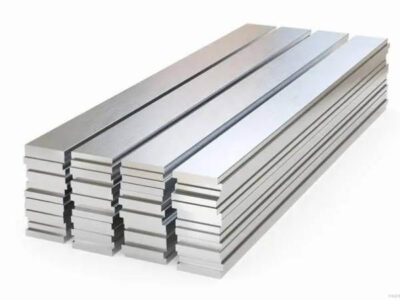
305 stainless steel is an austenitic stainless steel with excellent welding and mechanical properties. Stainless steel 305 is a stainless steel alloy with a specific chemical composition. It consists mainly of 17-19% chromium (Cr), 10.5-13.0% nickel (Ni) and a slight amount of carbon (C). 305 stainless steel has low work-hardening properties compared to other stainless steel materials. It is commonly used in spin-forming processes, special drawing and cold pressing. Its high nickel content makes it excellent for flexing and functionality in welded areas.
305 Stainless Steel Composition
Element | Content (%) |
---|---|
Iron, Fe | Bal |
Chromium, Cr | 17-19 |
Nickel, Ni | 10.5-13.0 |
Manganese, Mn | ≤ 2 |
Silicon, Si | ≤ 0.75 |
Carbon, C | 0.12 |
Phosphorous, P | 0.045 |
Sulfur, S | 0.030 |
305 Stainless Steel Mechanical Properties
Mechanical Properties | Value |
---|---|
Tensile strength, ultimate | 485 MPa |
Tensile strength, yield (@0.2%) | 170 MPa |
Elongation (in 50 mm) | 40 |
Hardness, Brinell HBW | 183 |
Hardness, Rockwell B | 88 |
305 Stainless Steel Physical Properties
- Density: 7.99g/cm³.
- Melting point: 1420 – 1455°C.
- Thermal conductivity: 16.3W/(m-K).
- Modulus of elasticity: 200GPa.
- Thermal expansion: 17.2μm/m℃(20 – 100℃).
Equivalent
- UNS S30500
- JIS SUS305
- DIN: X5CrNi1911
- EN 1.4303
Products
- screws
- bar
- bolts
- coil
- pipe
- sheet
- strip
- tubing
- wire
305 Stainless Steel Properties
- Good weldability: The high nickel content of 305 stainless steel gives it excellent weldability. In the welding process, it can maintain good deformability and toughness, reducing the occurrence of welding deformation and cracks.
- Good bending properties: Due to the special chemical composition of 305 stainless steel, it has excellent bending properties. During cold working and forming, 305 stainless steel can withstand large deformations without fracture or loss of strength.
- Heat Treatment Hardening: After heat treatment (e.g. quenching and tempering), 305 stainless steel hardens, increasing its mechanical properties and strength. This allows it to provide increased wear and impact resistance in certain applications.
- Non-Magnetic: Stainless Steel 305 is an austenitic stainless steel and is non-magnetic. This means that it will not be magnetized when subjected to magnetic fields, making it suitable for specific applications where non-magnetic materials are required, such as electrical and electronic equipment.
Applications
- Kitchen utensils: 305 stainless steel is often used in the production of kitchen utensils, such as pots and pans, cutlery, etc., because its corrosion resistance can ensure that the long-term use will not rust, to maintain the cleanliness and hygiene of the items.
- Tools: Due to its good processing performance, 305 stainless steel is often used to make a variety of tools, such as spanners, screwdrivers and so on.
- Medical equipment: In the medical field, 305 stainless steel is often used to make medical instruments and equipment because of its non-toxic, harmless and corrosion-resistant properties.
- Western-style cutlery: 305 stainless steel is also commonly used in the production of Western-style cutlery, such as knives and forks, because of its beauty and durability.
- Electronic components: In electronics, 305 stainless steel is used to make some electronic components that require high precision and corrosion resistance.
305 Stainless Steel vs 316
Composition
- Stainless steel 316: contains 18 to 20 percent chromium, 10 to 14 percent nickel, and 2 to 3 percent molybdenum, which gives it better corrosion resistance in chloride environments, especially in marine or chemical industry environments.
- Stainless steel 305: contains 17 to 19 percent chromium and 10.5 to 13 percent nickel, but no molybdenum. It is typically used where good corrosion resistance and formability are required.
Properties
- Corrosion resistance: 316 stainless steel has greater resistance to pitting and crevice corrosion due to its molybdenum content, especially at high temperatures and in environments containing chlorides. The corrosion resistance of 305 stainless steel in the presence of chlorides is not as good as 316 stainless steel.
- Temperature resistance: 316 stainless steel excels in high-temperature conditions, able to work stably in environments as high as 1200-1300 degrees Celsius, while 305 stainless steel is relatively weak in high-temperature resistance.
Application
- 316 stainless steel: widely used in the marine environment, chemical processing, food processing, medical devices, pharmaceutical equipment and other fields that require high corrosion resistance12.
- 305 stainless steel: commonly used in the manufacture of fasteners, pipes, valves, kitchen equipment, medical devices and automotive parts for general corrosion resistance applications and deep processing.
Cost
- 316 Stainless Steel: Due to the addition of molybdenum, its cost is usually higher than 305 Stainless Steel.
- 305 Stainless Steel: Relatively economical due to its absence of molybdenum, suitable for cost-sensitive applications.
304 vs 305 stainless steel
304 stainless steel has a nickel content of 8 percent, while 305 stainless steel has a nickel content of 11 percent. Nickel is an important alloying element that improves the properties of stainless steel such as corrosion resistance, heat resistance and strength.305 stainless steel is superior to 304 stainless steel in corrosion resistance and strength.