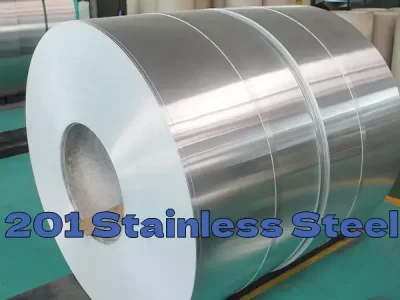
201 stainless steel is an austenitic chromium nickel-manganese stainless steel developed by replacing nickel with manganese, and nitrogen, it provides properties similar to 301 stainless steel and can be used in most applications. 201 stainless steel is a 200 series austenitic stainless steel grade with better corrosion resistance and hot and cold machining performance, enough to replace the previous 304 stainless steel products used indoors, inland cities, and outdoor corrosive environments not strong. it is a lower-cost alternative to the more conventional 304 stainless. 201 alloy is nonmagnetic in the annealed condition but becomes slightly magnetic when cold worked. Stainless steel 201 is annealed at 1010-1093°C (1850-2000°F). Temperature should not be exceeded above 2000°F to avoid scaling. It is rapidly cooled to prevent the crystallization of carbides.
201 stainless steel has good corrosion resistance, excellent machinability and moderate strength, and relatively low cost. However, its corrosion resistance is relatively not good and its strength is not as good as some high nickel stainless steels. When choosing to use 201 alloy, you need to consider its advantages and limitations to ensure that it is suitable for specific applications, 201 grade surface can be finished in various types including 2B, BA, polished, and others.
201 Stainless Steel Composition
Element | Content (%) |
---|---|
Iron, Fe | 72 |
Chromium, Cr | 16.0 – 18.0 |
Manganese, Mn | 5.50 – 7.50 |
Nickel, Ni | 3.50 – 5.50 |
Silicon, Si | 1.0 |
Nitrogen, N | 0.25 |
Carbon, C | 0.15 |
* Maximum, unless range is indicated
201 Stainless Steel Mechanical Properties
Property | Value |
---|---|
Yield Strength, min. (ksi) | 45 |
Tensile Strength, min. (ksi) | 95 |
Elongation, min. (%) | 40 |
Hardness, max. (HRBW) | 100 |
201 Stainless Steel Physical Properties
Property | Value |
---|---|
Density, lb/in3 | 0.283 |
Modulus of Elasticity, psi | 28.6 x 106 |
Coefficient of Thermal Expansion, 68-212˚F, /˚F | 9.2 x 10-6 |
Thermal Conductivity, Btu/ft hr ˚F | 9.4 |
Specific Heat, Btu/lb ˚F | 0.12 |
Electrical Resistivity, Microohm-in | 27.0 |
201 Stainless Steel Equivalent
- JIS SUS 201
- UNS S20100
- DIN 1.4372
- EN X12CrMnNiN17-7-5
201 Stainless Steel Properties
- Non-Magnetic: 201 non-magnetic stainless steel has a low iron content and high nickel content, making it non-magnetic. This makes it ideal for many applications such as electronic equipment, aerospace and medical devices.
- Good corrosion resistance: 201 non-magnetic stainless steel has excellent corrosion resistance to most common corrosive media, including acidic, alkaline and saline solutions. It also has good resistance to oxide reduction reactions.
- High strength and wear resistance: 201 non-magnetic stainless steel has high strength and wear resistance, enabling it to maintain its structural integrity at high temperatures, high pressures and high impact loads.
- Good Cutting and Welding Properties: 201 non-magnetic stainless steel is easy to machine and fabricate and has good cutting and welding properties. It can be shaped and joined by a variety of machining methods.
- Good heat treatment performance: 201 non-magnetic stainless steel can be heat-treated to change its mechanical properties and organizational structure, to adapt to different applications.
201 Stainless Steel Forms
Stainless Steel 201 vs 304
Composition: Stainless steel 201 contains 16-18 percent chromium and 3.50 – 5.50 percent nickel, while stainless steel 304 contains 18 percent chromium and 8 percent nickel.
Corrosion resistance: 201 grade is prone to rust due to its high manganese content, while 304 stainless steel is less prone to rust due to its high chromium content.
Performance: 201 grade is more brittle and hard than 304 stainless steel, while 304 stainless steel has better corrosion resistance, acid and alkali resistance and processing performance.
Application: 201 grade is mainly used for decorative pipes, industrial pipes and some shallow-drawn products, while 304 stainless steel is widely used in industry, furniture decoration, and the medical industries.
Price: As the performance of 304 stainless steel is better than 201, the price of 304 stainless steel is usually higher than 201 stainless steel.
201 Stainless Steel vs 301
Chemical Composition
- 201 stainless steel: 3.5%-5.5% nickel, 5.5%-7.5% manganese.
