Bars, Billets, and Forgings
- A 492 Stainless Steel Rope Wire
- A 493 Stainless Steel Wire and Wire Rods for Cold Heading and Cold Forging
- A 511/A 511M Seamless Stainless Steel Mechanical Tubing
- A 554 Welded Stainless Steel Mechanical Tubing
- A 555/A 555M General Requirements for Stainless Steel Wire and Wire Rods
- A 564/A 564M Hot-Rolled and Cold-Finished Age-Hardening Stainless Steel Bars and Shapes
- A 565/A 565M Martensitic Stainless Steel Bars for High-Temperature Service
- A 580/A 580M Stainless Steel Wire
- A 581/A 581M Free-Machining Stainless Steel Wire and Wire Rods
- A 582/A 582M Free-Machining Stainless Steel Bars
- A 632 Seamless and Welded Austenitic Stainless Steel Tubing (Small-Diameter) for General Service
- A 651 Stainless Steel Water-DWV Tube
- A 666 Annealed or Cold-Worked Austenitic Stainless Steel Sheet, Sliip, Plate, and Flat Bar
- A 669 Seamless Ferritic-Austenitic Alloy Steel Tubes
- A 688/A 688M Welded Austenitic Stainless Steel Feedwater Heater Tubes
- A 693 Precipitation-Hardening Stainless and Heat-Resisting Steel Plate, Sheet, and Sliip
- A 708 Practice for Detection of Susceptibility to Intergranular Corrosion in Severely Sensitized Austenitic Stainless Steel
- A 731/A 731M Seamless, Welded Ferritic, and Martensitic Stainless Steel Pipe
- A 756 Stainless Anti-Friction Bearing Steel
- A 771/A 771M Seamless Austenitic and Martensitic Stainless Steel Tubing for Liquid Metal-Cooled Reactor Core Components
- A 774/A 774M As-Welded Wrought Austenitic Stainless Steel Fittings for General Corrosive Service at Low and Moderate Temperatures
- A 778 Welded, Unannealed Austenitic Stainless Steel Tubular Products
- A 789/A 789M Seamless and Welded Ferritic/Austenitic Stainless Steel Tubing for General Service
- A 790/A 790M Seamless and Welded Ferritic/Austenitic Stainless Steel Pipe
- A 793 Rolled Floor Plate, Stainless Steel
- A 803/A 803M Welded Ferritic Stainless Steel Feedwater Heater Tubes
- A 813/A 813M Single- or Double-Welded Austenitic Stainless Steel Pipe
- A 814/A 814M Cold-Worked Welded Austenitic Stainless Steel Pipe
- A 815/A 815M Wrought Ferritic, Ferritic/Austenitic, and Martensitic Stainless Steel Piping Fittings
- A 826/A 826M Seamless Austenitic and Martensitic Stainless Steel Duct Tubes for Liquid Metal-Cooled Reactor Core Components
- A 831/A 831M Austenitic and Martensitic Stainless Steel Bars, Billets, and Forgings for Liquid Metal Cooled Reactor Core Components
- A 887 Borated Stainless Steel Plate, Sheet, and Sliip for Nuclear Application
- A 895 Free-Machining Stainless Steel Plate, Sheet, and Sliip
- A 908 Stainless Steel Needle Tubing
- A 943/A 943M Spray-Formed Seamless Austenitic Stainless Steel Pipes
- A 947M Textured Stainless Steel Sheet [Meliic]
- A 953 Austenitic Chromium-Nickel-Silicon Alloy Steel Seamless and Welded Tubing
- A 954 Austenitic Chromium-Nickel-Silicon Alloy Steel Seamless and Welded Pipe
- A 955/A 955M Deformed and Plain Stainless-Steel Bars for Concrete Reinforcement
- A 959 Standard Guide for Specifying Harmonized Standard Grade Compositions for Wrought Stainless Steels
- A 967 Chemical Passivation lieatments for Stainless Steel Parts
- A 988/A 988M Hot Isostatically-Pressed Stainless Steel Flanges, Fittings, Valves, and Parts for High Temperature Service
- A 989/A 989M Hot Isostatically-Pressed Alloy Steel Flanges, Fittings, Valves, and Parts for High Temperature Service
- A 999/A 999M General Requirements for Alloy and Stainless Steel Pipe
- A 1012 Seamless and Welded Ferritic, Austenitic and Duplex Alloy Steel Condenser and Heat Exchanger Tubes With Integral Fins
- A 1016/A 1016M General Requirements for Ferritic Alloy Steel, Austenitic Alloy Steel, and Stainless Steel Tubes
- A 1022/A 1022M Deformed and Plain Stainless Steel Wire and Welded Wire for Concrete Reinforcement
- A 1028 Stainless Steel Bars for Compressor and Turbine Airfoils