- 301 stainless steel: nickel content of 6%-8%, manganese content of 2%.
Performance
- Corrosion resistance: 301 stainless steel has good rust resistance under atmospheric conditions, but poor corrosion resistance in reducing media and acid, alkali, salt and other chemical media. corrosion resistance of 201 is not as good as 301, 201 is easy to rust.
- Cold working strengthening: 301 stainless steel is the easiest cold deformation strengthening steel, through cold deformation processing can make the steel strength, hardness, and retain sufficient plasticity and toughness. Stainless steel 201 is mainly used for decorative tubes. industrial pipe and some shallow tensile products.
- Work hardening: 301 stainless steel is easy to produce work hardening when impacted by external forces, which can absorb more impact energy and provide more reliable safety.
Use
- 301 stainless steel: mainly used to withstand higher loads, the requirement to reduce the weight of equipment and rust-free equipment parts. For example, trains, aircraft, conveyor belts, vehicles, bolts, nuts, springs etc. In addition, 301 stainless steel is susceptible to work hardening when hit by external forces, and can be used where higher strength is required. 23
- 201 stainless steel: used for decorative tubes, industrial tubes, and some shallow-drawn products.
201 Stainless Steel vs 316
201 stainless steel contains high manganese and low nickel, so the corrosion resistance and heat resistance are poor, suitable for general environment use. 316 stainless steel contains high nickel and molybdenum, with a high degree of corrosion resistance and heat resistance, suitable for more corrosive environments, such as chemical and Marine environments.
201 Stainless Steel vs 430
Chemical Composition
The chemical composition of stainless steel 430 and 201 is one of the main differences. Stainless steel 430 is composed of iron, chromium, and a small amount of nickel. Among them, the content of chromium is between 16 percent and 18 percent, and the content of nickel is less than 0.75 percent. Stainless steel 201, on the other hand, consists mainly of iron, chromium, and manganese. Among them, chromium content is between 16% and 18%, and manganese content is between 5.5% and 7.5%.
Stainless Steel 430 contains more chromium, while Stainless Steel 201 contains higher levels of manganese. Chromium is an important alloying element that enables stainless steel to have good corrosion resistance. The addition of manganese can improve the strength and hardness of stainless steel. Therefore, in terms of corrosion resistance and mechanical properties, there are some differences between stainless steel 430 and 201.
Physical Properties
Stainless steel 430 and 201 also have some differences in physical properties. Stainless steel 430 has higher hardness and strength and is more resistant to wear than stainless steel 201. This gives stainless steel 430 an advantage in some demanding application scenarios, such as automotive parts, kitchen utensils and so on.
Stainless steel 201 has better ductility and plasticity and is easier to process into various shapes. This makes stainless steel 201 more common in some applications that require bending, stamping, and deep-drawing molding, such as metal parts in manufacturing, furniture, etc.
There are also differences in the thermal and electrical conductivity of stainless steel 430 and 201. Stainless steel 430 has a low thermal and electrical conductivity, while stainless steel 201 has a relatively high one. This makes stainless steel 430 more suitable for certain heat-sensitive applications, such as the housing of electronic equipment.
Application
Due to the differences in the chemical composition and physical properties of stainless steel 430 and 201, they also have some differences in the field of application. Stainless steel 430 is often used for automotive parts, building structures, kitchen utensils, etc. due to its high hardness and strength. Its wear-resistant properties make Stainless Steel 430 perform well in applications that need to withstand high strength and frequent use. Stainless steel 201 is often used in manufacturing metal parts, furniture, decorative items, etc. due to its good ductility and plasticity. Its easy processing characteristics make stainless steel 201 more common in the need for various shapes processing occasions.
FAQ
201 stainless steel is not food-grade stainless steel. 201 steel has a lower chromium and nickel content and a higher manganese and carbon content. Food-grade stainless steel usually has a high chromium and nickel content, as well as a low manganese and carbon content, and this combination of components can effectively prevent bacterial growth and corrosion, ensuring food safety and hygiene.
201 Stainless Steel is not magnetic. 201 is an austenitic stainless steel and its internal structure is not magnetically conductive and therefore cannot be attracted to magnets. The main composition of 201 stainless steel includes iron, chromium and nickel, but due to its low iron content, it is not magnetic.
201 stainless steel has a certain degree of rust resistance, but its rust resistance is affected by various factors. 201 stainless steel’s main compositions include iron, chromium and nickel, of which the content of chromium is about 18%, and the content of nickel is lower. Chromium will react with oxygen in the air to form a dense chromium oxide film, which can prevent the oxygen inside the steel from coming into contact with moisture, thus preventing rust. However, due to the low content of nickel in stainless steel 201, its rust-prevention ability is relatively weak, especially when in contact with corrosive substances or a harsh environment